
NASA’s Commercial Crew Program Press Kit
NASA works with the American aerospace industry through a public-private partnership to launch astronauts on American rockets and spacecraft from American soil.
TODAY
Missions Launched
Month Until Next Crewed Mission
What is commercial crew?
NASA’s Commercial Crew Program is delivering on its goal of safe, reliable, and cost- effective human transportation on International Space Station missions from the United States through a partnership with American private industry. A new generation of spacecraft and launch systems capable of carrying astronauts to low-Earth orbit and the space station provides expanded utility, additional research time, and broader opportunities for discovery on the orbiting laboratory.
At the Station
NASA uses the International Space Station as a critical testbed to understand and overcome the challenges of long-duration spaceflight. As commercial companies focus on providing human transportation services to and from low-Earth orbit, NASA will focus on building spacecraft for deep space missions. With the ability to obtain transportation from Boeing and SpaceX on a fixed-price contract, NASA will use resources to put the first woman and the first person of color on the Moon as a part of the agency’s Artemis missions in preparation for human missions to Mars.
NASA certified SpaceX’s crew system and started regular missions with astronauts to the space station. SpaceX’s Dragon spacecraft launches on the company’s Falcon 9 rocket from Launch Complex 39A at NASA’s Kennedy Space Center in Florida.
NASA and Boeing launched the company’s Crew Flight Test on the Starliner spacecraft in June 2024, to prove its capability to carry astronauts to low-Earth orbit and the orbiting laboratory. The crewed mission follows an end-to-end flight test, known as Orbital Flight Test 2 (OFT-2), that launched on a United Launch Alliance Atlas V rocket from Space Launch Complex-41 on Cape Canaveral Space Force Station in Florida May 19, 2022. If approved, NASA’s Boeing Crew Flight Test mission will pave the way for the agency’s certification of Boeing’s astronaut transportation system for regular missions to the space station.
How is NASA’s Commercial Crew Program different?
NASA’s Commercial Crew Program represents a revolutionary approach to government and commercial collaborations for the advancement of space exploration.
NASA’s Prior Approach for Obtaining Crew Transportation Systems
Since the Mercury program in the early 1960s, NASA used an almost identical operating model to achieve its goals of human spaceflight. This includes the Space Shuttle Program and the American portions of the International Space Station. NASA would identify a need for a crew transportation system, and then the agency’s engineers and specialists would oversee every development aspect of the spacecraft, support systems, and operations plans. A commercial aerospace contractor would build the system, ensuring that it meets the specifications spelled out by the agency. NASA personnel was heavily involved and oversaw the processing, testing, launching, and operation of the crew system to ensure safety and reliability. All of the hardware and infrastructure was owned by NASA.
Commercial Crew’s Approach for Obtaining Crew Transportation Systems
NASA identified a need for a crew transportation system and a broad set of requirements that would be necessary to ensure crew safety. In the case of commercial crew, the need centered around a safe, reliable, and cost-effective means of getting humans to low-Earth orbit, including the International Space Station, and return safely to Earth. Interested companies are encouraged to apply their most efficient and effective manufacturing and business operating techniques. The companies own and operate their hardware and infrastructure. NASA’s engineers and aerospace specialists work closely with the commercial companies, allowing for substantial insight into the development process and offering up expertise and available resources.
A New Model
NASA's Commercial Crew Program is the first time the current commercial model has been implemented at the agency.
Learn More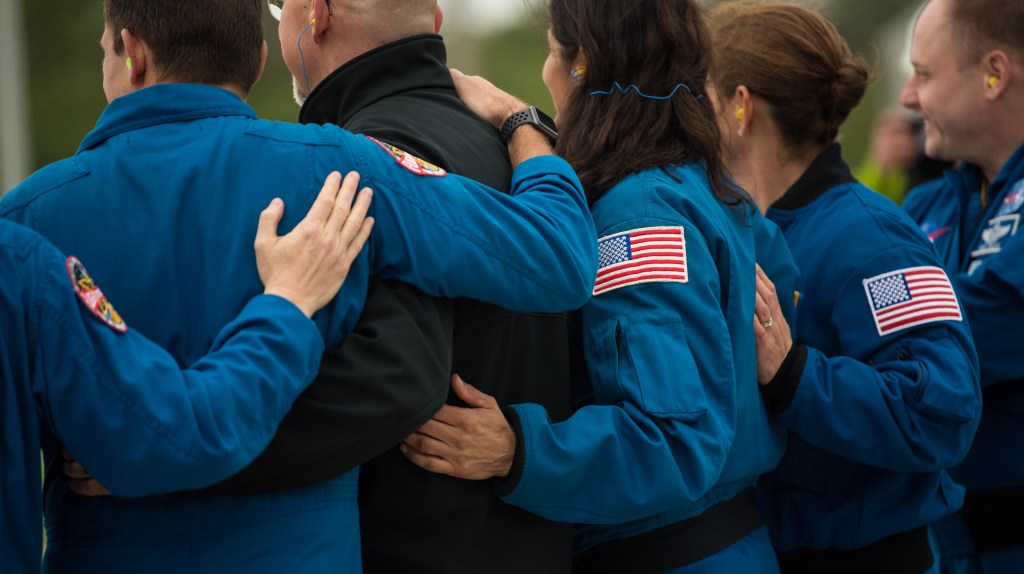
National Investment
NASA, Boeing, and SpaceX, with the help of contractors throughout America, have dedicated countless hours to the agency’s Commercial Crew Program to achieve a common goal: restore our nation’s ability to launch humans to the International Space Station from American soil.
This government-private industry partnership has significant economic benefits, with more than 1,000 suppliers employing workers in all 50 states to support commercial crew spacecraft systems. Contractors apply the most efficient and innovative approaches to launch astronauts back into low-Earth orbit on American-made spacecraft and rockets.
Commercial Crew Timeline
2010
NASA invests about $50 million for Commercial Crew Development Round 1 (CCDev1) to stimulate efforts within the private sector to aid in the development and demonstration of safe, reliable, and cost-effective crew transportation capabilities. The companies include:
- Blue Origin
- Boeing
- Paragon Space Development Corporation
- Sierra Nevada Corporation
- United Launch Alliance
2011
NASA develops partnerships with industry through Commercial Crew Development Round 2 (CCDev2) by awarding nearly $270 million to four companies and providing expertise to an additional three companies to further development and demonstration of safe, reliable and cost-effective transportation capabilities. The agency’s funded agreements are with:
- Blue Origin
- Boeing
- Sierra Nevada Corporation
- SpaceX
The agency’s unfunded agreements are with:
- Alliant Techsystems Inc.
- Excalibur Almaz I
- United Launch Alliance
2012
Commercial Crew Integrated Capability (CCiCap) continues the development of three fully integrated systems in August 2012. The Space Act Agreements call for industry partners to develop crew transportation capabilities and to perform tests to verify, validate and mature integrated designs. Companies include:
- Boeing
- Sierra Nevada Corporation
- SpaceX
2013
Kickoff of the Certification Products Contracts (CPC), is the first of a two-phase certification plan. The three U.S. companies work with NASA to develop data products to implement the agency’s flight safety and performance requirements. This includes implementation across all aspects of the space system, including the spacecraft, launch vehicle, and ground and mission operations. NASA awards a total of about $30 million under the CPC contracts.
Companies include:
- Boeing
- Sierra Nevada Corporation
- SpaceX
2014
Commercial Crew Transportation Capability (CCtCap), the second of a two-phase certification plan for commercially built and operated integrated crew transportation systems, begins. Through its certification efforts, NASA will ensure the selected commercial transportation systems meet the agency’s safety and performance requirements for transporting NASA crew to the International Space Station. NASA awards a total of $6.8 billion under CCtCap contracts.
Companies include:
- Boeing
- SpaceX
2015
NASA names four astronauts as Commercial Crew Cadre to work with Boeing and SpaceX as the companies refine their spacecraft systems. The crew provides invaluable user experience feedback to help shape their hardware and systems to ensure they are ready for flight. NASA astronauts include:
2016
Boeing and SpaceX design and manufacture hardware for testing to ensure their spacecraft can handle the harsh environment of space. The International Docking Adapter is installed on the International Space Station. Two adapters will ultimately serve as the docking points for Boeing’s Starliner spacecraft and SpaceX’s Dragon spacecraft.
2017
Boeing and SpaceX continue development and testing to prepare for emergency situations and ensure human safety. Boeing and SpaceX unveil brand-new spacesuits to be worn by crews while on board each company’s spacecraft.
2018
Testing ramps up and nears completion for Boeing and SpaceX as they prepare their hardware, systems, flight crews and ground support teams for launch.
NASA assigns nine astronauts to crew Boeing and SpaceX’s test flights and first operational missions on the Starliner spacecraft and Dragon spacecraft.
2019
Flight Tests Completed:
- NASA’s SpaceX Demo-1 (March 2-8)
- NASA’s Boeing Pad Abort Test (Nov. 4)
- NASA’s Boeing Orbital Flight Test (Dec. 20-22)
2020
Flight Tests Completed:
- SpaceX In-Flight Abort Test (Jan. 19)
- SpaceX Demo-2 (May 30 – Aug. 2)
Missions Launched:
- NASA’s SpaceX Crew-1 (Nov. 15)
2021
Missions Launched:
2022
Missions Launched:
- NASA’s SpaceX Crew-4 (April 27)
- NASA’s Boeing Orbital Flight Test-2 (May 19)
- NASA’s SpaceX Crew-5 (Oct. 5)
2023
Missions Launched:
2024
Missions Launched:
- NASA’s SpaceX Crew-8 (March 3)
- NASA’s Boeing Crew Flight Test (June 5)
- NASA’s SpaceX Crew-9 (September 28)
Upcoming Missions:
- NASA’s SpaceX Crew-10 (March 2025)
See NASA Launches
Access Full Launch Schedule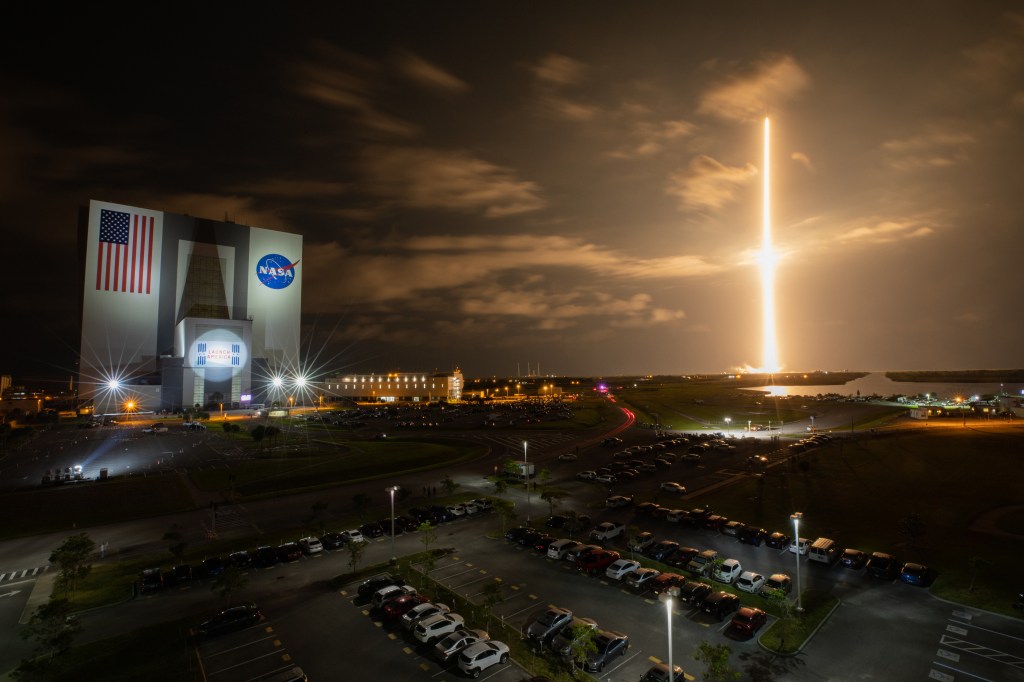
NASA Leadership
Astronaut Training
Astronauts work alongside Boeing and SpaceX to understand the spacecraft, launch systems, and spacesuits, and refine operations in space. Crew members train to live and work aboard the space station. The astronauts learn how to conduct spacewalks, maintain the space station, and perform a myriad of research investigations covering all scientific disciplines.
