Marshall Leadership Discusses COVID-19, Work Environments in Virtual Town Hall
Jody Singer, left, director of NASA’s Marshall Space Flight Center, is joined by Steve Miley, Marshall associate director, for a virtual town hall Oct. 25. Singer and Miley discussed COVID-19 vaccination deadlines, updates on remote work environments, the Space Launch System Request for Information, and the reorganization of NASA’s human spaceflight operations. The leaders also answered questions from the workforce on the vaccine mandate, reasonable accommodation process, and telework submitted by the Marshall team. “We’re still in Stage 2, still in a maximum telework environment,” Miley said. “We are monitoring the situation and, for the most part, things are improving. We are still considered at a high level of risk for COVID spread … but rates of positive infection rates are decreasing and improving. Everything is headed in the right direction.” Also taking part in the town hall were Larry Mack, deputy director of the Office of Human Resources; Susan Whitfield, director of the Office of Human Resources; Loucious Hires, director of the Office of Diversity & Equal Opportunity; and Dr. Joseph Musick, Marshall medical director. Marshall team members can watch the town hall on Inside Marshall. (NASA)
NASA Completes Mega-Moon Rocket Stacking
NASA has completed stacking of the agency’s mega-Moon rocket and spacecraft that will launch the next generation of deep space operations. Engineers and technicians successfully secured the Orion spacecraft atop the fully assembled Space Launch System rocket at the agency’s Kennedy Space Center just before midnight Oct. 21.
With stacking complete, a series of integrated tests now sit between the rocket and targeted liftoff of the Artemis I uncrewed mission in February 2022. The mission will pave the way for a future flight test with crew before NASA establishes a regular cadence of more complex missions with astronauts on and around the Moon under Artemis.
“With stacking and integration of NASA’s Space Launch System rocket and Orion spacecraft complete, we’re getting closer and closer to embarking on a new era of human deep space exploration,” NASA Administrator Sen. Bill Nelson said. “Thanks to the team’s hard work designing, manufacturing, testing, and now completing assembly of NASA’s new rocket and spacecraft, we’re in the home stretch of preparations for the first launch on the Artemis I mission, paving the way to explore the Moon, Mars, and beyond for many years to come.”
The stack now stands 322 feet tall inside the Vehicle Assembly Building at Kennedy as it enters the final phase of testing before launch. Next up, NASA’s Exploration Ground Systems teams will conduct integrated tests of Orion and SLS along with the ground equipment, prior to rolling the rocket and spacecraft to the launch pad for a final test, known as the wet dress rehearsal. This final test will run the rocket and launch team through operations to load propellant into the fuel tanks and conduct a full launch countdown. Following a successful rehearsal, NASA will roll the stack back into the Vehicle Assembly Building for final checks and set a target date for launch.
“It’s hard to put into words what this milestone means, not only to us here at Exploration Ground Systems, but to all the incredibly talented people who have worked so hard to help us get to this point,” said Mike Bolger, Exploration Ground Systems program manager. “Our team has demonstrated tremendous dedication preparing for the launch of Artemis I. While there is still work to be done to get to launch, with continued integrated tests and wet dress rehearsal, seeing the fully stacked SLS is certainly a reward for all of us.”
Through Artemis missions, NASA will land the first woman and the first person of color on the surface of the Moon, paving the way for a long-term lunar presence and serving as a steppingstone on the way to Mars.
NASA Seeks Input to Position SLS for Long-Term Exploration
NASA is preparing for the first flight of the Space Launch System rocket and the Orion spacecraft from the agency’s Kennedy Space Center, along with other flight hardware for the next several Artemis missions in production around the country. The agency also is looking forward to future missions and working to transition SLS from design and development to production and operations to support NASA’s long-term exploration goals.
To accomplish this goal, NASA has invited industry to submit responses to a Request for Information to assist NASA in maximizing the long-term efficiency of the SLS rocket’s super-heavy-lift, national launch capabilities while streamlining operations to minimize production, operations, and maintenance costs. NASA will use the information received to inform plans for production and operations of the SLS rocket beginning on or about Artemis V to ensure this national asset is available for decades of deep space exploration to the Moon, Mars, and beyond.
