To launch the Artemis I Moon mission, NASA’s powerful Space Launch System (SLS) rocket must go from 0 to more than 17,000 miles per hour. The rocket’s flight software and avionics systems control all that power to ensure the rocket and NASA’s Orion spacecraft make it to space. The SLS avionics and flight software came a step closer to the Artemis I mission when NASA certified the Systems Integration Laboratory for final integrated avionics and flight software testing Nov. 14.
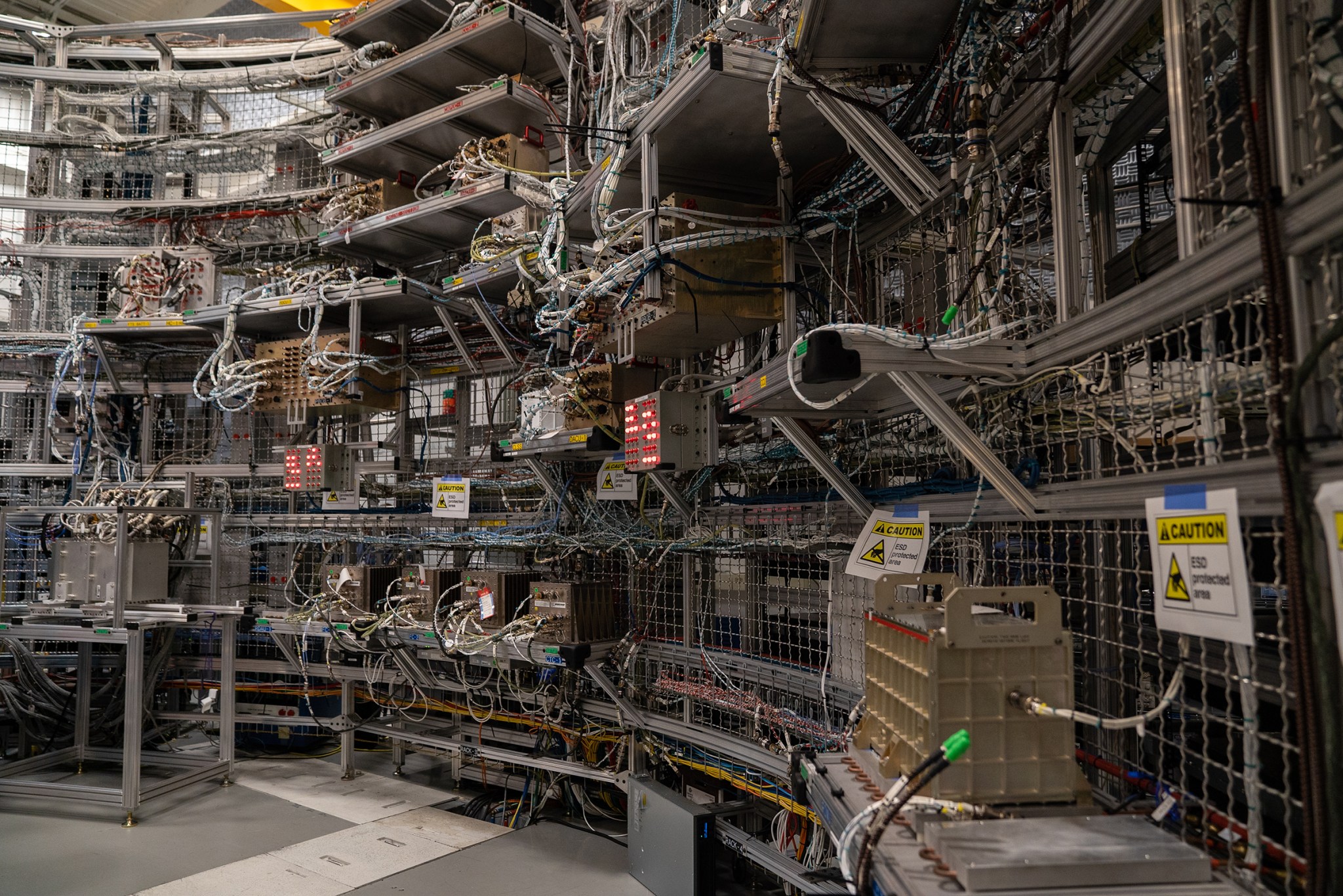
“The System Integration Lab’s test environment is the most accurate representation of the rocket’s entire avionics and software system,” said Dan Mitchell, lead SLS integrated avionics and software engineer. “Certification means the lab has completed a series of tests and analyses to assert that the facility, its simulation environment and the avionics and flight software have been properly integrated and ready for formal system verification testing.”
This lab at NASA’s Marshall Space Flight Center in Huntsville, Alabama, not only includes the flight computers and avionics identical to the core stage avionics but also includes emulators for the rocket’s boosters and engines, the Launch Control Center and Orion. Now that the lab is ready, software engineers can test the software both under normal and unplanned scenarios.
Using unique software programs, engineers in the lab create real-time launch vehicle simulations for the rocket’s extensive and incredibly intricate flight software and avionics hardware. These simulations include numerous nominal and off nominal real-time pre-launch and ascent SLS mission scenarios.
Equipped with two propellant tanks that can hold a combined 733,000 gallons of fuel and four RS-25 engines, the 212-foot-tall core stage serves as the powerhouse of the rocket. The core stage, along with the two, five-segment solid rocket boosters, produces more than 8.8 million pounds of thrust to launch it and NASA’s Orion spacecraft to the Moon.
The internal flight software and avionics outfitted throughout the boosters and core stage operate with three SLS flight computers and interface with the avionics systems to control all that power and safely guide the rocket beyond Earth’s orbit. The software also works with software for the Exploration Ground Systems team at NASA’s Kennedy Space Center in Florida, from where SLS will launch.
“The flight software and avionics systems are considered the brain and nervous system of the rocket,” Mitchell said. “They control the rocket from launch through the first eight minutes of flight, and the test scenarios we create in the lab can simulate any part of an SLS rocket’s launch or even the entire mission.”
In the same room as the lab, the Software Integration and Test Facility integrates and tests hardware for the avionics systems in the core stage of the rocket. These two facilities provide a comprehensive scope of the rocket’s “internal organs” as teams of engineers run hundreds of virtual launches to verify the rocket’s thousands of functional lines of code to evaluate how it will perform in space.
The facilities contain a complete set of avionics and software for the rocket’s core stage, boosters and engines to support end-to-end avionics and software system testing.
“Across the lab in roughly the same positions as they would be inside the core stage, SLS avionics boxes are mounted around a cylinder frame that matches the size of the rocket,” said Lisa Espy, SLS core stage avionics lead. “Inside the skeleton of the rocket, the boxes are even connected with the same sized cables and connectors that will be used on the flight vehicle itself.”
With the certification of the lab complete, formal system testing will be conducted in two phases. First, engineers and developers will focus on the critical avionics hardware and software for flight. Following that, testing will be conducted on the engineering and developmental data acquisition hardware and the hardware for the imagery and flight safety systems.
Althought manufacturing hardware generally garners the most attention, development and testing of the flight software are two of the more technically challenging aspects of the rocket’s design.
NASA is working to land the first woman and next man on the Moon by 2024. SLS and Orion, along with the Gateway in orbit around the Moon, are NASA’s backbone for deep space exploration. SLS is the only rocket that can send Orion, astronauts and supplies to the Moon on a single mission.
For more on NASA’s SLS, visit:
Tracy McMahan
Marshall Space Flight Center, Huntsville, Alabama
256-544-0034
tracy.mcmahan@nasa.gov