The astronauts participate in nominal and off-nominal mission simulations, studying every aspect of the spacecraft, as well as launch, in-orbit, and landing procedures to ensure they are prepared for any situation during their mission.
Current Mission
NASA’s SpaceX Crew-9
The tenth flight of the Dragon spacecraft with people as part of NASA's Commercial Crew Program launched Sept. 28, 2024, for a five-month science mission aboard the International Space Station.
Learn More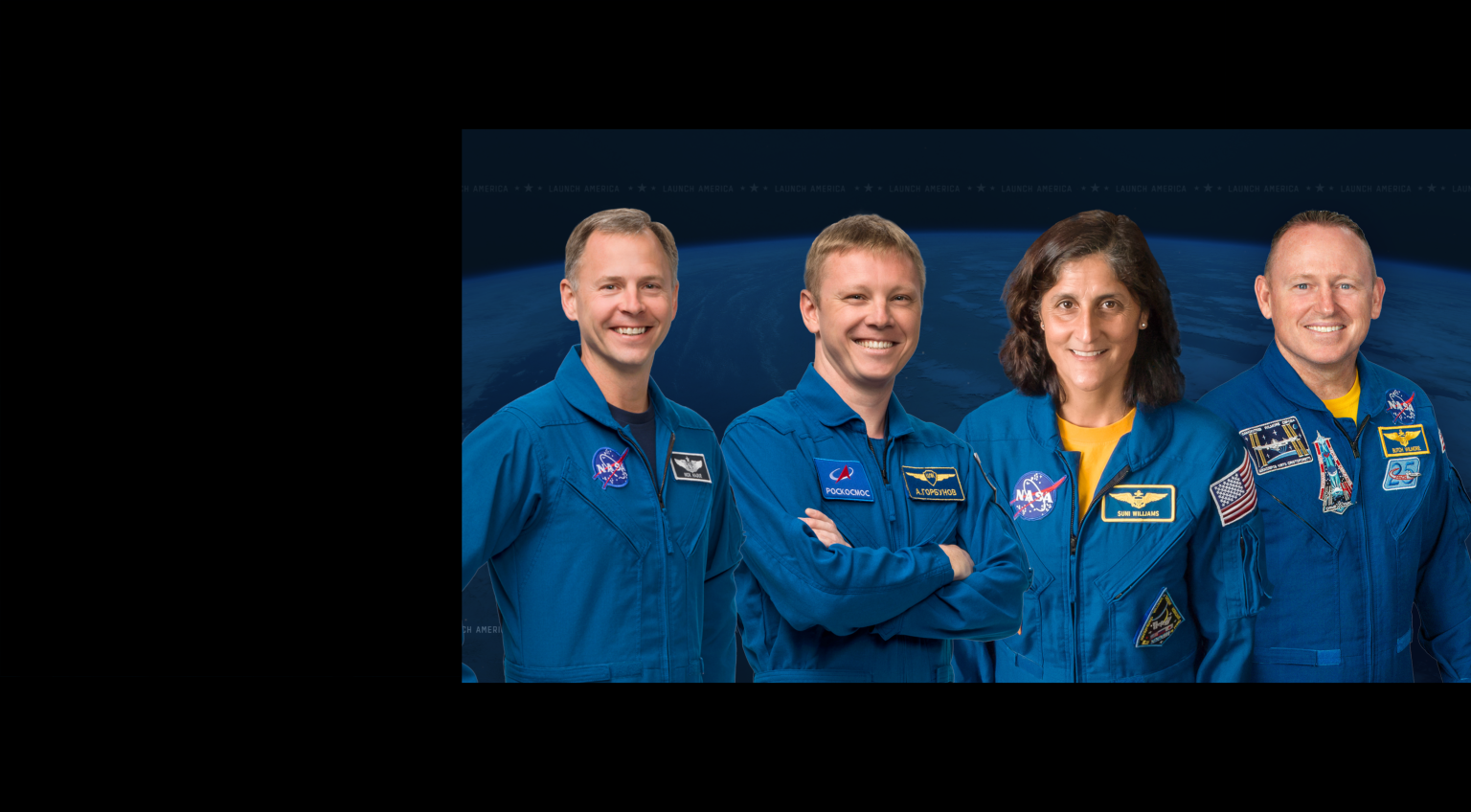
Upcoming Mission
NASA’s SpaceX Crew-10
The 11th flight of the Dragon spacecraft with people as part of NASA's Commercial Crew Program. Launch is scheduled for NET March 2025.
Learn More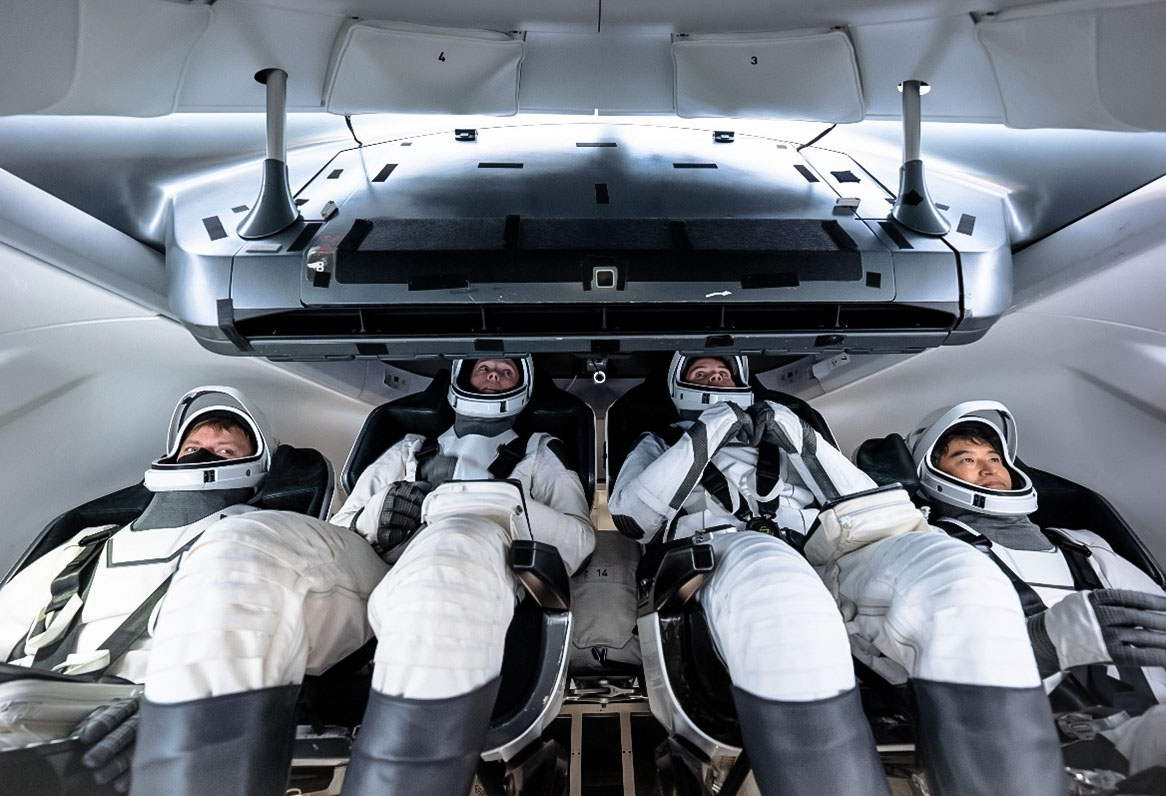
SpaceX Operations
Dragon
Designed with crew and reuse in mind, Dragon is an innovative achievement worthy of the challenge to advance human spaceflight. SpaceX’s Dragon spacecraft has re-established an American human launch capability, flying astronauts regularly to the International Space Station from U.S. soil and increasing use of the orbiting laboratory’s unique research environment.
Dragon is an autonomous spacecraft designed to deliver crew and critical cargo to orbiting destinations. Dragon launches atop a Falcon 9 rocket from Launch Complex 39A at NASA’s Kennedy Space Center in Florida.
As part of NASA’s commercial resupply services contract with SpaceX, the company developed its Dragon cargo spacecraft to carry science and supplies to space, but they designed it with people in mind. For its second commercial resupply services contract, SpaceX delivered an upgraded Dragon cargo spacecraft similar to the Dragon that brings humans to the orbiting laboratory, which also lifts off from Launch Complex 39A at NASA’s Kennedy Space Center.
Dragon Design and Development
SpaceX’s Dragon spacecraft was developed in collaboration with NASA’s Commercial Crew Program. In 2014, NASA awarded Commercial Crew Transportation Capability (CCtCap) contracts to Boeing and SpaceX to each safely and cost-effectively transport astronauts to the International Space Station from the United States.
Dragon is capable of carrying up to seven passengers but carries up to four astronauts for NASA missions, and is designed for water landings. Dragon’s displays provide real-time information on the state of the spacecraft’s capabilities—anything from the spacecraft’s position in space, to possible destinations, to the environment on board. Dragon is a fully autonomous spacecraft that can be monitored and controlled by onboard astronauts and SpaceX mission control in Hawthorne, California.
Dragon is composed of two main elements: the capsule, which is designed to carry crew and critical, pressurized cargo, and the trunk, which is an unpressurized service module. The capsule is subdivided into the pressurized section, the service section and the nose cone, which is opened once on orbit and stowed prior to re-entry.
Near the base of the capsule, but outside the pressurized structure, are the Draco thrusters, which allow for orbital maneuvering. Additional Draco thrusters are housed under the nose cone, along with Dragon’s Guidance Navigation and Control sensors.
Dragon’s trunk provides the mating interface for the capsule to Falcon 9 on its ascent to space. On orbit, half of the trunk contains a solar array, which powers Dragon, and the other half contains a radiator, which rejects heat. Both the radiator and solar array are mounted to the exterior of the trunk, which remains attached to Dragon until shortly before re-entry when the trunk is jettisoned.
Dragon was designed with three windows so passengers can take in views of Earth, the Moon and the wider solar system right from their seats. Dragon has an Environmental Control and Life Support System that provides a comfortable and safe environment for crew members. During their trip, astronauts onboard can set the spacecraft’s interior temperature to between 65 and 80 degrees Fahrenheit.
Dragon features an advanced abort system with eight SuperDraco engines and a series of parachutes that can be activated instantaneously from the moment they are armed on the launch pad all the way through orbital insertion. NASA and SpaceX are capable of supporting seven splashdown sites located off Florida’s east coast and in the Gulf of Mexico. These sites are off the coasts of Pensacola, Tampa, Tallahassee, Panama City, Cape Canaveral, Daytona, and Jacksonville.