“The primary goal of the RFI is to gather information to position the agency to support long-term exploration of the Moon and beyond by streamlining SLS production and operations,” said Kathy Lueders, associate administrator for the Space Operations Mission Directorate at NASA Headquarters. “Working with industry will enable us to expand availability of this national capability to not only NASA, but also to other government and nongovernment entities, and bring down the cost of SLS launches to benefit multiple users.”
As the agency continues to refine the plans for future exploration missions, NASA is looking to transform current traditional acquisition approaches. Specifically, the agency is considering an overall acquisition strategy of a service provider for the integrated SLS system in partnership with a potential service provider for the ground systems and launch operations in order to evolve into an integrated launch service available to NASA and other customers in both the public and private sectors.
This approach envisions NASA as the priority customer with at least one crewed flight per year for the next 10 or more years as an essential part of the agency’s human exploration plans at the Moon. With the capability to send unprecedented mass and volume to the Moon and beyond, SLS is designed to be flexible and evolvable and will also open new possibilities for NASA and other users to send large cargos or science missions into the far reaches of the solar system.
“The NASA workforce and our industry partners can be proud of moving SLS through design, development, testing, manufacturing, assembling, and soon flying the rocket for the first time on Artemis I,” said John Honeycutt, SLS program manager at NASA’s Marshall Space Flight Center. “Our team will remain focused on using SLS’s unprecedented power to launch the first three Artemis missions to the Moon and on increasing SLS’s capability by adding the Exploration Upper Stage on Artemis IV. SLS is a national capability that will be used for decades to make the boldest space missions possible.”
As NASA transitions responsibility for SLS production, integration, and launch operations to industry, the agency’s development efforts will shift focus to the next generation of technologies and infrastructure to ensure U.S. leadership in space and extend human missions farther into the solar system.
“While our near-term focus is on a successful Artemis I mission, NASA is looking ahead and preparing to tackle the next development challenges for our exploration goals, such as habitats and other lunar surface systems, cryogenic fluid management, and spacecraft nuclear propulsion.” said Jim Free, associate administrator for the Exploration Systems Development Mission Directorate at NASA Headquarters. “The talented workforce at Marshall, including the workforce responsible for SLS development, is recognized as the go-to for expertise on transportation systems and advanced manufacturing and will be essential in developing our Moon to Mars capabilities.”
SLS and NASA’s Orion spacecraft, along with the commercial human landing system and the Gateway in orbit around the Moon, are NASA’s backbone for deep space exploration. SLS is the only rocket that can send Orion, astronauts, and supplies to the Moon in a single mission.
NASA Announces Winners of Deep Space Food Challenge
By Taylor Goodwin
Variety, nutrition, and taste are some considerations when developing food for astronauts. For NASA’s Deep Space Food Challenge, students, chefs, small businesses, and others whipped up novel food technology designs to bring new solutions to the table.
NASA has selected 18 U.S. teams to receive a total of $450,000 for ideas that could feed astronauts on future missions. Each team will receive $25,000. Additionally, NASA and the Canadian Space Agency jointly recognized 10 international submissions.
NASA Television, the NASA app, and the agency’s website will air a show on the Deep Space Food Challenge at 10 a.m. CST Nov. 9 with details about the competition, winning solutions, and what could be next for the teams.
Special guests during the show will include celebrity chef Martha Stewart and retired NASA astronaut Scott Kelly, who will announce the winners of two awards honoring international teams that demonstrated exceptional innovation. Other participants will include retired Canadian Space Agency astronaut Chris Hadfield and celebrity chef Lynn Crawford.
“NASA is excited to engage the public in developing technologies that could fuel our deep space explorers,” said Jim Reuter, associate administrator for NASA’s Space Technology Mission Directorate at the agency’s headquarters. “Our approach to deep space human exploration is strengthened by new technological advances and diverse community input. This challenge helps us push the boundaries of exploration capabilities in ways we may not recognize on our own.”
NASA, in coordination with the Canadian Space Agency, opened the Deep Space Food Challenge in January. The competition asked innovators to design food production technologies or systems that met specific requirements: They would need to use minimal resources and produce minimal waste. The meals they produced would have to be safe, nutritious, and delicious for long-duration human exploration missions.
