The word “qualification” has become quite synonymous with testing and building the world’s most powerful rocket, NASA’s Space Launch System, which will make missions possible to an asteroid and the journey to Mars.
So, what does it mean for rocket parts to be “qualified” for the mission of going to deep space? And how does that fit in to being ready for that first, uncrewed flight of SLS with the Orion spacecraft in late 2018?
“When you’re building a rocket, there’s a whole flight certification process, and qualification is an important part of that,” said Garry Lyles, SLS chief engineer at NASA’s Marshall Space Flight Center in Huntsville, Alabama. “It proves the hardware meets the requirements and performs the way it is designed to do. We want to test like we fly.”
The Process to the Pad
Setting requirements is the first step in the flight certification process and essentially answers the question of what the rocket is being built to do. For SLS, the vehicle has requirements to send humans on deep-space missions, including the journey to Mars.
The next step is designing the rocket, and then construction begins before the next step of qualification testing. And that includes building flight hardware.

“NASA’s modeling techniques are extremely mature and have been developed over many, many years,” said Lyles. “A lot of our qualification is done by modeling and analysis, with big margins for safety and other factors. This gives NASA the confidence to go ahead and build flight hardware.”
Lyles says a common misconception about qualification testing is that it means the hardware and systems are “go” for flight. While qualification testing shows various parts of the rocket perform as predicted, NASA still has to integrate and test key elements of the rocket that work together during various phases of the mission.
“After qualification testing, there’s still work to be done,” Lyles said. “We do acceptance tests, like ‘green’ run, where the core stage and engines will be integrated and fired up together, just like they will operate during a launch.”
Green run testing at NASA’s Stennis Space Center near Bay St. Louis, Mississippi, will occur closer to the launch date, which is scheduled no later than November 2018.
“While the RS-25 engines have been previously certified, they do have some new parts, including the engine controller, and we have to qualify those pieces for flight,” Lyles added. “And we want to make sure the different parts of the rocket, like the core stage and engines, work together as designed.”
A countdown rehearsal, a type of validation test, will happen before SLS lifts off from the launch pad at NASA’s Kennedy Space Center in Florida. Engineers will load the rocket with propellant, drain it, and ensure all the ground systems equipment and processes are in place for that maiden flight.
Along with testing and rehearsals, SLS has another program milestone to clear – design certification review. Already passing preliminary design review and critical design review, the rocket will be certified that it meets all design requirements. It will then proceed to the integrated test, checkout and flight readiness review.
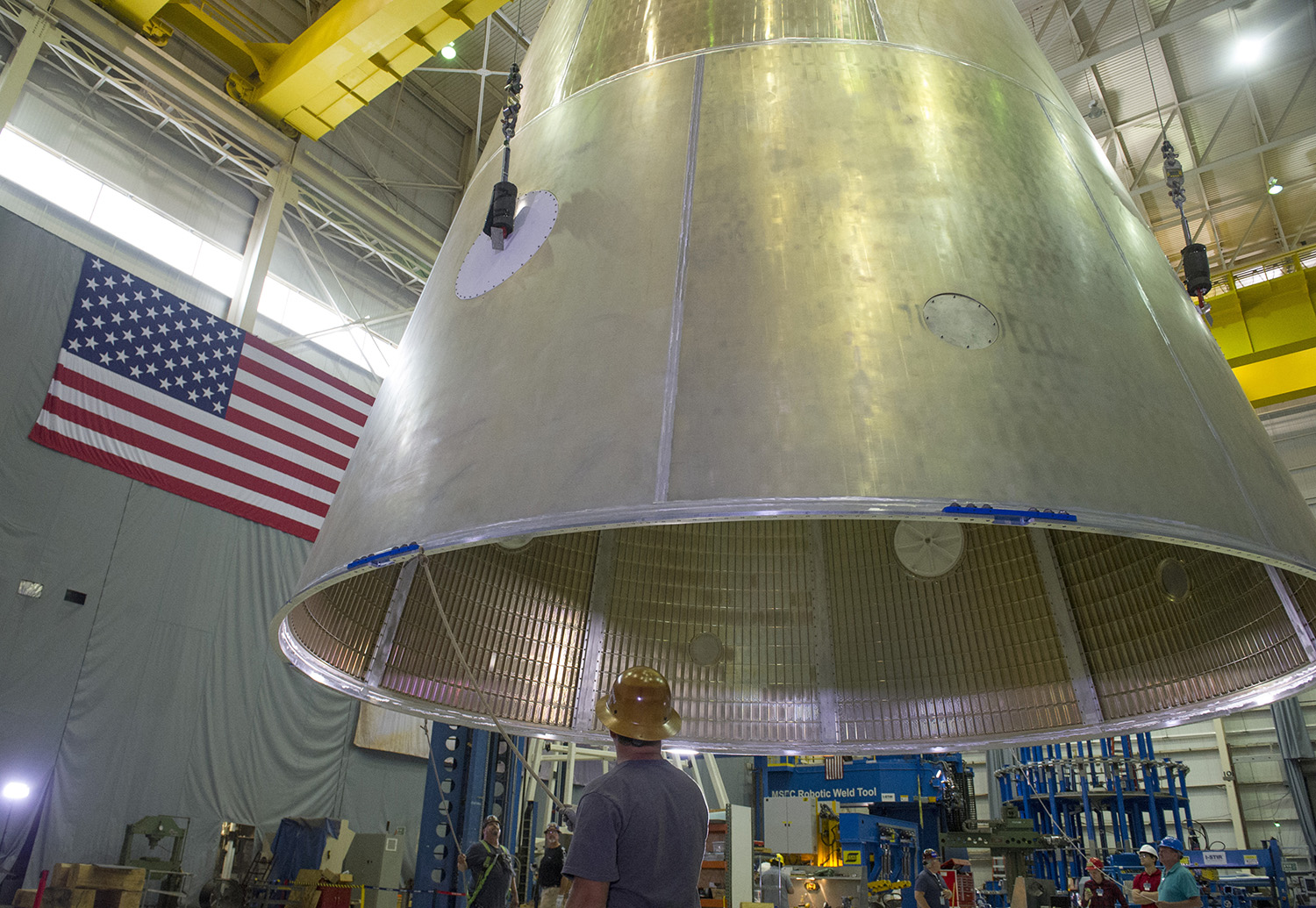
“We have come a long way since the beginning of this program in 2011, and it’s the first time in almost 40 years a human-rated rocket has passed critical design review,” said SLS Program Manager John Honeycutt. “I am confident that this vehicle has the capabilities to take us on human exploration missions that have never been accomplished before, and it’s exciting for me, and our workforce, to be a part of that story.”
The initial SLS configuration will have a minimum 70-metric-ton (77-ton) lift capability and be powered by twin solid rocket boosters and four RS-25 engines. The next planned upgrade of SLS will use a more powerful exploration upper stage for more ambitious missions with a 105-metric-ton (115-ton) lift capacity. A third configuration will add a pair of advanced solid or liquid propellant boosters to provide a 130-metric-ton (143-ton) lift capacity. In each configuration, SLS will continue to use the same core stage and four RS-25 engines.
For more information on SLS, visit:
Kim Henry
Marshall Space Flight Center, Huntsville, Ala.
256-544-0034
Kimberly.m.henry@nasa.gov