In August 2018, NASA announced the first astronauts who would fly aboard Demo-2 and SpaceX’s first operational mission, or NASA’s SpaceX Crew-1. In Demo-2, launched May 30, 2020, NASA astronauts Bob Behnken and Doug Hurley became the first to fly aboard Dragon and returned to Earth 64 days later with a splashdown in the Gulf of Mexico on Aug. 2, 2020.
Following the successful Demo-2 flight test and completion of the agency certification process, SpaceX began regular crew rotation missions to the space station, beginning with NASA astronauts Victor Glover, Mike Hopkins, Shannon Walker, and JAXA astronaut Soichi Noguchi aboard NASA’s SpaceX Crew-1 mission. Crew-1 launched Nov. 15, 2020, and splashed down in the Gulf of Mexico on May 2, 2021. NASA has ordered 14 crew rotation missions to the International Space Station from SpaceX. Crew-1 was the first of these rotation missions.
Falcon 9
Falcon 9 is a two-stage rocket designed and manufactured by SpaceX for the reliable and safe transport of satellites and the Dragon spacecraft into orbit. Falcon 9 is the first orbital class rocket capable of re-flight. Falcon 9 made history in May 2020 when it launched two American astronauts on an American spacecraft from American soil to the International Space Station as part of NASA’s Commercial Crew Program – the first time since the retirement of the Space Shuttle Program in 2011. Falcon 9 has since successfully launched eight more astronauts to the space station for the program.
Falcon 9 began delivering cargo to the International Space Station for NASA in 2012, making SpaceX the first commercial company to visit the station. Falcon 9 went on to make numerous trips to space, delivering satellites to orbit as well as delivering and returning cargo from the space station for NASA, before becoming certified to launch astronauts.
Falcon 9’s first stage incorporates nine Merlin engines and aluminum-lithium alloy tanks containing liquid oxygen and rocket-grade kerosene propellant. After ignition, a hold- before-release system ensures that all engines are verified for full-thrust performance before the rocket is released for flight. Then, with thrust greater than five 747s at full power, the Merlin engines launch the rocket to space. Unlike airplanes, a rocket’s thrust actually increases with altitude; Falcon 9 generates more than 1.7 million pounds of thrust at sea level but produces over 1.8 million pounds of thrust in the vacuum of space. The first-stage engines are gradually throttled near the end of first-stage flight to limit launch vehicle acceleration as the rocket’s mass decreases with the burning of fuel.
The interstage is a composite structure that connects the first and second stages and holds the release and separation system. Falcon 9 uses an all-pneumatic stage separation system for low-shock, highly reliable separation that can be tested on the ground, unlike pyrotechnic systems used on most launch vehicles.
Falcon 9 is equipped with an Autonomous Flight Termination System to be used in the unlikely event that the rocket drifts off course or becomes unresponsive. Carbon fiber landing legs and hypersonic grid fins, all stowed during ascent, are two of the critical elements essential to ensure safe and successful landing of the Falcon 9 first stage.
Technical Overview
- Height: 70 meters or 229.6 feet
- Mass: 549,054 kilograms or 1,207,920 pounds
- Payload to Low Earth Orbit: 22,800 kilograms or 50,265 pounds
- Diameter: 3.7 meters or 12 feet
SpaceX Spacesuit
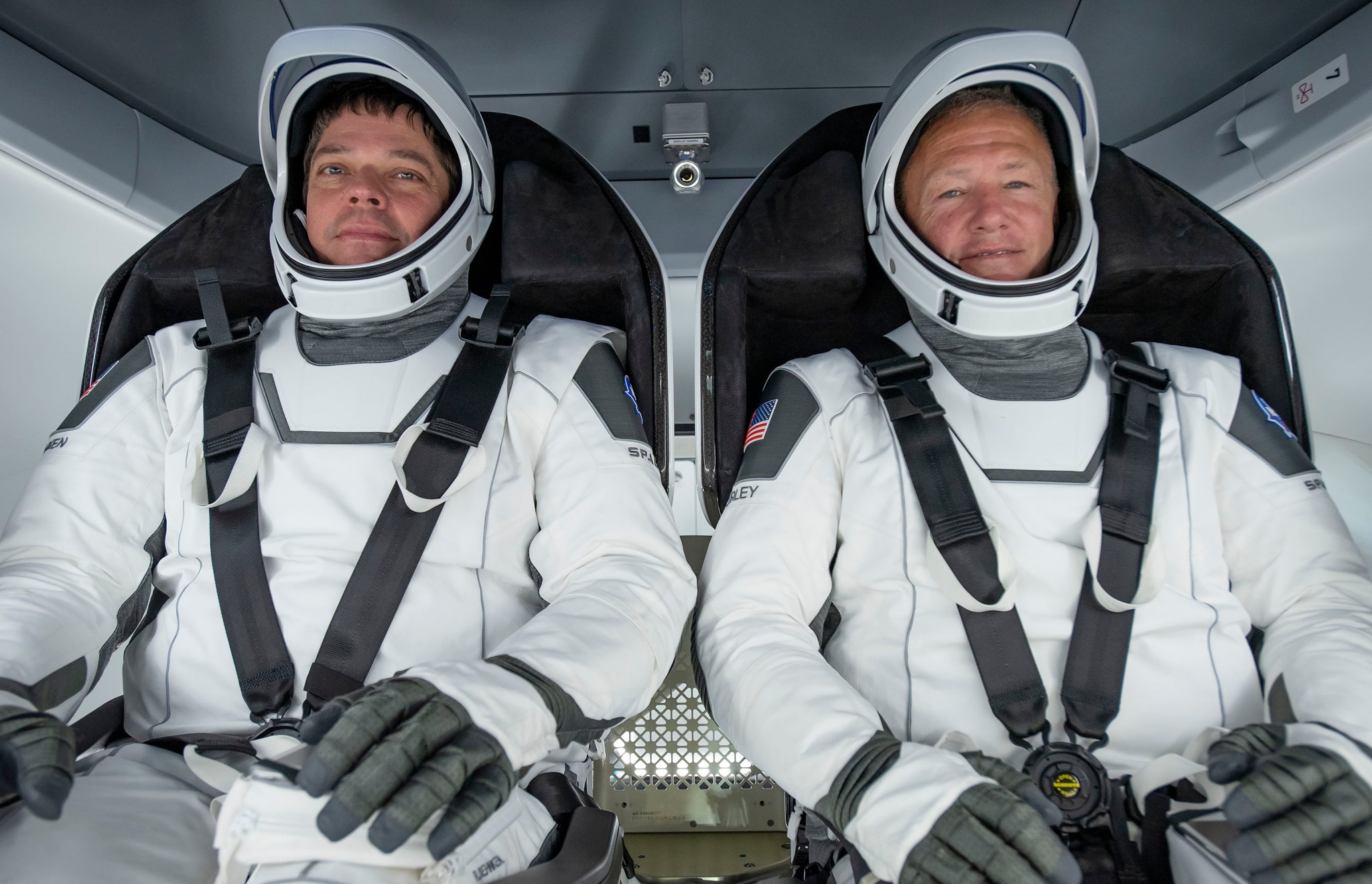
SpaceX designed its spacesuit for astronauts to wear inside the Dragon spacecraft as they fly to and from the International Space Station and to ensure their safety as they operate in low-Earth orbit. The suit is custom-made for each passenger aboard Dragon and is designed to be functional, lightweight, and to offer protection from potential depressurization. A single connection point on the suit’s thigh attaches life support systems, including air and power connections.
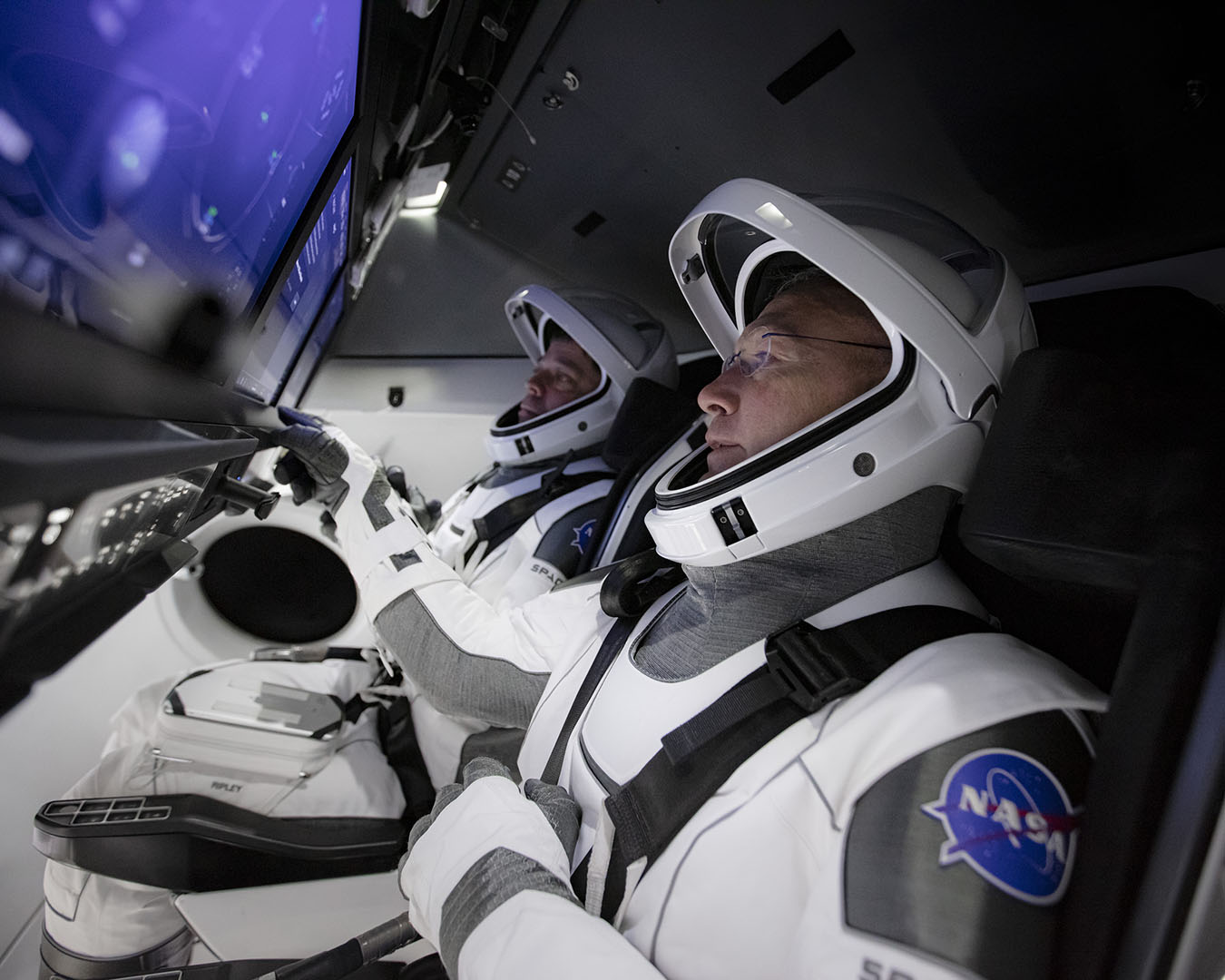
The helmet is custom manufactured using 3D printing technology and includes integrated valves, mechanisms for visor retraction and locking, and microphones within the helmet’s structure. NASA astronauts perform spacesuit fit checks and other testing to prepare for their missions, including pressurized spacesuit tests.