For the U.S. teams, NASA’s judges grouped submissions based on the food they envisioned producing. Among the designs were systems that used ingredients to create ready-to-eat foods, such as bread, as well as dehydrated powders that could be processed into more complex food products. Others involved cultivated plants and fungi or engineered or cultured food, such as cultured meat cells.
Details about the winning submissions and teams can be found on the challenge website.
“These types of food systems could offer benefits on our home planet,” said Robyn Gatens, director of the International Space Station Program at NASA and challenge judge. “Solutions from this challenge could enable new avenues for worldwide food production in resource-scarce regions and locations where disasters disrupt critical infrastructure.”
The winning U.S. teams, in alphabetical order, are:
- Astra Gastronomy of San Francisco
- BeeHex of Columbus, Ohio
- BigRedBites of Ithaca, New York
- Biostromathic of Austin, Texas
- Cosmic Eats of Cary, North Carolina
- Deep Space Entomoculture of Somerville, Massachusetts
- Far Out Foods of St. Paul, Minnesota
- Hefvin of Bethesda, Maryland
- Interstellar Lab of Los Angeles
- Kemel Deltech USA of Cape Canaveral, Florida
- Mission: Space Food of Mountain View, California
- Nolux of Riverside, California
- Project MIDGE of La Crescenta-Montrose, California
- RADICLE-X of Brooklyn, New York
- SIRONA NOMs of Golden, Colorado
- Space Bread of Hawthorne, Florida
- Space Lab Café of Boulder, Colorado
- µBites of Carbondale, Illinois
The Canadian Space Agency ran a parallel competition with a separate application, judging process, and prize for participating Canadian teams. The agency will announce its winners at a later date.
Teams from outside the U.S. and Canada qualified for recognition but were not eligible for monetary prizes. The 10 international submissions recognized are:
- ALSEC Alimentos Secos SAS of Antioquia, Colombia
- Ambar of Bucaramanga, Colombia
- Electric Cow of Germany
- Enigma of the Cosmos of Écully, France and Brunswick, Australia
- JPWORKS SRL of Milan, Italy
- KEETA of Bangkok, Thailand
- LTCOP of Piracicaba, Brazil
- Natufia X Edama of Thuwal, Saudi Arabia
- Solar Foods of Lappeenranta, Finland
- π of Ghaziabad, India
The Deep Space Food Challenge is a NASA Centennial Challenge. Centennial Challenges are part of the Prizes, Challenges, and Crowdsourcing program within NASA’s Space Technology Mission Directorate at the agency’s Headquarters and are managed at NASA’s Marshall Space Flight Center. Subject matter experts at NASA’s Johnson Space Center and NASA’s Kennedy Space Center support the competition. NASA, in partnership with the Methuselah Foundation, manages the U.S. and international Deep Space Food Challenge competition.
Goodwin, an LSINC employee, supports Marshall’s Office of Strategic Analysis & Communications.
60 Years of Pride, Unwavering Dedication on Display at Michoud During Hurricane Ida
By Heather Keller
On Aug. 29, 2021 – 16 years to the day of Hurricane Katrina, one of the most devastating storms to make landfall along the Louisiana/Mississippi Gulf Coast – emergency crews at NASA’s Michoud Assembly Facility found themselves in familiar territory. As Hurricane Ida threatened the facility, the team demonstrated the same fierce commitment to its mission as it has for 60 years; and once again protected vital equipment from serious damage.
A Category 4 storm at landfall, Ida brought 150 mph sustained winds, substantial rainfall, and flooding to New Orleans and surrounding parishes for six hours. At Michoud, on-site emergency crews recorded 110 mph wind gusts, over 13 inches of rain, and 85 mph sustained winds before sensing devices failed in Ida’s ferocity. As the storm passed, they watched on security cameras as water intrusion threatened the factory. Other cameras showed damage and leaks, some of which were still undergoing repairs from 2020’s Hurricane Zeta, which brought 50 mph sustained winds with gusts of 101 mph.
