How in-space manufacturing is bringing change to life on Earth
An average of 22 people die each day in the United States waiting for a donated organ. Upwards of 30 million people worldwide suffer from degenerative retinal diseases. New manufacturing processes are being developed aboard the International Space Station that could help address both issues.
Microgravity provides a unique opportunity for companies to create everything from bioprinted organs to a variety of high quality materials not achievable on Earth. In making the business case, high-demand products that address significant unmet needs or that have a high return on investment are at the top of the list for creation in orbit and return to our planet. It turns out that research at the intersection between biotechnology and medicine, something that seems straight out of science fiction, may fit that bill.
U.S.-based biotechnology company LambdaVision is designing and developing a protein-based artificial retina using a light-activated protein that could replace the function of damaged photoreceptors in the eye. The aim is to restore functional sight in those with blindness caused by retinal degenerative diseases, which include age-related macular degeneration and retinitis pigmentosa. Currently, no cure is available for either of these diseases, representing a significant unmet need to develop a technology to restore meaningful vision to these patients and improve their quality of life.
The ISS National Lab-sponsored Protein-Based Artificial Retina Manufacturing investigation evaluates the use of the protein bacteriorhodopsin in a layer-by-layer deposition process to create thin films that can be inserted into the subretinal space. Those created on station are expected to have better quality and stability than those manufactured on Earth.
“In a microgravity environment, we expect more homogeneous and consistent layering,” said principal investigator Nicole Wagner, president and chief executive officer of LambdaVision. “On Earth, we construct the artificial retina using a layer-by-layer process that is very much subject to the effects of gravity. Manufacturing in microgravity allows us to avoid sedimentation of solutions and aggregation, which can produce thin films with fewer defects, higher homogeneity, and enhanced optical clarity.”
LambdaVision researchers and their implementation partner Space Tango were able to manufacture a 200-layer film in microgravity for the first time — an important step in their studies.
Many commercial manufacturing operations are taking advantage of microgravity’s reduction in errors caused by gravity on Earth. Made in Space Fiber Optics examines fiber optic filament manufacturing in microgravity using a material called ZBLAN, a blend of zirconium, barium, lanthanum, sodium, and aluminum. This optical fiber glass can perform 100 times more efficiently than traditional silica-based fibers, according to the ISS National Lab.
Researchers believe that these optical fibers, used for ultra-high-speed broadband communications and remote sensing, could exhibit far superior qualities when produced in microgravity. Several studies are putting this theory to the test, seeing whether low-Earth orbit can house commercial manufacturing of these fibers for use on the ground.
ISS National Lab sponsored Fiber Optic Production-2 (FOP-2) expands upon earlier work, helping construct a process to aid future manufacturing of high-quality optical fiber of the highest value for commercial businesses.