Launch Complex 39A
Launch Complex 39A was built for the Apollo and Saturn V rockets that launched American astronauts to the Moon and back. Since the late 1960s, Pads A and B at NASA’s Kennedy Space Center’s Launch Complex 39 serve as backdrops for America’s most significant human spaceflight endeavors— Apollo, Skylab, Apollo-Soyuz and the space shuttle.
In 2014, Space Exploration Services, or SpaceX, signed a property agreement with NASA for use and operation of Launch Complex 39A for 20 years, a component of Kennedy Space Center’s transition to a multi- user spaceport. SpaceX modified Launch Complex 39A to adapt it to the needs of the company’s Falcon 9 and Falcon Heavy rockets. SpaceX constructed a Horizontal Integration Facility near the perimeter of the pad where rockets are processed for launch prior to rollout to the pad for liftoff.
SpaceX also uses Launch Complex 39A for its crewed Dragon missions to the International Space Station. Standing 212 feet high—more than 20 stories—the company’s transporter erector moves launch-ready rockets and spacecraft from the processing hangar at the base of the pad up to the pad surface and into a vertical position over the flame trench. The transporter erector is larger in size and stronger in comparison to the erector SpaceX uses at Space Launch Complex 40 and is used for processing and launching Falcon Heavy rockets.
The first SpaceX launch from Launch Complex 39A was SpaceX’s 10th commercial resupply services mission to the International Space Station. The launch on Falcon 9 took place on Feb. 19, 2017, and carried supplies and research to the oribiting laboratory.
Ascent
Mission Timeline for NASA and SpaceX Crewed Launches
(All times are approximate and subject to change with each mission. This timeline was from NASA’s SpaceX Crew-2 launch):
MET | Time | Event |
-06:40:00 | 11:09:00 PM | Crew Wake |
-05:30:00 | 12:19:02 AM | CE Launch Readiness Briefing |
-05:00:00 | 12:49:02 AM | Launch Shift On Console |
-04:59:59 | 12:49:03 AM | Dragon IMU align and Configure for launch |
-04:30:00 | 1:19:02 AM | Dragon prop pressurization |
-04:20:00 | 1:29:02 AM | Crew weather brief |
-04:10:00 | 1:39:02 AM | Crew handoff |
-04:00:00 | 1:49:02 AM | Suit donning and checkouts |
-03:20:00 | 2:29:02 AM | Crew walk out from Neil Armstrong Operations & Checkout Building |
-03:15:00 | 2:34:02 AM | Crew Transportation to Launch Complex 39A |
-02:55:00 | 2:54:02 AM | Crew arrives at pad |
-02:35:00 | 3:14:02 AM | Crew ingress |
-02:20:00 | 3:29:02 AM | Communication check |
-02:15:00 | 3:34:02 AM | Verify ready for seat rotation |
-02:14:00 | 3:35:02 AM | Suit leak checks |
-01:55:00 | 3:54:02 AM | Hatch close |
-00:45:00 | 5:04:02 AM | SpaceX Launch Director verifies go for propellant load |
-00:42:00 | 5:07:02 AM | Crew access arm retracts |
-00:37:00 | 5:11:02 AM | Dragon launch escape system is armed |
-00:35:00 | 5:14:02 AM | RP-1 (rocket grade kerosene) loading begins. 1st stage LOX (liquid oxygen) loading begins |
-00:16:00 | 5:33:02 AM | 2nd stage LOX loading begins |
-00:07:00 | 5:42:02 AM | Falcon 9 begins engine chill prior to launch |
-00:05:00 | 5:44:02 AM | Dragon transitions to internal power |
-00:01:00 | 5:48:02 AM | Command flight computer begins final prelaunch checks. Propellant tank pressurization to flight pressure begins |
-00:00:45 | 5:48:17 AM | SpaceX Launch Director verifies go for launch |
-00:00:03 | 5:48:59 AM | Engine controller commands engine ignition sequence to start |
+00:00:00 | 5:49:02 AM | Liftoff |
+00:01:02 | 5:50:04 AM | Max Q (moment of peak mechanical stress on the rocket) |
+00:02:36 | 5:51:38 AM | 1st stage main engine cutoff (MECO) |
+00:02:39 | 5:51:41 AM | 1st and 2nd stages separate |
+00:02:47 | 5:51:49 AM | 2nd stage engine starts |
+00:07:27 | 5:56:29 AM | 1st stage entry burn |
+00:08:47 | 5:57:49 AM | 2nd stage engine cutoff (SECO-1) |
+00:09:03 | 5:58:05 AM | 1st stage entry burn |
+00:11:58 | 6:01:00 AM | Crew Dragon separates from 2nd stage |
+00:13:02 | 6:02:04 AM | Dragon nosecone open sequence begin |
International Space Station Docking
Commercial crew astronauts arrive at the International Space Station no later than the next day. Dragon performs a series of phasing maneuvers to gradually approach and autonomously dock with the station. After docking, the crew joins the previous expedition crew on the space station. For a short time, the number of crew on the space station increases to upwards of 11 people until members of the previous crew return to Earth a few days later.
Retrieving Dragon
Dragon re-enters Earth’s atmosphere and deploys drogue parachutes, prior to unfurling the spacecraft’s four main parachutes. NASA and SpaceX are capable of supporting seven splashdown sites located off Florida’s east coast and in the Gulf of Mexico. These sites are off the coasts of Pensacola, Tampa, Tallahassee, Panama City, Cape Canaveral, Daytona, and Jacksonville.
SpaceX’s recovery ship is equipped with a crane to lift the capsule out of the water and onto the main deck of the ship. The ship also is outfitted with a medical treatment facility and a helipad in the center of the vessel, allowing for immediate treatment and swift transport to a hospital in the unlikely event of an astronaut medical emergency after splashdown.
Return Flight
Commercial crews are scheduled for long duration stays of up to six months aboard the orbiting laboratory, conducting science and maintenance.
At the conclusion of the mission, astronauts will board Dragon, which will then autonomously undock, depart the space station, and re-enter Earth’s atmosphere. NASA and SpaceX are capable of supporting seven splashdown sites located off Florida’s east coast and in the Gulf of Mexico. Upon splashdown, the crew will be picked up by the SpaceX recovery ship and returned to shore.
Boeing Operations
Starliner
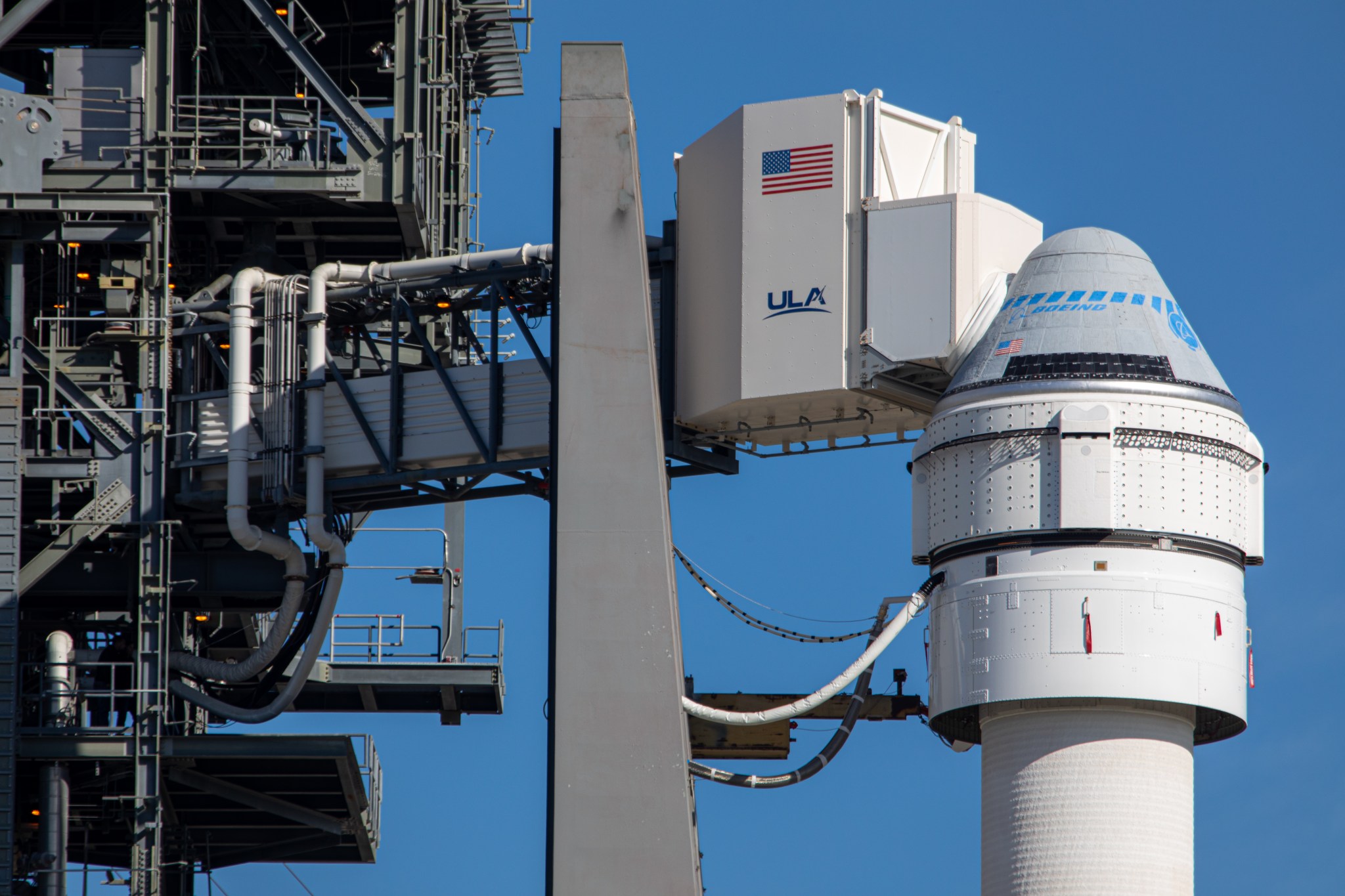
The Starliner spacecraft is Boeing’s commercial crew transportation spacecraft, a next-generation, autonomous spacecraft that will safely take people and cargo to and from low-Earth orbit. The United States will have two, unique human transportation systems that provide redundancy for International Space Station access.
For NASA missions to the International Space Station, Starliner will carry up to four NASA- sponsored crew members and about 220 pounds of time-critical scientific research. Boeing’s Crew Flight Test, part of its Commercial Crew Transportation Capability contract with NASA, will carry two NASA astronauts aboard Starliner to verify the fully integrated rocket and spacecraft system can launch, maneuver in orbit, and dock to the space station, as well as validate that its systems perform as expected.
Launch Abort Engines: Starliner has four launch abort engines that each provide 40,000 pounds of thrust and are dedicated for low altitude abort-use. They are capable of burning about 700 pounds (105 gallons) of propellant every second to rapidly fly crew members away from a dangerous situation.
Orbital Maneuvering and Attitude Control Engines: A total of 20 engines can each produce 1,400 pounds of thrust and, together, provide Starliner with the propulsion it needs to reach orbit after separating from United Launch Alliance’s Atlas V rocket. These engines also would be used in the event of an abort.
Reaction Control System Engines: A combined 28 engines, each providing 85 pounds of thrust, will provide the velocity needed for Starliner to make small directional changes, including when it docks to the International Space Station.