“This facility has weathered many storms the past 60 years,” Michoud Acting Director Lonnie Dutreix said. “It continues to stand strong, and even though we have faced challenges, including COVID-19 and Hurricane Ida, this team has managed to build on the legacy of Apollo and shuttle, and continues to build hardware for the Artemis missions to the Moon.”
Once conditions were safe, crews began assessing damage. Initial reports showed everyone safe and accounted for and no visible damage to the Space Launch System rocket and Orion spacecraft flight hardware that is built at Michoud for Artemis. In the following days, crews remained on-site to continue assessments, began cleanup, and initiate repair efforts. Operating through the Labor Day weekend, the team worked with the city of New Orleans to get power restored to the facility and pumped 45,000 gallons of rainwater out of Building 103, the 43-acre factory. A few weeks later, Michoud was challenged by Tropical Storm Nicholas, which brought more damage and rain, for a combined 65,000 gallons of rainwater intrusion. NASA tenant and contractor teams worked persistently to restore utility services to buildings throughout the site.
“I am proud to be part of the NASA family and lead this team at Michoud. Experiencing how they responded during Hurricane Ida to keep critical hardware safe makes me even prouder,” Dutreix said. “Even though many team members faced personal challenges and losses, they did not hesitate to stay and protect this facility. That takes a special kind of person, and we are fortunate to have that kind of team here at Michoud.”
No stranger to storms, Michoud saw impacts from Hurricanes Betsy and Camille among others in its 60 years of operation for NASA. The team’s most notable success came during 2005’s Hurricane Katrina. While most of the area was devastated from the storm, Michoud stood dry and protected through meticulous preparation, redundant levee protection, and the utilization of on-site pump stations.
As Ida encroached on the anniversary of Katrina, Michoud had its sites on another milestone as it prepared to celebrate the facility’s 60th anniversary as America’s rocket factory. Since Ida scrubbed original celebration plans, Michoud will celebrate 60 years of success this fall with a series of events.
On Sept. 7, 1961, NASA named Michoud the location to build the Saturn V rockets and core stages for the Apollo program. In the years that followed, Michoud manufactured the first stages of the Saturn IB and Saturn V rockets as well as the 15-story-tall external tanks for 135 shuttle flights.
Today, Michoud manufactures and assembles the largest rocket stage NASA has ever constructed: the core stage that provides power to help launch SLS. The factory also produces the Orion spacecraft that will carry astronauts to the Moon, and its launch abort system that can pull Orion away from the rocket in case of emergencies. The SLS team at Michoud just started manufacturing the Exploration Upper Stage, which will allow future SLS configurations to send 40% more payload to the Moon. By protecting the hardware from the storm, crews prevented what could have been a catastrophic loss to the mission.
Repairs continue a month after Ida. Rainwater has been removed and 2,000 point repairs have been conducted to the roof covering the factory. Though more repairs are needed, Michoud is open and operating at its pre-storm capacity.
From the groundbreaking missions of Apollo to the engineering feats made possible by the Space Shuttle Program, and the new generation of explorers in Artemis’ endeavors to land the first woman and first person of color on the Moon, the people of Michoud have always prided themselves in their place in history. It’s a multigenerational facility where tradition means an unwavering commitment to the success of the mission.
Keller, a Manufacturing Technical Solutions employee, supports Michoud through Marshall’s Office of Strategic Analysis & Communications.