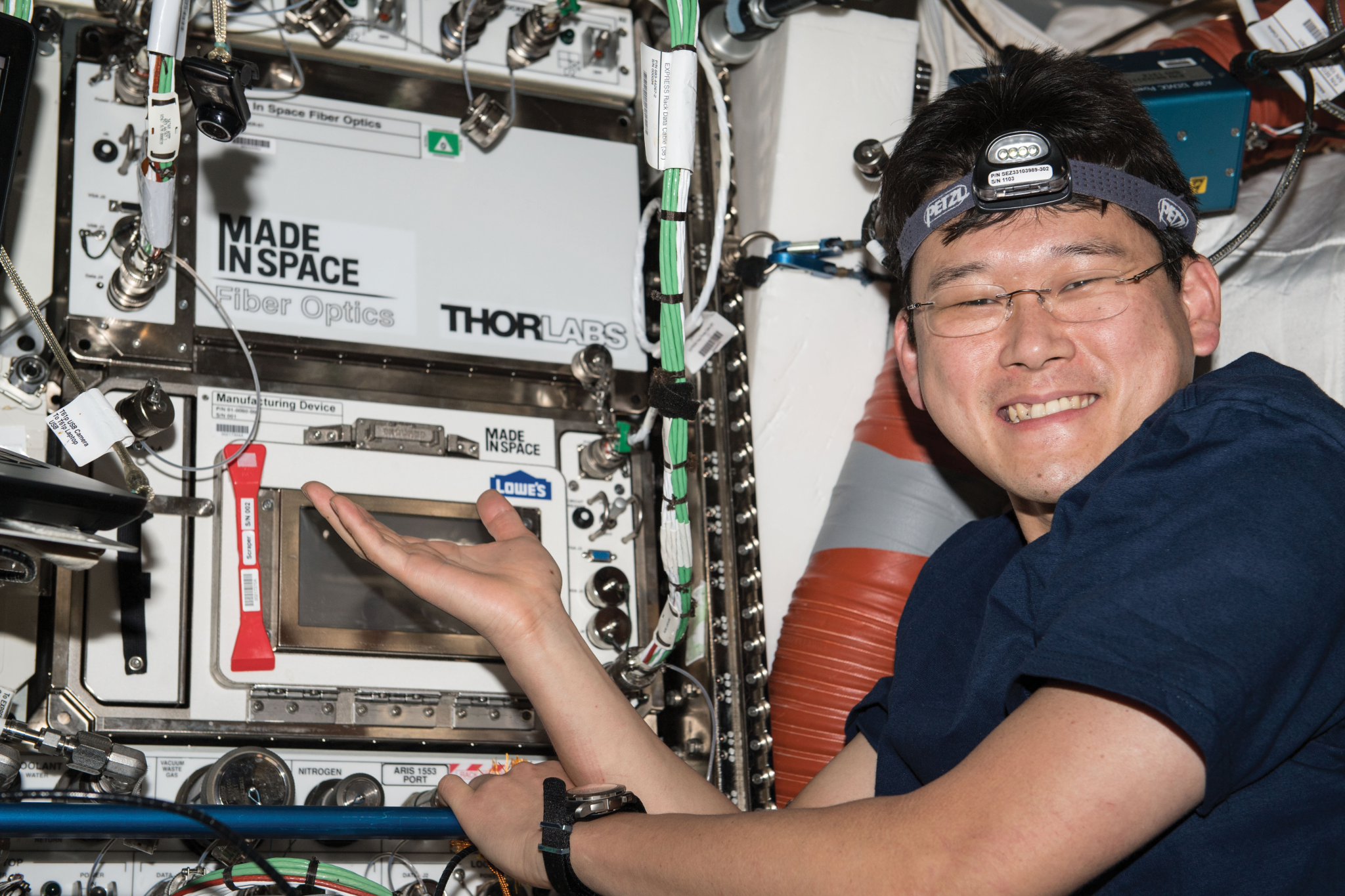
Also returning to Earth from orbit could be actual 3D-printed human cells. Several companies are working toward the creation of human organs using microgravity as a tool. Bioprinting, a subcategory of 3D printing, uses viable cells and biological molecules to print tissue structures. A first-of-its-kind bioprinter launched by Russian state space agency ROSCOSMOS (ROSCOSMOS) in 2018 helped pave the path for research on artificial organ creation. Specialists from Russian company 3D Bioprinting Solutions developed special scientific equipment called 3D MBP, which consists of a magnetic bioprinter, Organ.Aut, and a set of multifunctional transparent cuvettes. Organ.Aut’s capabilities include culturing cartilage cells in space through the use of magnetic fields.
A series of experiments performed on station from 2018-2020 proved the scientific importance of this approach for the creation of tissue constructs (platforms for research), obtaining stable biofilms of bacteria and studying the processes for synthesizing mineral components of bones and crystallizing organic molecules. These results pave the way for the development of innovative treatments that include tissue engineering products and next-generation medicines.