Starliner Design and Development
Boeing’s Starliner was developed in collaboration with NASA’s Commercial Crew Program starting with the first development Space Act Agreement in 2010. In 2014, NASA awarded contracts to Boeing and SpaceX to each safely and cost- effectively transport astronauts to the International Space Station from the United States.
Boeing assembles and processes Starliner for launch at the revitalized Commercial Crew and Cargo Processing Facility at NASA’s Kennedy Space Center in Florida. The facility was previously used to process space shuttle orbiters prior to flight. Starliner is a reusable spacecraft that combines a proven capsule architecture, materials and subsystem technologies.
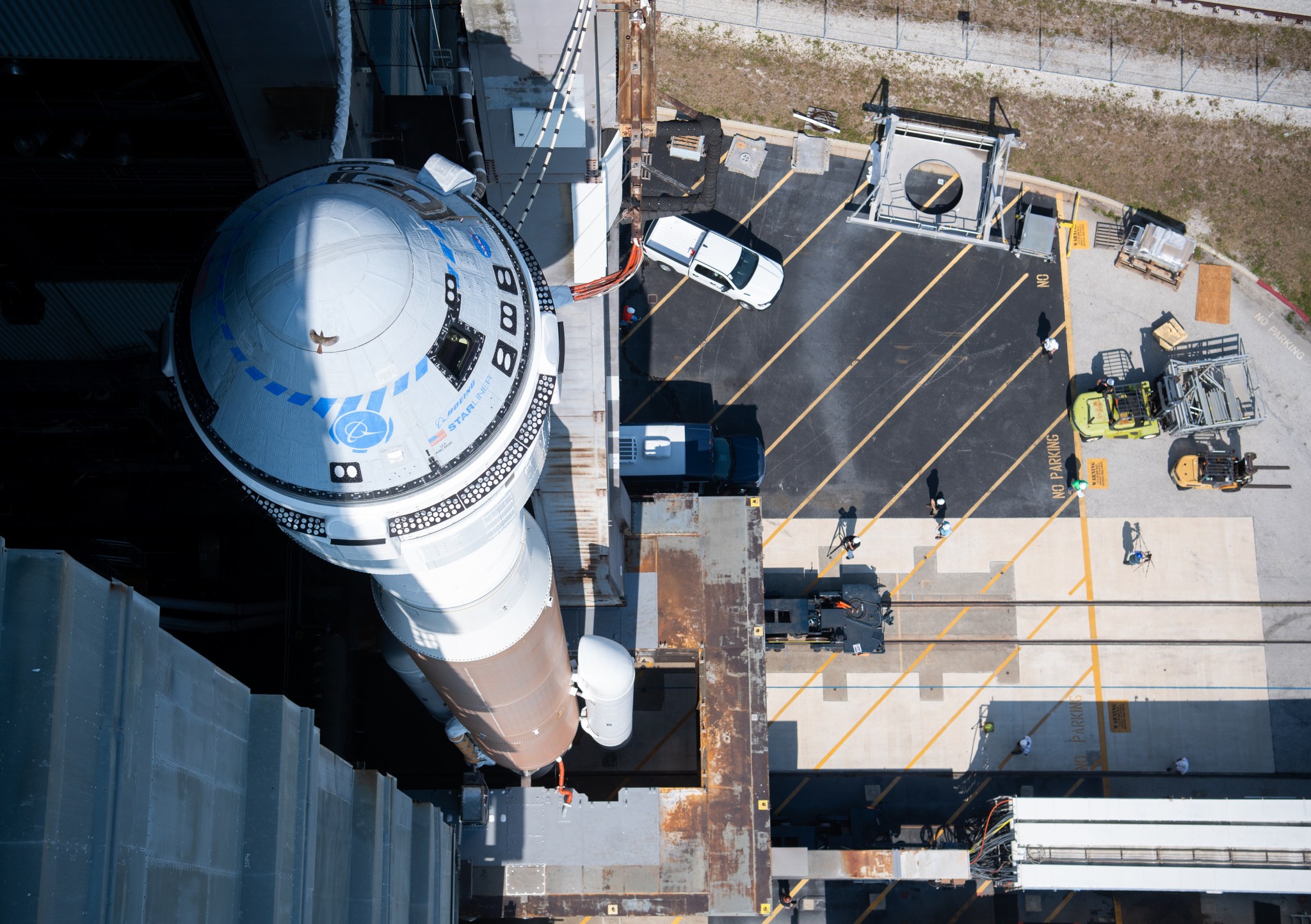
Starliner is designed for up to seven passengers or a mix of crew and cargo, but for NASA missions will carry up to four astronauts to the orbiting laboratory. Starliner has a weldless structure, which eliminates the structural risk of traditional welds, and it also reduces mass and production time. Boeing designed the spacecraft to be reusable up to 10 times with a six-month processing turnaround time. Starliner also has wireless internet and tablet technology for crew interfaces.
One of the NASA requirements under the CCtCap contract was to have autonomous capability. This reduces training time for crews and provides greater flexibility with other potential customers. Starliner adapted a best practice from the commercial industry, with backup manual controls for the pilot. Starliner crews receive extensive training to ensure the astronauts can handle any situation that could arise in the harsh environment of space, even with a spacecraft that is designed to be autonomous.
The service module contains Starliner’s four launch abort engines to be used during an unlikely abort scenario. They would fire between 3 and 5.5 seconds, with enough thrust to get the spacecraft and its crew away from the rocket, before splashing down in the ocean under parachutes. The pusher abort system provides safe crew escape throughout the launch and ascent phase of the mission. Starliner uses a proven parachute and airbag system for shock absorption in order to land on ground.
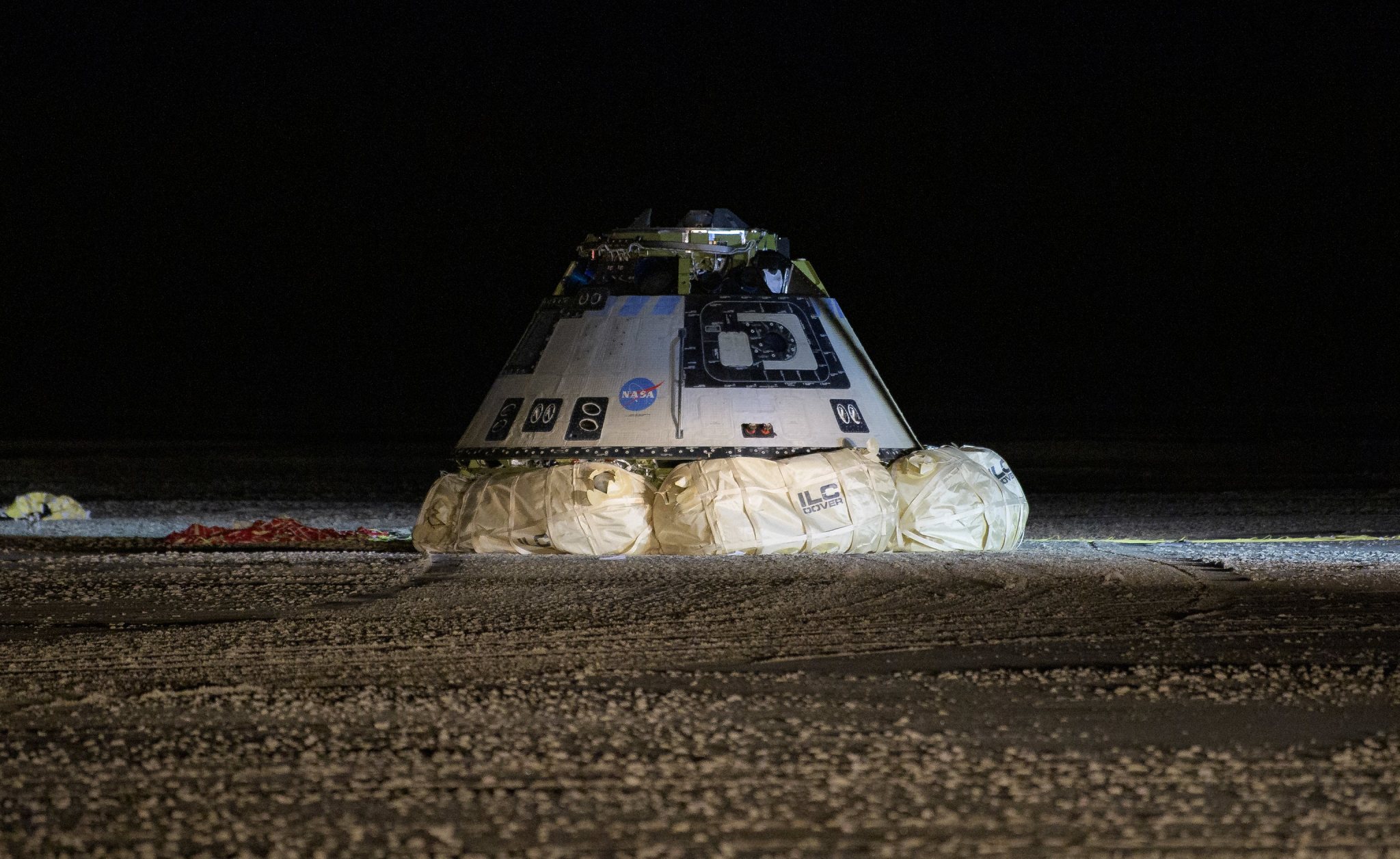
NASA astronauts Butch Wilmore and Suni Williams will be the first astronauts to fly aboard Starliner in the agency’s Boeing Crew Flight Test. The flight test is part of the path to certification for Starliner.
Following the successful mission and completion of the NASA certification process, Boeing will begin regular crew rotation missions to the space station, beginning with Starliner-1. NASA astronauts Scott Tingle and Mike Fincke, as well as CSA (Canadian Space Agency) astronaut Joshua Kutryk will fly on Starliner-1. A fourth crew member is expected to be named for the Starliner-1 mission.
In addition to an uncrewed and a crewed flight test, NASA has ordered six crew rotation missions to the International Space Station from Boeing. Starliner-1 will be the first of these rotation missions. Starliner’s development has required more than 425 suppliers in 37 states.
Atlas V
Atlas rockets have evolved over four decades to become the Atlas V rocket that is used today. John Glenn became the first U.S. astronaut to orbit the Earth after being launched on a heritage Atlas LV-3B rocket from Cape Canaveral, Florida, in 1962.
For Starliner missions to station, Boeing will use the Starliner Configuration of the Atlas V, as seen above.
Configuration Breakdown:
RD-180: The first stage booster will deliver more than 860,000 pounds of thrust at liftoff and a range of continuous throttling capability. The liquid oxygen/liquid kerosene, two-thrust-chamber RD-180 engine is a complete propulsion unit equipped with hydraulics for control valve actuation and thrust vector gimbaling, pneumatics for valve actuation and system purging, and a thrust frame to distribute loads.
Atlas V Booster: The Atlas V Common Booster Core is the first stage of the Atlas V family of rockets produced and operated by United Launch Alliance. It stands 106 feet tall with a 12.5- foot diameter, and houses the combination liquid oxygen/liquid kerosene fuel to power the RD- 180 engine at its base.
Solid Rocket Boosters: A pair or solid rocket boosters, or SRBs, will be used along with the core stage and RD-180 engine to provide enough thrust to achieve liftoff on the way to orbit. Each SRB is capable of approximately 380,000 pounds of thrust, for a total of over 1.6 million pounds of thrust at liftoff. The Atlas V SRBs are manufactured be Aerojet and use the world’s largest monolithic filament-wound carbon composite case.