Take 5 with Lakiesha Hawkins
By Daniel Boyette
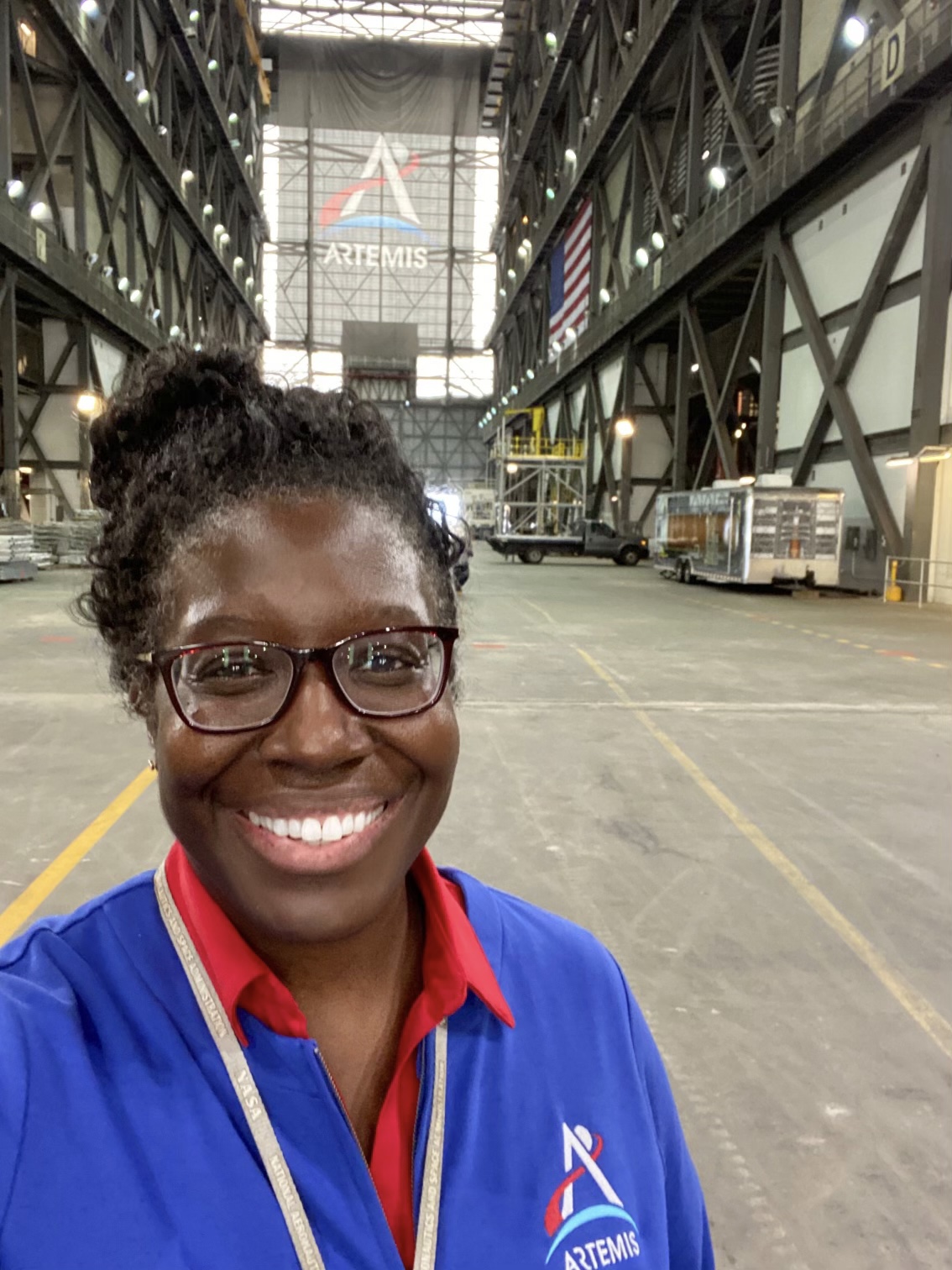
A little encouragement can go a long way. Lakiesha Hawkins, deputy manager of the Human Landing System program at NASA’s Marshall Space Flight Center, found that out first-hand.
Hawkins was attending Florida A&M University in Tallahassee in the mid-1990s when a mentor, who was working with the Space Shuttle Program, urged her to consider studying propulsion and to apply for opportunities at the school.
“I am a NASA engineer today because of that mentor,” Hawkins said. “I remember him saying I could do it, and I believed him.”
Because of that experience, Hawkins has volunteered time to mentor students and young professionals.
“That has been a significant part of my life because I know that having a mentor speaks to an individual’s potential and can change the course of a young person’s career,” she said. “I have experienced many positive turns in my journey through the power of mentoring, so I feel an obligation to pay it forward.”
Question: How do you encourage teamwork, collaboration, and integration, especially in this unprecedented telework environment?