Astronauts currently use the BioFabrication Facility (BFF) to test the creation of biofabricated tissues in microgravity. Techshot, a Redwire company that built and runs the facility, is looking to capitalize on the increased opportunities for commercial businesses in space. Techshot launched BFF in 2019 and since then has been working toward the goal of developing the capability to solve the problem of organ shortage.
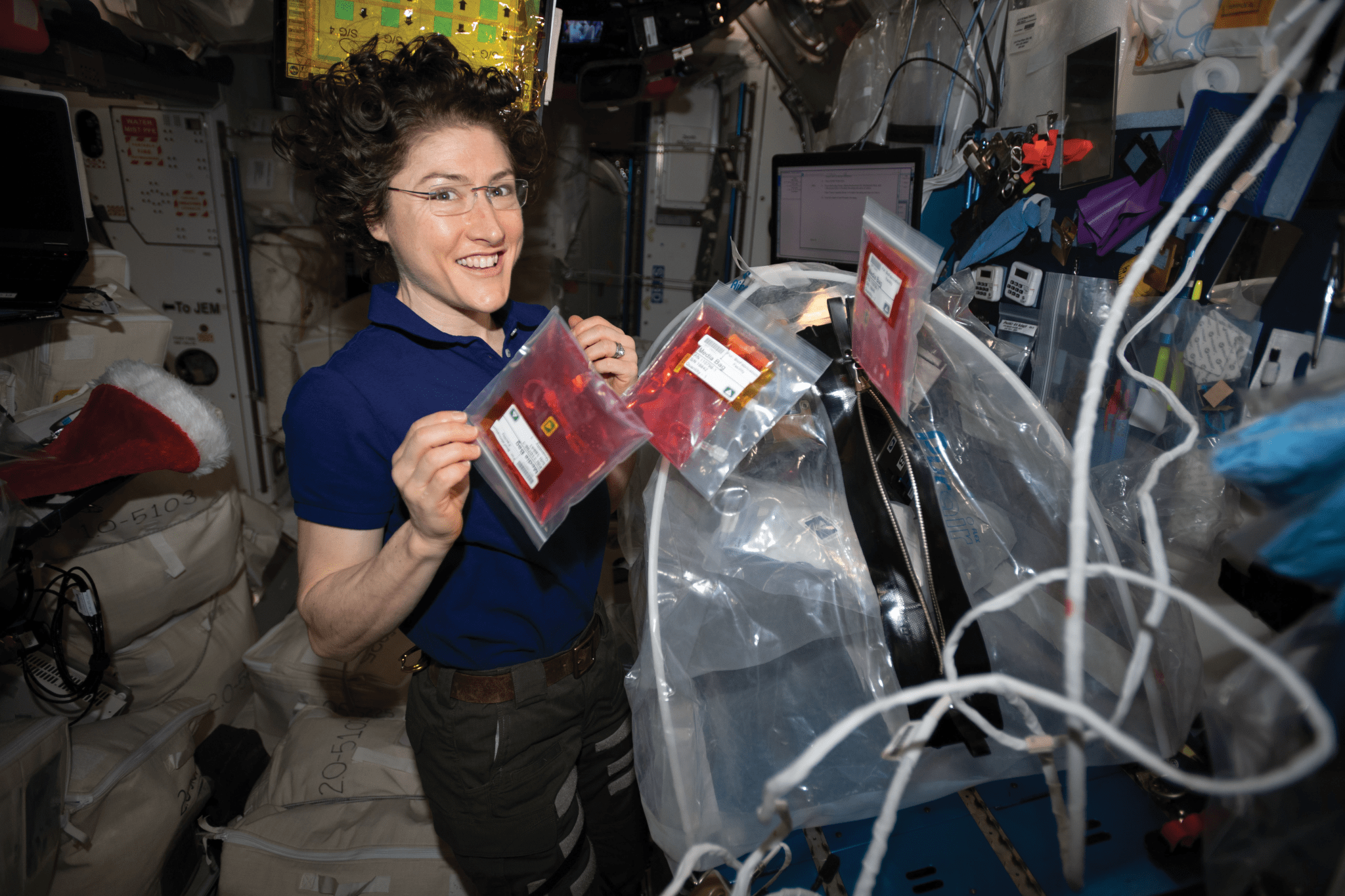
“There will never be a solution available if we don’t take the first step,” says Richard Boling, vice president at Techshot. BFF already has printed multilayer cardiac constructs as well as preliminary test prints of components of a human meniscus.