400 Series Interstage Adapter: The interstage adapter connects the first and second stage while leaving a safe amount of room between the second stage engine and the top of the propellant tanks on the first stage. The adapter is built to be strong enough to manage the forces of launch without buckling, but it also has to be as light as possible. It is jettisoned along with the first stage on the Atlas V.
Dual Engine Centaur: For Starliner missions, the Centaur upper stage will fly with two RL10A- 4- 2 engines, offering more thrust to accommodate Starliner. The engines also help shape the ascent trajectory to station.
Emergency Detection System: This system monitors various launch vehicle parameters to determine the health of the rocket and provides a capability to take action by signaling an abort command so the Starliner can escape, if necessary.
Launch Vehicle Adapter and Aeroskirt: The launch vehicle adapter (LVA) provides the structural attachment of the Starliner capsule to the Atlas V rocket. The LVA uses a truss structure and metallic ring to attach the spacecraft to the Centaur upper stage of the Atlas V. ULA also designed a 70-inch-long aeroskirt to extend Starliner’s aerodynamic surface, which enhances the aerodynamic characteristics, stability, and loads of the Atlas V for the unique crew configuration.
Stats
- Height: 62.5 meters or 205 feet
- Diameter: 3.81 meters or 12.5 feet
- Mass: 21,173 kilograms or 46,678 pounds
- Stages: Two
- Maiden Flight: Aug. 12, 2002
Boeing Spacesuit
Astronauts heading into orbit aboard Boeing’s CST-100 Starliner spacecraft will wear spacesuits that are 40 percent lighter than astronauts wore in years past. Boeing designed the suit with comfort, utility, and production in mind.
The suit capitalizes on historic designs, meets NASA requirements for safety and functionality, and introduces cutting-edge innovations. A few of the advances in the design include:
- Lightweight and flexible materials and new joint patterns
- Helmet and visor incorporated into the suit instead of detachable
- Touchscreen-sensitive gloves
- Vents that allow astronauts to be cooler, but can still pressurize the suit immediately
The full suit, which includes an integrated shoe, weighs about 20 pounds with all of its accessories – about 10 pounds lighter than the launch-and-entry suits worn by space shuttle astronauts.
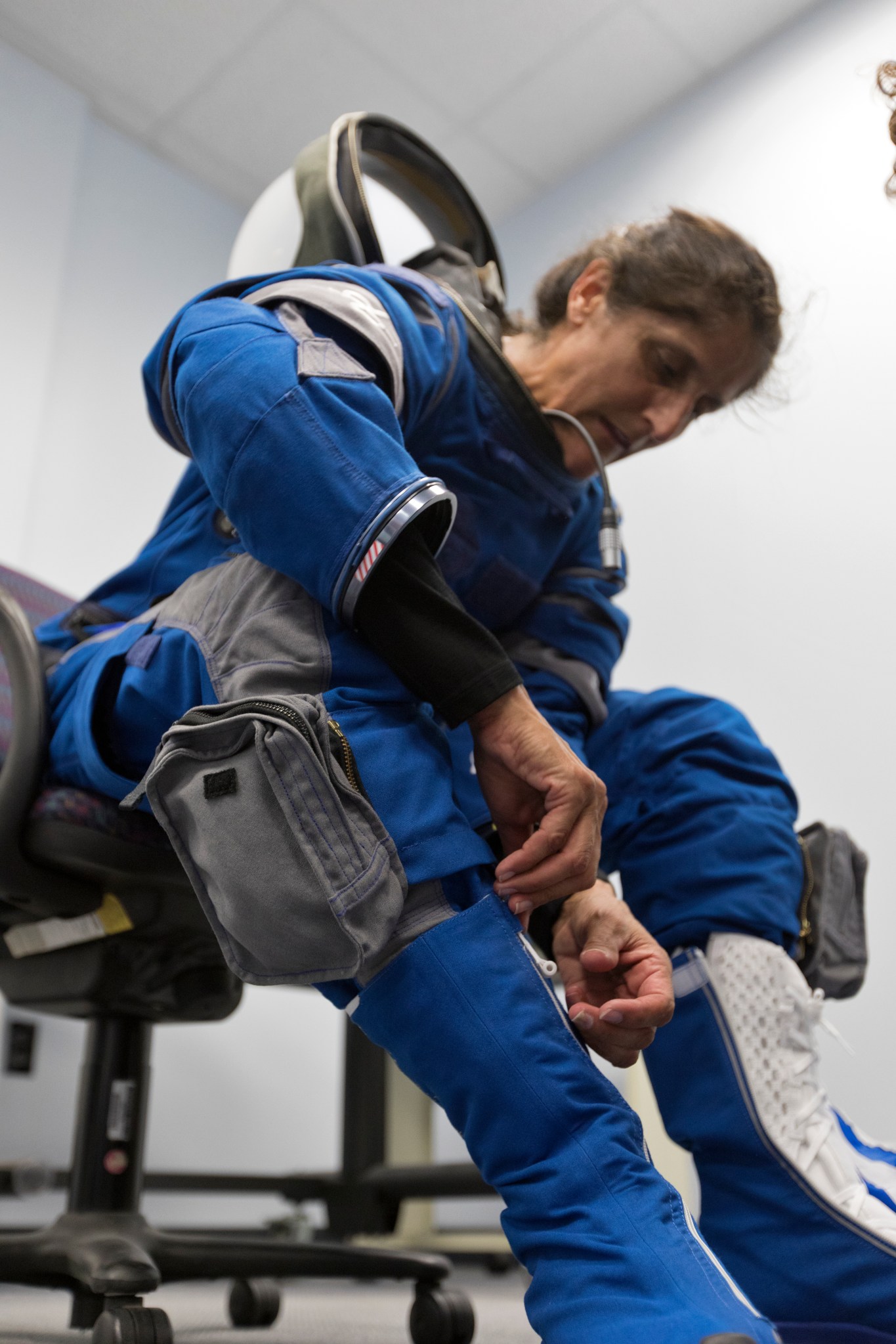
The new Starliner suit’s material lets water vapor pass out of the suit, away from the astronaut, but keeps air inside, making crew cooler without sacrificing safety. Flexible material in the elbows and knees allows astronauts greater movement, while strategically located zippers allow them to adapt the suit’s shape when standing or seated.
On launch day, the crew will don their suits in the historic Astronaut Crew Quarters inside John F. Kennedy Space Center’s Neil Armstrong Operations and Checkout building in Florida before being transported to Space Launch Complex 41. At the launch pad, the crew will ascend the Crew Access Tower and stride through the Crew Access Arm to board Starliner, which will be secured atop a United Launch Alliance Atlas V rocket.
Space Launch Complex 41
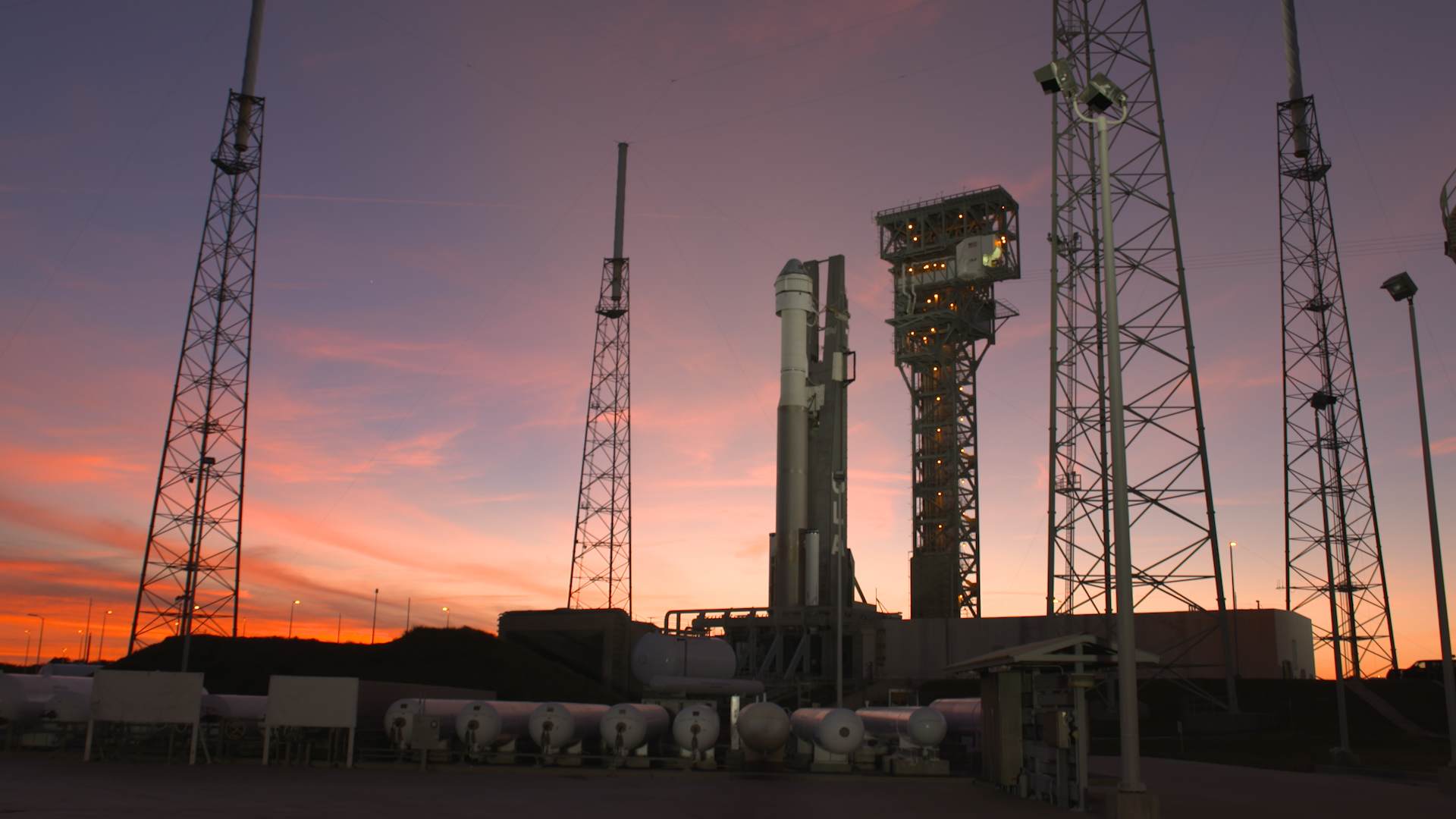
United Launch Alliance (ULA) has modified the pad at Space Launch Complex 41 (SLC-41) at Cape Canaveral Space Force Station for launches of Boeing’s CST-100 Starliner spacecraft aboard ULA’s Atlas V rocket to carry astronauts to the International Space Station.
The Vertical Integration Facility at SLC-41 is where Atlas V is stacked and tested, and where Boeing’s Starliner spacecraft is installed atop the rocket.
For Boeing, launching from SLC-41 meant needing a Crew Access Tower, the first crew- focused structure at Cape Canaveral since Apollo 7.
The tower was built in segments close to the launch pad and stacked together to form the nearly 200-foot-tall structure.
The Crew Access Arm and White Room provide the walkway for astronauts to enter the Starliner spacecraft on top of the Atlas V rocket. The arm is connected to level 12 of the Crew Access Tower, about 172 feet above the pad deck.
Weighing about 90,000 pounds and reaching almost 50 feet, the arm is outfitted with several systems including electronics, data, lighting, and fluids.
The White Room is an enclosed area big enough for astronauts to make final adjustments to their suits before climbing aboard the spacecraft. It is a clean area designed to keep contaminants out of the spacecraft and off the astronauts’ suits.