Hawkins: The last year and a half has been unlike any challenge we’ve ever experienced. Encouraging teamwork, collaboration, and integration has had to be more intentional with a dispersed team. I have missed the natural breaks that in-person meetings afford and the informal interactions of seeing one another in the halls. To address this, HLS has been intentional about holding virtual one-on-one check-ins with team members as well as virtual coffee breaks via Microsoft Teams. Because HLS is a multicenter team, the virtual environment has, in some respects, allowed more inclusiveness because scheduled meetings have taken the place of water cooler problem-solving where those not physically present may have missed out in the past.
Question: How are you managing your personal and your team’s work-life balance, especially now, more than a year into the COVID-19 pandemic?
Hawkins: Working from home, it’s challenging to turn the workday “off” at the end of the day. I have designated a defined work area so at the end of the day, I can step away from my computer, close the door, and transition to time with my family. Getting outside and setting aside time for social interaction has also helped me to maintain a healthy balance. I find myself frequently reminding members of my team to prioritize a work-life alignment that is best for them.
Question: What key partnerships are your team pursuing to help NASA build and develop a sustainable presence on the Moon? Help push the boundaries of science, technology, and/or human exploration?
Hawkins: For the Artemis mission, establishing a sustainable presence on the Moon will take partnerships across the agency, with industry, academia, and with international stakeholders. The HLS program has embraced the partnership philosophy by bringing together the best of industry and its innovative approaches, with the agency’s deep technical expertise, experience, and commitment to crew safety. We have implemented a collaboration strategy where NASA discipline experts provide in-line support to contractor designs, working side by side with our provider teams to develop the next lunar landers.
Question: How does your team honor and demonstrate NASA’s commitment to creating a diverse and inclusive environment?
Hawkins: The HLS team is committed to a diverse and inclusive environment. To land the first woman and first person of color on the lunar surface, we have engaged a diversity of disciplines, perspectives, and experience levels across all NASA centers. With such a challenging mission, we celebrate the team with program, center, mission directorate, and agency recognitions. Our program manager, Lisa Watson-Morgan, and her management team have also established a “flat” organization where leaders are accessible and encourage the team to share great ideas, no matter where they may originate from.
Question: Why do you think your team is successful at staying mission-focused?
Hawkins: The HLS team has been successful so far because each of us is committed to the challenging objective of returning Americans the Moon. To achieve this, the HLS program has adopted a risk-based approach to program leadership where we allow highest safety, technical, and programmatic risk areas to drive our efforts and resources. Every process and requirement has bought its way into the program, ensuring our energies are targeted towards achieving our goal. The team communicates frequently to remind each other of the extraordinary yet attainable goal we are striving to achieve.
Boyette, an LSINC employee and the Marshall Star editor, supports Marshall’s Office of Strategic Analysis & Communications.
Former Astronaut Andrew Allen: People Who Care Vital to NASA’s mission
By Wayne Smith
Employees at Marshall Space Flight Center and other NASA centers turn fiction into reality with their work. And a vital element toward accomplishing their mission is people caring about what they do.
Former astronaut and space shuttle commander Andrew Allen delivered those overarching messages Oct. 21 in the Mission Success in in Our Hands virtual lecture series, the final forum for 2021.
Allen called his experience as an astronaut the “greatest opportunity I would think anyone could ever have.”
As NASA prepares for the next generation of deep space exploration with the Artemis program and the Space Launch System, Allen used his experience as a space shuttle commander, as well as a manager for ground operations support, to stress the importance of everyone involved with that mission.
“You are part of a group of people that makes the impossible, possible,” said Allen, a former Marine Top Gun pilot and senior NASA executive. “You’re part of a group that turns fiction into reality.”
Allen, now CEO at Aerodyne Industries in Cape Canaveral, Florida, recalled telling his grandmother about his selection as an astronaut and her initial reaction of saying the Moon landing wasn’t real.
“We have a lot of people who lived through such technology changes in our lives,” Allen said. “Who would have ever thought that the computing power we have on our iPhones is way more than the five general purpose computers we had on any of the space shuttles.
“The real intelligence is the people who make it all work. Whether I came across people at Marshall, or Johnson (Space Center), or Kennedy (Space Center), the level of effort that people put into making the flights successful, that workforce talent that is out there is just phenomenal.”