On Earth, bioprinted constructs either collapse or require chemical thickening treatments, both of which render the cells incapable of replicating human organ tissue. Microgravity makes it possible to print complex multilayer constructs and compile them into tissue with a two-pronged process. First, cells are printed in repetitious layers using the BFF. A second piece of Techshot hardware, the ADvanced Space Experiment Processor (ADSEP), conditions these cells into tissues.
While the focus of this project is better health for those on Earth, these two hardware systems also may play a role in production of food or medicine during deep space exploration.
“We provide the picks and shovels researchers use to make new discoveries and improve life on Earth,” says Boling. “Feed people and heal them, what more would you want to do to benefit humanity? To me, the space industry is less about the rings of Saturn and more about humanity, whether making life better on Earth or extending life to Mars.”
Bioprint FirstAid, a study from the German Space Agency (DLR), focuses on bioprinting for exploration. It demonstrates a portable handheld bioprinter that uses a patient’s own skin cells to create a tissue-forming patch to cover a wound and accelerate the healing process.
On future missions to the Moon and Mars, bioprinting such customized patches could help address changes in wound healing that can occur in space, which complicates treatment. Extracting an individual’s cells before a mission could enable more immediate response to injury. Similar 3D printing technology could help address another issue with long-duration spaceflight: limits on the ability to predict every tool or object needed for missions beyond the lunar surface. One way to avoid “over packing” is to bring technology to create any fixture the crew may need during the spaceflight.
The first 3D printer in microgravity, a plastic-based machine, arrived on station in 2014. Developed by Redwire Space (formerly Made in Space), the machine combined heat with the plastic in a singular-layering process to manufacture objects on demand.
The 3D Printing In Zero-G experiment opened the door to this possibility by demonstrating that a 3D printer works normally in space. The Italian Space Agency (ASI) and NASA also collaborated on the Portable On Board Printer 3D experiment, which further paved the way for printing on station. Now hundreds of samples have been created using multiple printing facilities.
In general, these printers extrude streams of heated plastic, metal, or other material, building layer on top of layer to create three-dimensional objects. Testing this process using relatively low-temperature plastic feedstock on the space station was an important first step toward establishing an on-demand fabrication capability for deep-space crewed missions and in-space manufacturing.
Minimizing waste is of the utmost importance aboard the space station and will be crucial on long-duration missions. NASA’s Refabricator, the first 3D Printer integrated with a recycler aboard station, recycles plastic waste into high-quality 3D printer filament. Successfully demonstrating sustainable manufacturing, repairing, and recycling is a key initiative for NASA.
The Redwire Regolith Print (RRP) demonstration took this concept to the next level by examining an entirely different kind of feedstock for 3D manufacturing on the orbiting laboratory: regolith. This dust, present on the surface of the Moon and other planetary bodies, could provide raw materials for construction of habitats and other structures. Using regolith would reduce how much material must be launched on future missions.
Exploring the next frontier of manufacturing off the Earth gives commercial partners the opportunity to explore the capabilities of production in microgravity for use on Earth and on long-duration space missions. As with many advanced scientific concepts relating to space, the space station seemed like a fictional concept in the mid-20th century. Now it is bringing to reality futuristic ideas for manufacturing.
Additional resources:
ZBLAN continues to show promise
Exotic Glass Fibers From Space: The Race to Manufacture ZBLAN