Boeing and United Launch Alliance designed and built the arm and White Room based on their unique design and lessons learned from NASA’s more than 50 years of spaceflight.
The escape, or egress, system is located on level 12 of the Crew Access Tower – the same level as the Crew Access Arm.
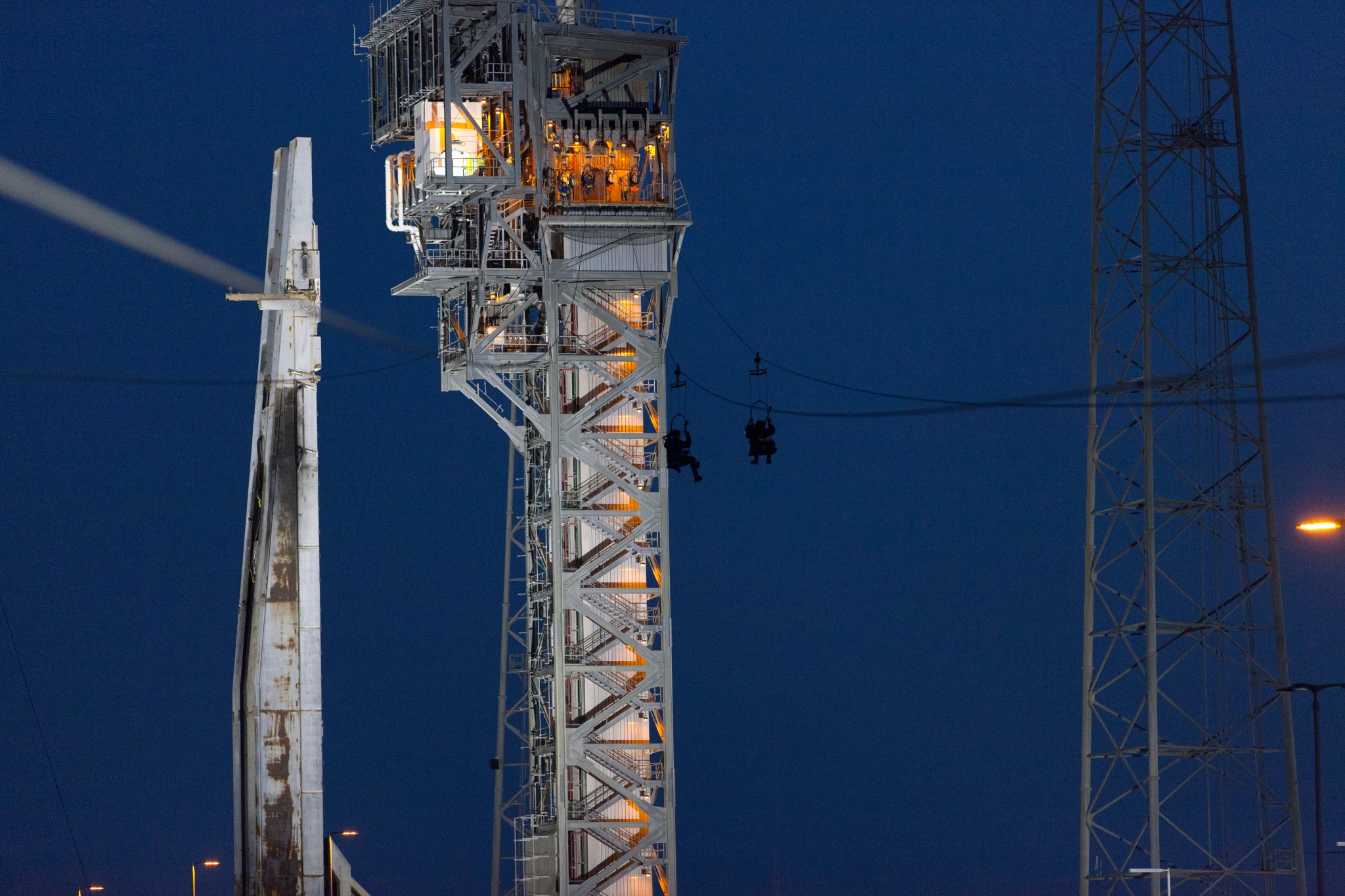
The slide wire emergency escape system features five seats on four separate slide wires, so up to 20 astronauts and ground support personnel can quickly escape from the tower in the unlikely event of a dangerous situation on the launch pad. The egress system allows astronauts and ground personnel to evacuate the Crew Access Tower to a landing zone more than 1,340 feet from the base of the Atlas V, outside of the launch pad perimeter.
The system was designed with the astronauts’ spacesuits in mind; the escape seats are easy to get into and are attached to easily accessible handles to control speed on the slide down from the launch tower.
Ascent

Countdown
(all times are approximate and adjustments may occur prior to launch)
Hour/Min/Sec | Events |
-06:00:00 | Atlas V fueling commences |
-04:05:00 | Atlas V fueling is complete |
-04:04:00 | T-4 built-in hold begins |
-01:25:00 | Hatch closure complete |
-01:15:00 | Prelaunch cabin leak checks |
-01:05:00 | Cabin pressurization complete |
-00:20:00 | Launch Conductor conducts terminal count briefing |
-00:18:00 | CST-100 poll for terminal count |
-00:15:00 | CST-100 to internal power |
-00:10:00 | Crew Access Arm retracted |
-00:08:00 | Launch vehicle poll for terminal count |
-00:04:45 | Starliner configured for terminal count |
-00:04:00 | T-4 minute built-in hold releases |
-00:01:00 | CST-100 is configured for launch |
-00:00:03 | RD-180 engine ignition |
Launch, Landing and CST-100 Deployment
(all times are approximate and adjustments may occur prior to launch)
Hour/Min/Sec | Events |
+00:00:01 | Liftoff |
+00:00:06 | Begin pitch/yaw maneuver |
+00:00:41 | Maximum dynamic pressure |
+00:01:05 | Mach 1 |
+00:02:22 | SRB jettison |
+00:04:29 | Atlas booster engine cutoff (BECO) |
+00:04:35 | Atlas Centaur separation |
+00:04:41 | Ascent cover jettison |
+00:04:45 | Centaur first main engine start (MES-1) |
+00:05:05 | Aeroskirt jettison |
+00:11:54 | Centaur first main engine cutoff (MECO-1) |
+00:14:54 | Starliner separation |
+00:31:00 | Starliner orbital insertion |
International Space Station Docking
Once in a stable orbit on course for the International Space Station, Starliner begins its rendezvous procedures. Unique to the Crew Flight Test mission, Starliner will conduct a series of demonstration burns a few hours after launch to prove the spacecraft can maneuver itself safely in space. As Starliner closes on the station, the vehicle’s star tracker cameras will first see the orbiting lab as a distant, but bright, point of light moving in front of a background of fixed stars.
Over the next few hours, Starliner will slowly move itself closer to the station and then pause before entering the 200-meter “keep out sphere” until station flight controllers clear it to enter. Starliner then begins the docking process, pausing once more 10 meters away from a Boeing-built International Docking Adapter and then continuing to final approach and docking.
Retrieving Starliner

The Starliner is designed to land at one of five landing sites in the continental U.S. After re-entering the atmosphere. Starliner will deploy pilot and drogue parachutes, prior to unfurling the spacecraft’s three main parachutes. Once the capsule is stable under its parachutes the spacecraft’s base heat shield will drop away, allowing the air bag system to inflate prior to a soft landing.
Boeing’s Starliner has several designated landing sites across the western United States:
- White Sands Missile Range in New Mexico (dual sites, preferred)
- Edwards Air Force Base in California
- Willcox Playa in Arizona
- Dugway Proving Ground in Utah
Return Flight
Once Starliner is ready and cleared to leave the International Space Station, the undocking process begins and the spacecraft slowly backs away from the station. After a flyaround maneuver, Starliner positions itself for the deorbit burn. A short time later, when Starliner is in the right position over the Pacific Ocean, the service module conducts the deorbit burn, slowing down Starliner from orbital speeds, and then the service module detaches.
The crew module begins its descent through the atmosphere, facing reentry heat of 3,000 degrees Fahrenheit (1,650 degrees Celsius). The parachute sequence begins around 30,000 feet (9 km) above the ground, when Starliner jettisons the forward heat shield that protects the parachutes during reentry. Two drogue parachutes begin slowing Starliner down, then detach. The three main parachutes are then deployed and inflated, and about 3,000 feet (0.9 km) off the ground, the airbags inflate. On touchdown, those airbags absorb the initial forces of landing, cushioning the crew for a soft, safe return to Earth.
Safety and Innovation
Crew safety remains NASA’s primary responsibility and priority for all human spaceflight programs. Since the beginning of NASA’s Commercial Crew Program, safety has been built into the agency’s requirements as a direct result of NASA’s extensive experience in human spaceflight systems development and operations.
NASA and its commercial partners, Boeing and SpaceX, have developed and rigorously tested systems that prioritize crew safety and survival, including launch pad emergency escape and egress systems. Through successful completion of launch abort tests, both companies have demonstrated their ability to safely fly astronauts away from an emergency situation.
These commercial systems are required to meet NASA’s safety and performance requirements for certification to transport NASA and international partner astronauts to the space station.
Foundation of Innovation
NASA’s Commercial Crew Program tailored requirements for a new generation of human-rated spacecraft, allowing the industry to create innovative design solutions, manufacturing processes, operational methods and engineering techniques. The result has been a series of components, systems and now spacecraft and rockets flying astronauts to and from the International Space Station in a manner that is both cost-effective and reliable.
At the heart of the innovation is an approach that is new to NASA’s human spaceflight programs, which calls on the private industry to design, build and operate spacecraft and rockets along with all their related ground systems, control centers and support infrastructure. To learn more on innovation and the Commercial Crew Program, click https://www.nasa.gov/general/business-innovation-key-to-commercial-crew-programs-success/.
Certification
The certification process is based upon NASA’s decades of experience, as well as the combined talents and experience of the Boeing and SpaceX engineers, technicians and managers.
When Boeing’s Starliner is also certified by NASA, the United States will have two, unique human transportation systems that provide redundancy for International Space Station access and end sole reliance on the Russian Soyuz.
To complete SpaceX certification, NASA teams used flight data from the company’s uncrewed Demo-1 flight test, spacecraft abort tests, and its crewed Demo-2 flight test to verify that SpaceX systems met NASA’s safety and performance requirements. The crew aboard the Demo-2 test flight validated that the spacecraft systems operated as planned in both autonomous and manual settings. NASA will examine a similar set of data following Boeing’s uncrewed Orbital Flight Test 2 (OFT-2) and eventual Crew Flight Test with astronauts aboard in order to certify the Boeing transportation system to begin regular astronaut flights to the space station.
NASA will verify that, throughout upcoming flight tests and regular missions, the companies demonstrate compliance with Commercial Crew Program hardware and software requirements, NASA standards for design and construction, engineering and management processes, and validation of the entire crew transportation system in a flight environment. The companies will continue to work with NASA to resolve issues as necessary to ensure the systems meet NASA’s safety and performance requirements outlined in the Commercial Crew Transportation Capability (CCtCap) contracts.
Boeing and SpaceX each have a set number of regular crewed science missions contracted with NASA following certification. SpaceX has completed seven of its 14 and is currently on its eighth (Crew-8). Boeing will fly its first regular mission with astronauts (Starliner-1) following completion of the Crew Flight Test and NASA certification.
