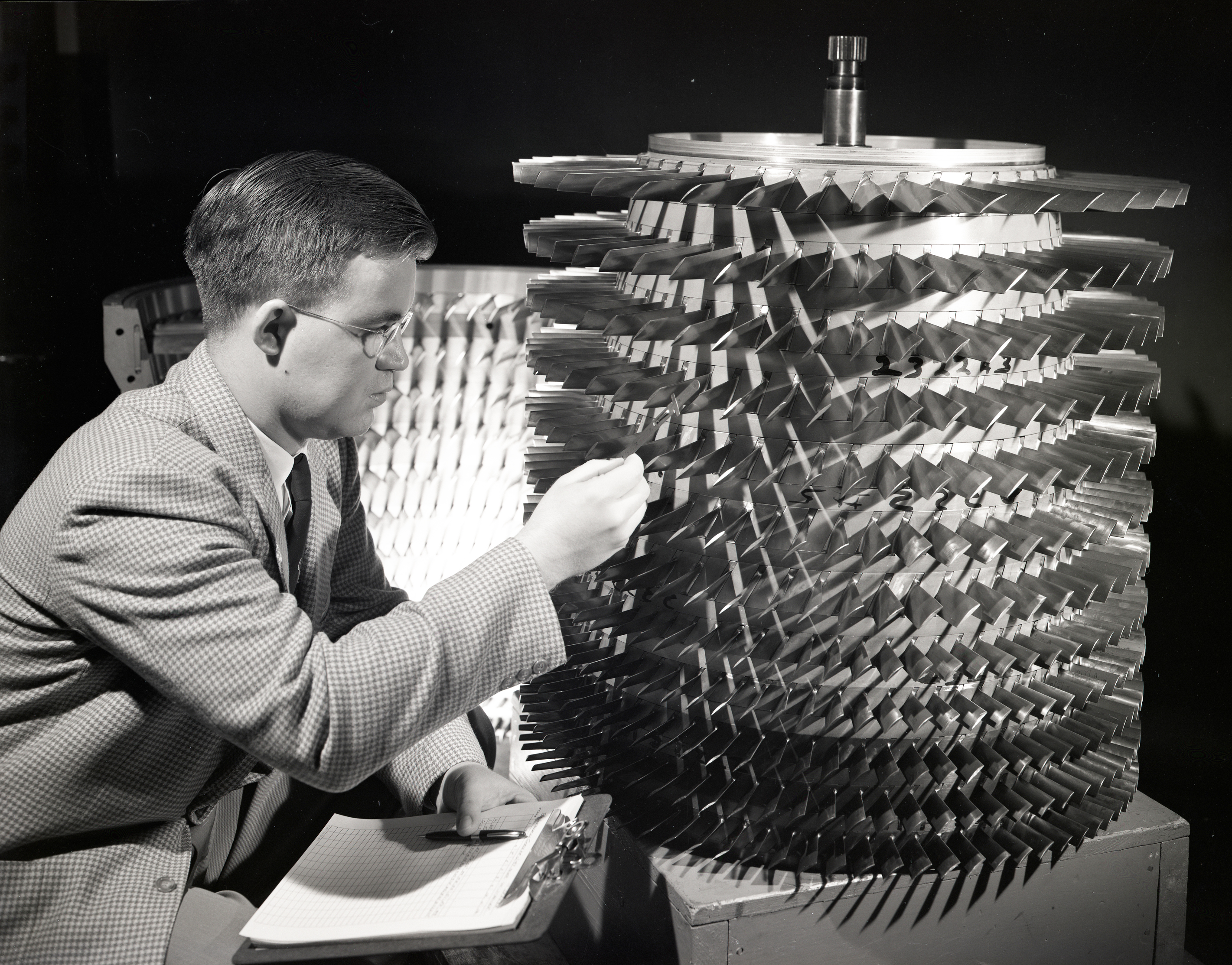
NACA Engineer Measures 12-Stage Axial Flow Compressor Blades
A researcher measures the blades on a 12-stage axial-flow compressor at the National Advisory Committee for Aeronautics (NACA) Lewis Flight Propulsion Laboratory in Cleveland, Ohio. The earliest jet engines in the late 1930s employed centrifugal compressors which compressed the air flow with a finned rotating disk. The centrifugal engines were efficient enough to power contemporary aircraft but were ultimately limited by the need to increase the compressor’s diameter in order to increase the engine’s power. Axial-flow compressors used a series of fan-like stages to compress the air flow. Additional stages could be added in line with one another to increase power without increasing the diameter of the engine. By the late 1940s the axial-flow compressors were found in every new turbojet model. The Compressor and Turbine Division at the NACA Lewis laboratory was dedicated to improving the design of axial-flow compressor engines. The engineer in this photograph is measuring the stator blades on a vertically-positioned 12-stage axial-flow compressor. The countless studies at Lewis in the 1940s and 1950s covered blade shapes, compressibility, fatigue, thrust augmentation, and full-scale engine tests. The studies were conducted in wind tunnels, on test stands and dynamotors, and rigs built for a single or multiple compressor stages. One of the most significant outcomes of the Lewis research was the transonic compressor. The Lewis engineers designed, built, and tested an 8-stage transonic compressor to verify their theoretical predictions on transonic air flow. The group continued working on the problem by creating additional single-stage and then multi-stage compressors and integrating them into advanced turbojet engines. The Lewis researchers were able to demonstrate that there were no preexisting theoretical limitations to compressor design. Instead, performance could be continually increased with proper design methods.
- X