In sharing his experience on safety, operational excellence, and workforce performance, Allen said ensuring all links in the chain remain unbroken can be the difference between mission success and catastrophe.
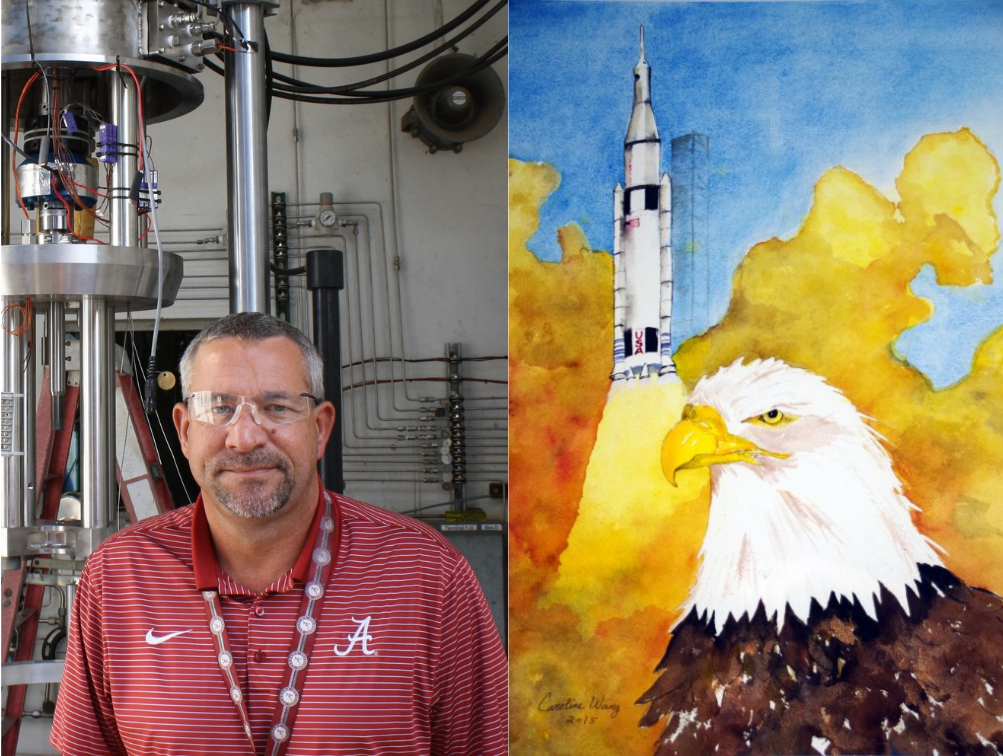
He said caring is the key word for him when talking about workforce performance, whether it’s related to maximum productivity, efficiency, or quality control.
“One of the things that struck me was hearing about back during Apollo and President John Kennedy visiting the center and coming across a janitor and asking him what he was doing. His answer was, ‘I’m helping us put a man on the Moon.’ That meant that he cared, was enthused and was feeling like part of the team.”
Allen also discussed potential detractors of mission success, including schedule pressures, unrealistic expectations, risk acceptance, and economics.
He told Marshall workers that, while there is a lot of work to be done, “you are the people who will get us there.”
“Somebody much, much younger than me is going to be the first person to walk on Mars,” Allen said. “You are some of the key folks who will make that happen.”
The Mission Success is in Our Hands initiative is a campaign led by Marshall’s Safety and Mission Assurance Directorate and partner Jacobs Engineering that promotes and strengthens Marshall’s focus on mission, hardware, and crew safety.
Smith, a Media Fusion employee, supports Marshall’s Office of Strategic Analysis & Communications.
NASCAR Engineer Richie Parker to Speak at Disability Employment Awareness Month Event Oct. 28
By Rick Smith
NASA’s Marshall Space Flight Center and its partners will welcome motivational speaker and NASCAR engineer Richie Parker on Oct. 28 to commemorate National Disability Employment Awareness Month. The national theme for this year’s observance is “America’s Recovery: Powered by Inclusion” – and Parker richly embodies that philosophy.
A former vehicle motor engineer for Hendrick Motorsports, Parker was born without arms. Nonetheless, as a child he learned to ride a modified bicycle, taught himself to write with his feet, and zealously pursued his passion for automotive engineering, which led him into the world of NASCAR. After earning a master’s degree in business from Clemson University in South Carolina, he went on to co-found Optimech Solutions, a company that provides mechanical engineering solutions to industry firms around the world, and today speaks to executives and workers around the nation about the value of hiring individuals with disabilities.
Parker’s virtual address will be live via Webex beginning at 11 a.m. Details on how to participate in the virtual event are available on Inside Marshall.
Marshall Disability Program manager Natasha Stanton, an equal employment opportunity specialist in the center’s Office of Diversity and Equal Opportunity and leader of the employee resource group, said the group seeks to “pursue positive actions that address underrepresentation in equity, fairness, and diversity in Marshall career development opportunities.” She encourages all employees to join the Oct. 28 session.
“It’s not necessary to have a disability to be part of this team of motivated, caring individuals,” she said. “Many of us at Marshall have co-workers, family members, or friends who have disabilities or identify as part of that community. Finding opportunities like these to show support, to seek new avenues of understanding and advocacy, are at the heart of inclusiveness – and have always been the bedrock of Marshall’s success.”
Widening that circle of participants is a key goal of Marshall’s Diversity Employee Resource Group as well, said Michael Effinger, a project manager in Marshall’s Science and Technology Office. He said the chance to advocate for persons with less easily recognized disabilities compelled him to join the group.
“Three members of my engineering team are colorblind, unable to discern shades of red or green,” he said. “They requested we modify the way we marked up charts and documents to better enable them to respond to changes, ensuring more efficient turnaround of technical schematics and documents.”
Effinger said he was grateful for a teammate for speaking up. “If we don’t know, we can’t make improvements. It hadn’t occurred to me that something as simple as reformatting tracked edits in a Word document or using different kinds of pens to revise technical charts could dramatically improve a teammate’s workflow,” he said.
Marshall materials engineer Craig Moore, who is blind, said normalizing such changes to the way Marshall conducts business is part of what drew him to join the group as well.
“Accessibility is a broad topic, and it’s fairly easy to alter our routine to accommodate all parties,” he said. “That may mean using descriptive text to identify contents of a graphic for visually impaired persons, for example, or changing the rate of blinking cursors to avoid the risk of seizures for individuals who suffer from epilepsy or similar disorders.”
Recognizing these disabilities is are among the first steps to building a more inclusive and efficient workplace, Stanton noted – and that takes open, positive discussion.
“Not every disability is visible,” she said. “It’s our goal to find ways to clear those unanticipated obstacles, making every team member as successful as they can be to better guarantee the same for NASA’s mission.”
The Disability Employee Resource Group currently holds a monthly virtual meeting to discuss issues and to suggest potential improvements across the center. The group will assist with collection and interpretation of data and promote developmental and advancement activities and community outreach; plan and implement special emphasis program activities; provide insight into barriers to workforce recruitment and selection; and propose solutions to specific challenges or issues relevant to the community of persons with disabilities.
Stanton also credits the support and direction of the Office of Diversity and Equal Opportunity leadership – Director Loucious Hires and Deputy Director Carolyn Magsby – with enabling and championing these efforts. She is working to update the Disability Employee Resource Group’s formal charter and soon will have resources available on Inside Marshall. All Marshall team members are invited to take part in the virtual meetings; Stanton invites them to contact her for details.
Employee resource groups offer voluntary participation to network, socialize, and raise awareness of relevant issues in the workplace. They support professional development, increase awareness and education, provide platforms for the launch of programs and learning opportunities to benefit the entire workforce, and further the agency’s mission and goals.
“We all have different perspectives,” Moore said. “It strengthens our team and gives us new advantages to achieve NASA’s goals when every voice is heard – and every individual is seen.”
Marshall is hosting the Disability Employment Awareness Month event in partnership with NASA’s Kennedy Space Center, NASA’s Stennis Space Center, and the NASA Shared Services Center. Learn more about NASA resources for individuals with disabilities here, and read more about Marshall’s Disability Employment Program here.
Smith, a Manufacturing Technical Solutions employee, supports Marshall’s Office of Strategic Analysis & Communications.