NASA is breaking ground in the world of additive manufacturing with the Low Cost Upper Stage-Class Propulsion project. Recently, the agency successfully hot-fire tested a combustion chamber at NASA’s Marshall Space Flight Center in Huntsville, Alabama made using a new combination of 3-D printing techniques.
“NASA continues to break barriers in advanced manufacturing by reducing time and costs involved in building rocket engine parts through additive manufacturing,“ said John Fikes, project manager for the Low Cost Upper Stage-Class Propulsion Project. “We are excited about the progress of this project. We demonstrated that the E-Beam Free Form Fabrication produced combustion chamber jacket can protect the chamber liner from the pressures found in the combustion chamber.”
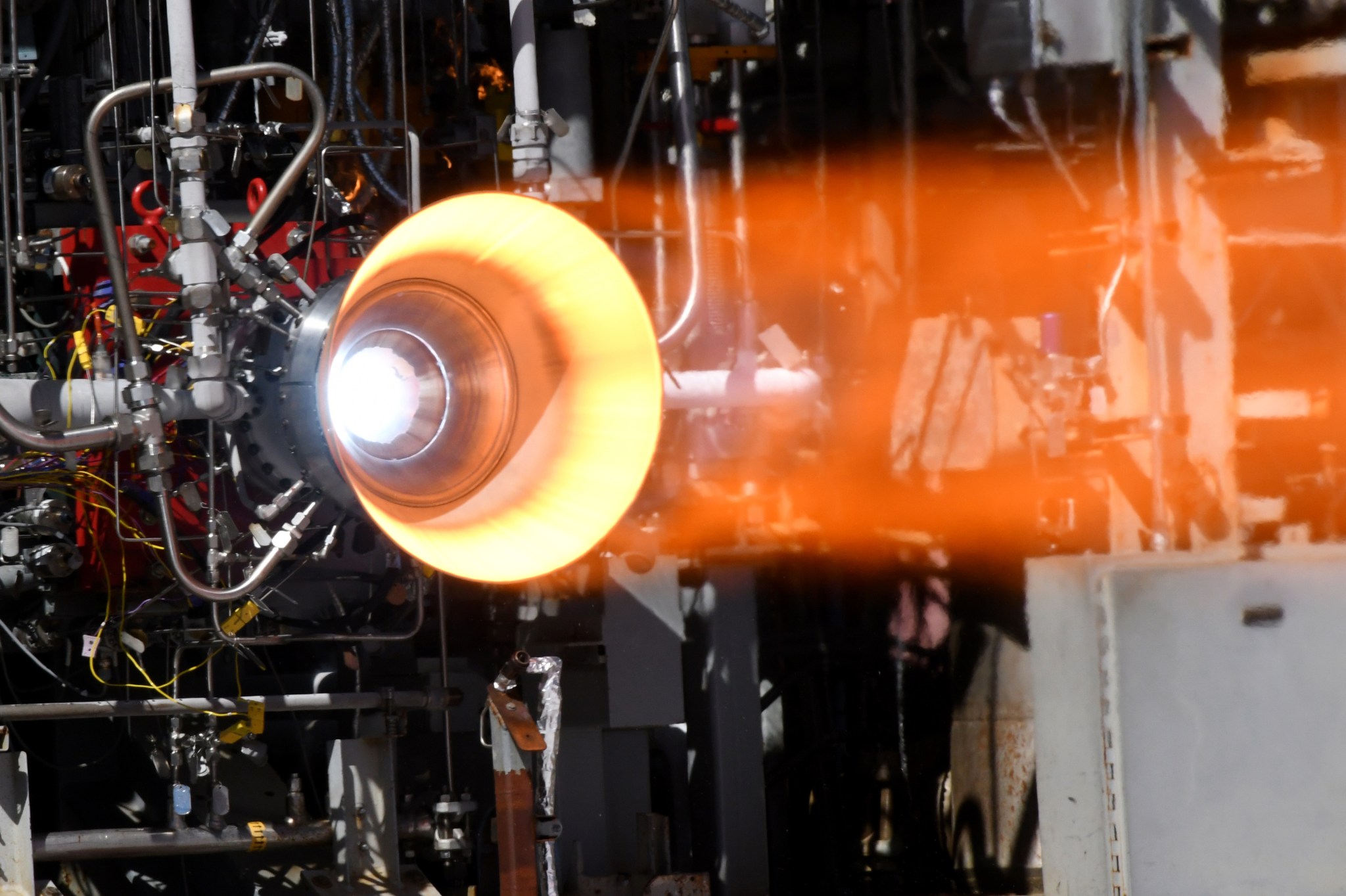
The project is a joint effort by three NASA centers – Glenn Research Center in Cleveland, Ohio, Langley Research Center in Hampton, Virginia, and Marshall. The agency successfully printed the first, full-scale 3-D printed copper combustion chamber liner in 2015 at Marshall using a powdered copper alloy created by material scientists at Glenn. The liner was then sent to Langley where E-Beam Free Form Fabrication Technology, a layer-additive process that uses an electron beam and wire to fabricate metallic structures, was used to deposit a nickel-alloy onto the liner to form the chamber jacket.
While the copper lining is good for thermal conductivity, it is not very strong, therefore it is covered in a nickel-alloy jacket to provide a strong structure that can withstand the stress from the pressure contained in the chamber. This additive manufacturing process eliminates traditional techniques including brazing which enabled the jacket to be made in hours, rather than days or weeks. Additionally, this process produces a single article with increased durability by reducing the multiple parts with welded joints found in traditional manufacturing.
For the just-completed series of tests, the chamber, composed of the liner and the newly added jacket was shipped back to Marshall and installed in a test stand to be fired at various power levels for durations ranging from 2 to 30 seconds under conditions akin to an actual launch. The final test went the full duration of 25 seconds at 100 percent power. The post-test data shows the hardware remained in great shape.
“Testing the chamber in flight-like conditions helps us continue to prove these revolutionary technologies,” said Chris Protz, engineering and design lead for the propulsion project. “We are proud of the way the chamber preformed during this test and the capabilities here at Marshall that allow us to continue paving the way for advancements in additive manufacturing.”
The technology for the liner and jacket will be incorporated into a new project called Rapid Analysis and Manufacturing Propulsion Technology. This project aims to further improve production time and costs for thrust chamber assemblies.
The Low Cost Upper Stage-Class Propulsion Project is funded by NASA’s Space Technology Mission Directorate’s Game Changing Development Program, which seeks to identify and rapidly mature innovative technologies that may lead to entirely new approaches for future space missions.
To view video of the Low Cost Upper Stage-Class Propulsion Project, click here.
For more information about NASA’s Space Technology Mission Directorate, visit: