The road to launch wasn’t always smooth, but the scientists and engineers who built the Dellingr spacecraft proved they could develop a more capable and resilient CubeSat platform, and in the process, advance the state-of-the-art in this increasingly more important mission class.
For the group’s efforts, the Office of the Chief Technologist at the Goddard Space Flight Center in Greenbelt, Maryland, awarded its IRAD (Internal Research and Development) Team Award to the engineers and scientists who created and now operate Dellingr and its payloads, including an advanced time-of-flight Ion-Neutral Mass Spectrometer, or INMS, two miniaturized magnetometer systems, a release mechanism called DANY, short for Diminutive Assembly for Nanosatellite Deployables, and a miniaturized thermal-control technology.
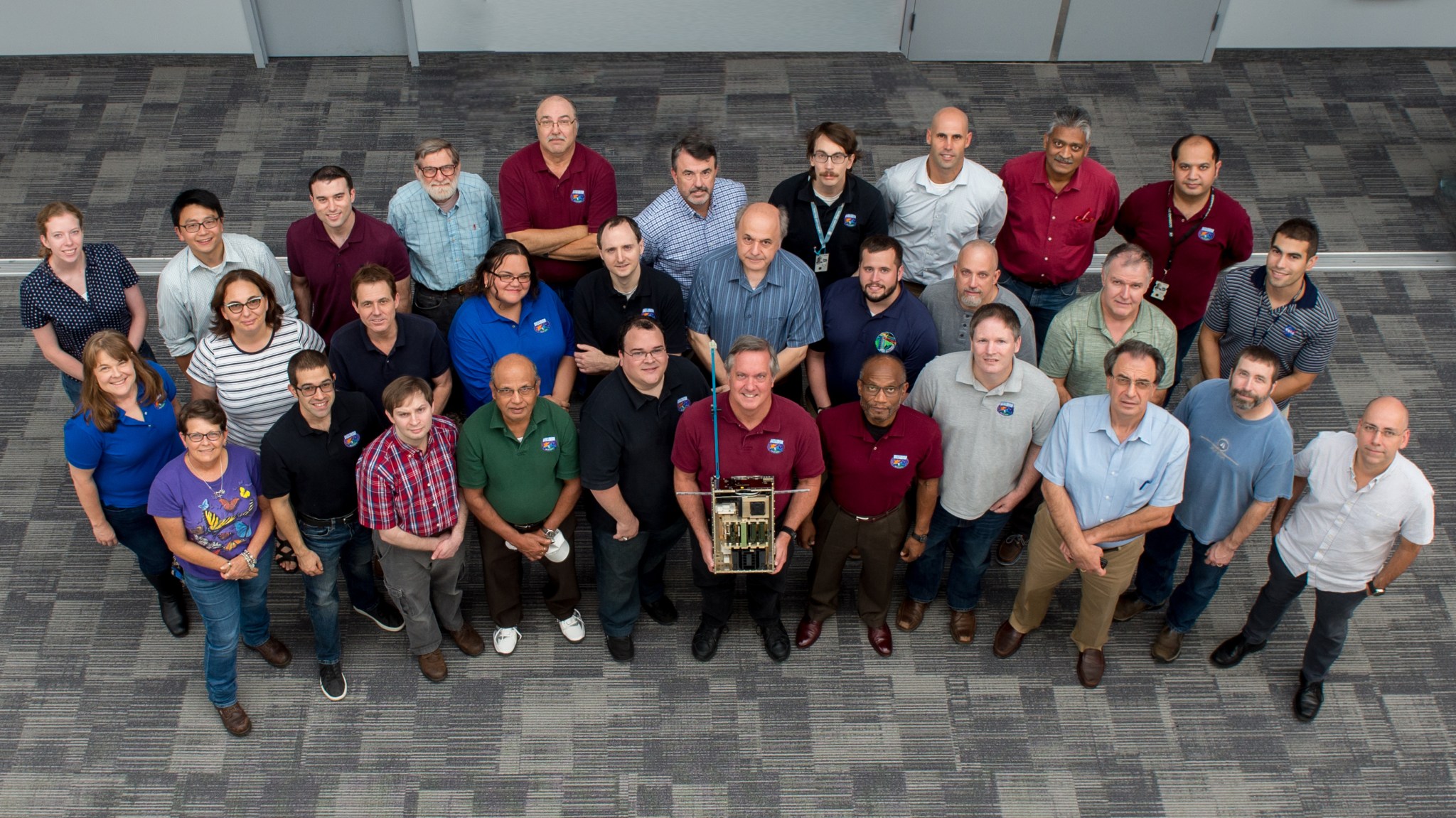
The office bestows the award annually on those who demonstrate the best in leading-edge research and development.
Since Dellingr’s deployment from the International Space Station in November 2017, the shoebox-sized spacecraft and its miniaturized science and engineering payloads have demonstrated new capabilities and gathered high-quality data about the densities of ionized atom species in Earth’s upper atmosphere.
Just as important, lessons learned from the Dellingr effort retired considerable cost and schedule risks for future SmallSat missions. It matured the skills of Goddard personnel and contributed to the win of three additional CubeSat missions, including petitSat, GTOSat, and BurstCube, said Michael Johnson, the chief technologist of Goddard’s Engineering and Technology Directorate and one of the Dellingr project founders. Efforts are now underway to create a follow-on SmallSat architecture — DellingrX — which will extend capabilities beyond CubeSats and be capable of operating outside the relatively benign radiation environment found in low-Earth orbit.
“When our team began developing Dellingr about four years ago, the goal was to build a relatively inexpensive and more reliable CubeSat platform. The goal was to advance the state-of-the-art in small-satellite capabilities,” said Goddard Chief Technologist Peter Hughes, in announcing the award [Goddard press release]. “Despite a tight budget and aggressive schedule, this team accomplished this and more. The team inaugurated a new era for scientists wanting to use small, highly resilient satellites to carry out important, and in some cases, never-before-tried science.”
Driven by Need
The quest to build a less-expensive, more resilient CubeSat platform was driven in response to growing interest among NASA and other government scientists. They sought a low-cost platform on which to fly instruments, as well as the ability to fly constellations of these tiny craft to gather simultaneous, multi-point observations — a technique not financially possible with more traditional spacecraft.
Unfortunately, many low-cost commercially available CubeSat platforms, subsystems, and components used by universities mainly for classroom instruction could not support NASA-class science.
Developing a new platform, however, proved challenging. The team had planned to use commercial components to reduce costs but getting the parts to play well together required additional engineering and technical effort. The team learned that to minimize costs, it also had to change the way it managed CubeSat missions, eliminating or modifying some standard processes and tests.
System Approach
“Resilience is just as important as reliability,” Johnson said. With larger missions, designers incorporate redundant systems in the event of a system failure. Small satellites, however, typically don’t have the resources to support backup systems. “It’s easier to design in redundancy,” Johnson added. “It’s more difficult to build single-string systems that will work even if something goes wrong. You really have to look at the challenge from a system perspective. The CubeSat has to work as a resilient unit.”
As a result, the team had to think differently, leveraging its knowledge of ground and flight systems and the power of software to correct problems should they occur on orbit.
That philosophy proved vital shortly after Dellingr was deployed. The platform’s command-and-data-handling subsystem experienced an upset and began rebooting every 64 seconds for 10 days. One of the team’s engineers, Behnam Azimi, however, had incorporated a hardware capability that allowed Dellingr to recover from the terminal loop, which the team ultimately traced to a one-line bug in a vendor-supplied software driver, Johnson said.
Innovative thinking was also on display shortly after ground controllers recovered Dellingr from the reset loop. Due to a bug in the attitude-control system, which includes torquers and reaction wheels that rotate a satellite in small amounts, the spacecraft began to spin, preventing the INMS from collecting data.
Unable to slow down the spacecraft with the existing attitude-control system, the team wrote a new software application, uploaded it, and used one of Dellingr’s two miniaturized onboard magnetometers as an attitude sensor, which provided data needed to activate Dellingr’s torquers to help stabilize the spinning.
“Thanks to the heroic efforts of the Dellingr team, the spacecraft recovered from a fast spin, tumbling once every five seconds, to once every 50 minutes,” said INMS Principal Investigator Nick Paschalidis. The instrument team turned on the instrument’s ion mode and collected mass spectra for hydrogen, helium, and oxygen. “We have collected excellent data,” Paschalidis said.
The now patented and licensed DANY, which released Dellingr’s magnetometer boom and UHF antenna, also “worked perfectly and is a huge success,” said Dellingr Project Manager Chuck Clagett. And Principal Investigator Allison Evans also reported success with her CubeSat Form Factor Thermal Louver Experiment, a miniaturized thermal-control system involving louvers that open or close depending on whether heat needs to be conserved or shed. The louvers opened when they sensed heat and closed when they didn’t.
Meanwhile, Eftyhia Zesta, the principal investigator on the two magnetometer systems, is still analyzing her data, but considers the flight of the two miniaturized magnetometer systems a success onto themselves.
“The team has tackled issues head on, is collecting and analyzing data, and has moved CubeSat capabilities from rudimentary, unreliable spacecraft to highly capable science platforms, all while enhancing workforce skills,” Hughes said. “I think we’ll be enjoying the fruits of the team’s labor for years to come.”
For more Goddard technology news, go to: https://www.nasa.gov/wp-content/uploads/2018/10/fall_2018_final_web_version.pdf?emrc=2fb7a2
By Lori Keesey
NASA’s Goddard Space Flight Center