A Space-Borne Lifeboat
New, American-made spacecraft flying to the International Space Station play a big role in bringing resident astronauts home to Earth, but their missions also include the ability to provide the orbiting laboratory with a temporary shelter in case of an emergency in space or even a safe ride back to Earth with short notice.
The scenarios that would call for the spacecraft to operate as space-borne lifeboats have not occurred on the space station before, but mission planners have long made sure they are prepared. An electrical issue or ammonia leak on the space station could call for astronauts to shelter inside a Commercial Crew Program spacecraft long enough to correct the problem.
To learn more about the life saving potential of commercial spacecraft docked to the space station, visit:
https://www.nasa.gov/feature/commercial-crew-spacecraft-will-offer-a-quick-escape-from-station
International Docking Adapter
Getting to orbit is a milestone and not a destination. It is no small feat to dock with our orbiting outpost. But before that feat can be achieved, the International Space Station needed an upgrade.
The International Docking Adapters were built to the International Docking System Standard, which features built-in systems for automated docking and uniform measurements. That means any destination or any spacecraft can use the adapters in the future—from the new commercial spacecraft to other international spacecraft yet to be designed. The adapters also include fittings so power and data can be transferred from the station to the visiting spacecraft.
SpaceX’s Crew Dragon spacecraft has docked at the adapters, and soon Boeing’s Starliner will also dock at the adapters as part of NASA’s Commercial Crew Program.
For more information on the International Docking Adapters, visit:
https://www.nasa.gov/missions/station/meet-the-international-docking-adapter/
Space Station Research
The addition of the Boeing Starliner and SpaceX Crew Dragon to the manifest of spacecraft heading to the International Space Station raises more than the opportunity for astronauts to fly to and from space aboard American spacecraft. It also increases the amount of science and broadens the research that can be performed aboard the orbiting laboratory.
That’s because the new generation of human-rated spacecraft are designed to carry time- critical science to and from the space station along with astronauts. Researchers are able to work with astronauts aboard the station to undertake a wide array of different science investigations and benefit from the increased opportunity to see their research returned back to Earth for continued examination.
To learn more about the benefits of commercial crew to space station research, visit:
https://www.nasa.gov/general/commercial-crew-missions-offer-research-bonanza-for-space-station/
Helicopter Rescue Training
When astronauts splash down into the ocean after their journey to the International Space Station on SpaceX’s Crew Dragon spacecraft, recovery teams must be able to transport them to land quickly. In the unlikely event of an astronaut medical emergency, SpaceX has outfitted each of its recovery ships with a medical treatment facility and a helipad in the center of the vessel.
To read more about SpaceX’s helicopter rescue training, visit:
https://blogs.nasa.gov/commercialcrew/2018/11/05/spacex-rehearses-helicopter-landing-at-sea/
Water Rescue Training
Rescue and recovery involves meticulous planning and close coordination among NASA, the Department of Defense (DOD) and company recovery teams for Crew Dragon. In the event of a variety of contingency landings, an elite team is prepared to rescue the crew anywhere in the world.
In preparation for both launch and landing, U.S. Air Force “Guardian Angel” pararescue forces will be pre-positioned in key locations, alert and ready to deploy at a moment’s notice. Should a spacecraft splash down within 200 nautical miles of the launch site, an HC-130 aircraft, along with two HH-60 Pave Hawk helicopters, will deploy from Patrick Space Force Base in Florida. These aircraft will carry a team of up to nine Guardian Angels—also known as pararescue specialists— along with rescue equipment and medical supplies.
To read more about water rescue training, visit:
Triage and Medical Evacuation Training
It is vital that teams prepare for launch day operations, including possible but unlikely emergency scenarios, and simulations are key to getting teams as ready as possible.
Teams from NASA, HSFS and SpaceX have conducted joint medical triage and medical evacuation (medevac) training exercises at NASA’s Kennedy Space Center in Florida.
To read more about joint medevac training, visit:
https://blogs.nasa.gov/commercialcrew/2018/10/25/commercial-crew-teams-practice-triage-and- medical-evacuation/
Crew Dragon Abort System
SpaceX completed a successful launch escape test of its Crew Dragon spacecraft abort system in January 2020. It was an important step in NASA’s endeavor to rebuild America’s ability to launch astronauts to the International Space Station from U.S. soil and set the stage for the historic Demo- 2 test flight with astronauts in May 2020. To read more about the successful launch escape test, visit:
To read more about the successful pad abort test of Crew Dragon, visit:
https://www.nasa.gov/press-release/spacex-demonstrates-astronaut-escape-system-for-crew- dragon-spacecraft
To see the pad abort test footage, watch the video below.
Space Launch Complex 41 Emergency Egress
An emergency egress system has been installed at Space Launch Complex 41 at Cape Canaveral Space Force Station to prepare for Boeing’s CST-100 Starliner crew launches for NASA’s Commercial Crew Program. The Starliner spacecraft and United Launch Alliance Atlas V rocket that will boost astronauts to the International Space Station will have many safety elements built into the systems.
The Starliner emergency egress system operates a lot like a zip line, with four egress cables connecting at level 12 of the Crew Access Tower to a landing zone about 1,300 feet away from the launch vehicle. Five individual seats on four separate lines can transport up to 20 people off of the tower in the unlikely event there is an emergency on the launch pad. NASA has partnered with private industry to take astronauts to the space station.
To see highlights of some of the emergency egress testing, visit:
https://images.nasa.gov/details/KSC-20170314-MH-KLS01-0002-ULA_EES_Demo_Coverage_H265-3149885.
Starliner Abort System
In the unlikely event of an emergency, Boeing’s CST-100 Starliner is equipped with an abort system capable of lifting the spacecraft and crew to safety. The high-tech, high-power system will be activated once the crew is securely on board and can be used while the spacecraft is still on the pad or during any portion of launch until the crew reach orbit. Boeing completed a successful demonstration of this capability in November 2019.
To read more about the Starliner’s abort system, visit:
https://blogs.nasa.gov/commercialcrew/2016/10/18/starliner-propulsion-hardware-arrives- testing-begins/.
Commercial Crew Media Contacts
Joshua Finch / Claire O’Shea / Julian Coltre
Office of Communications
NASA Headquarters
joshua.a.finch@nasa.gov / claire.a.o’shea@nasa.gov / julian.n.coltre@nasa.gov
Steve Siceloff / Stephanie Plucinsky
Public Affairs
NASA’s Kennedy Space Center
Phone: 321-867-2468
steven.p.siceloff@nasa.gov / stephanie.n.plucinsky@nasa.gov
Kenna Pell / Anna Schneider
Public Affairs
NASA’s Johnson Space Center
Phone: 281-483-5111
kenna.m.pell@nasa.gov / anna.c.schneider@nasa.gov
International Space Station
Sandra Jones
Public Affairs
NASA’s Johnson Space Center
Phone: 281-483-5111
sandra.p.jones@nasa.gov
Flight Operations
Courtney Beasley / Chelsey Ballarte
Public Affairs
NASA’s Johnson Space Center
Phone: 281-483-5111
courtney.m.beasley@nasa.gov / chelsey.n.ballarte@nasa.gov
Boeing
Starliner Communications Team
Phone: 321-360-3602
starliner@boeing.com
SpaceX
SpaceX Public Affairs
media@spacex.com
James Gleeson
james.gleeson@spacex.com
Rocket Science: Ride to Station
This interactive app gives an overview of the complexities involved in getting to and conducting research aboard the International Space Station. Play online or download in the app store.
Learn More
Additional Multimedia Resources
STEM Engagement
NextGen STEM
Bringing the accomplishments of NASA and our commercial partners, Boeing and SpaceX, to audiences through a variety of educational resources and opportunities.
These hands-on, authentic STEM activities and classroom resources, including apps like “Rocket Science: Ride to Station,” engage students and educators in the mission while helping build a strong and growing U.S. space industry in low Earth orbit by providing meaningful STEM experiences to the future generation of explorers.
Learn More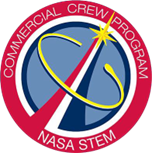
NASA’s Virtual Guest Program
Over one million virtual guests have followed NASA launches and milestones since 2020. The program offers a registration opportunity for each launch.
After registration, guests have access to curated resources, email updates, and a passport stamp for their virtual guest passport following a successful launch. Guests also have the opportunity to send a message to the crew through their registration for crewed missions. Providing the virtual guest program allows for guests to be notified of any schedule changes, interactive opportunities, and updated information.
Learn More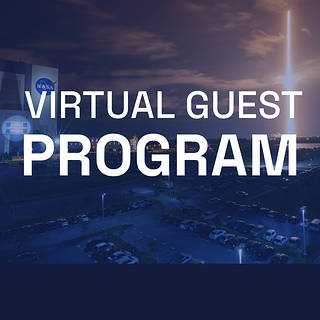
360 Virtual Reality Tour
Through 360-degree video and virtual reality technology, students can get a behind- the- scenes look at NASA and commercial partner facilities, where next-generation human- rated spacecraft and rockets are being developed and tested for flight, without leaving the classroom. These provide an experience second only to being there.
360 Tour Video Playlist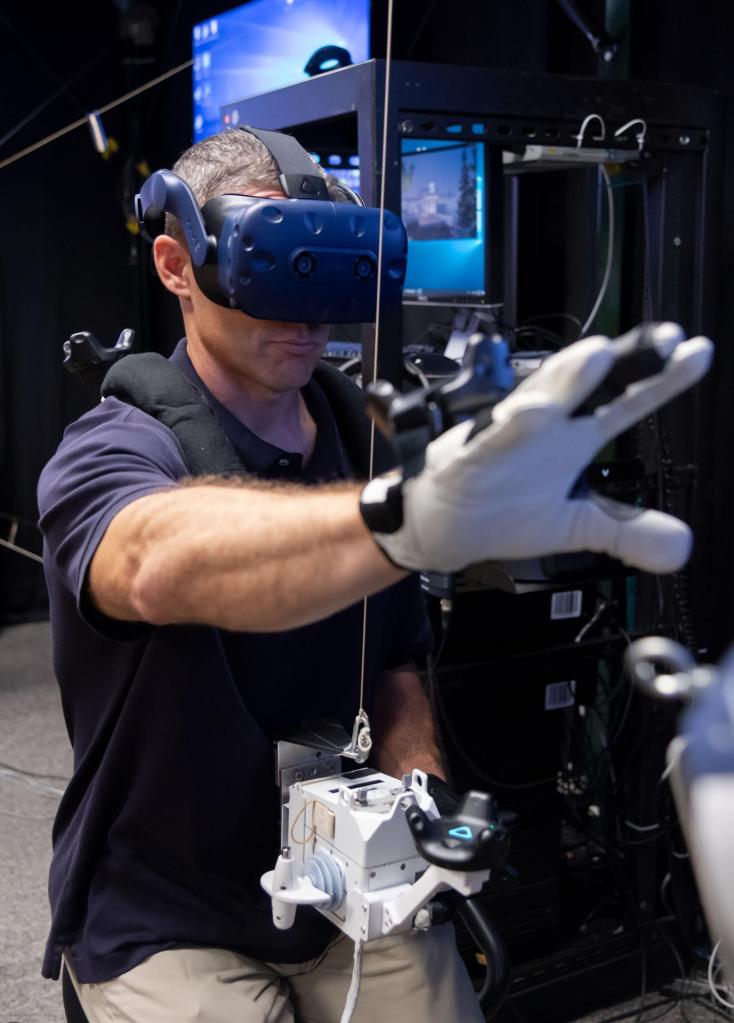