This article is from the 2019 NESC Technical Update.
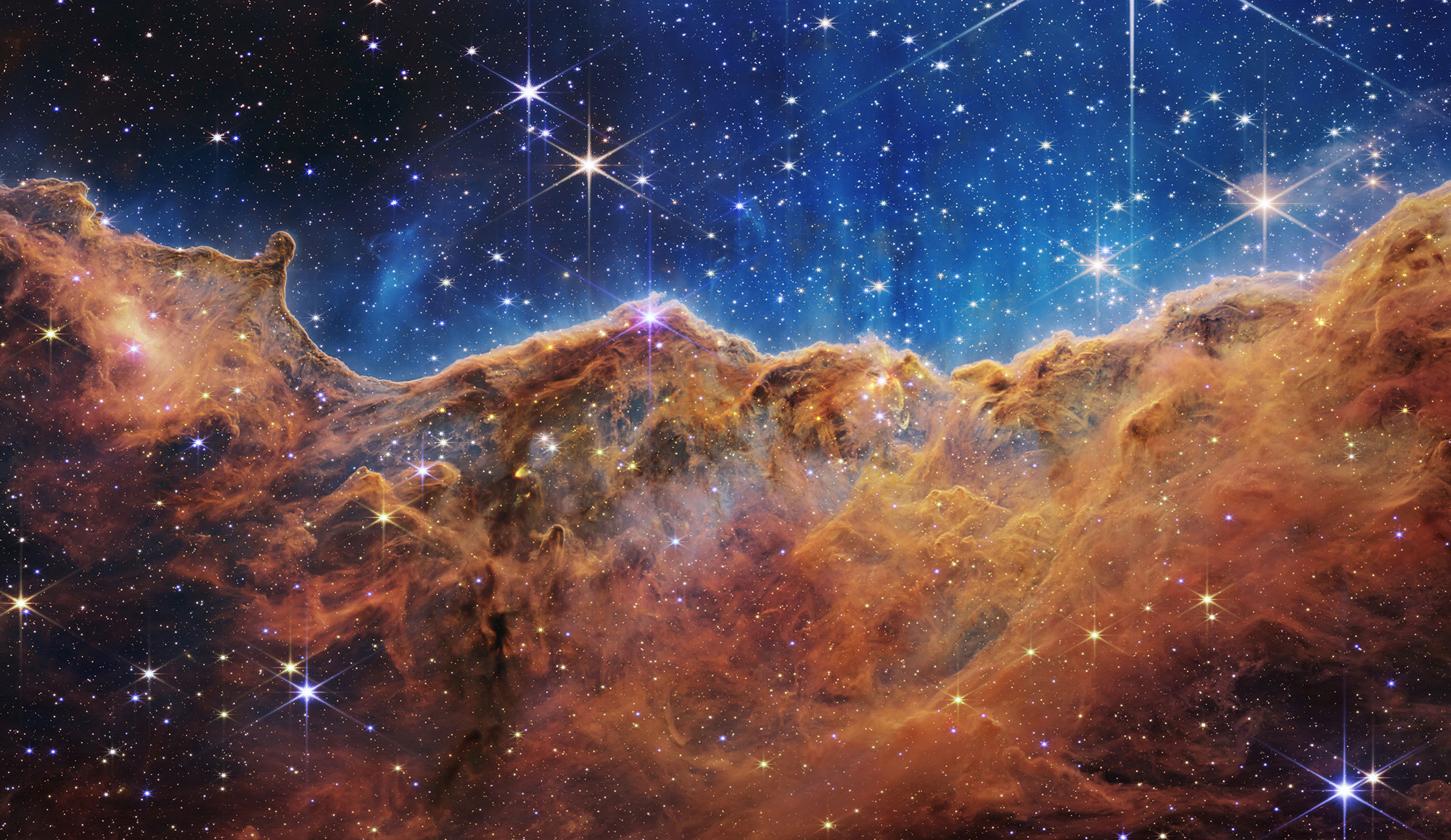
Composite overwrapped pressure vessels (COPV) are ubiquitous at NASA. Found on launch vehicles and spacecraft, they are critical containers and suppliers of propellants and the elements required for life support. The NESC has invested significant time and resources to better understand how COPVs work, and more importantly, how these complex, high-pressure storage systems can fail. Because should they fail, the consequences could be catastrophic.
“As NASA’s profile changes to more deep space missions, and in particular, deep space human missions, reliability is paramount,” said Mr. Richard Russell, NASA Technical Fellow for Materials. “If something goes wrong, there’s no safe haven or way to get back home. For deep space, reliability is the key.”
After years of study, however, some aspects of COPV behavior remain difficult to understand. “It’s a complex stress state that exists between the liner, its overwrap, and the adhesive that holds it together,” said Russell. “We need to understand not only the manufacturing process, but material compatibility, and the conditions we put them in. A lot of these questions are difficult to answer.”
Today, in many cases, COPVs are blow down systems – their pressure is reduced with use, said Mr. Steven Gentz, NESC Chief Engineer at MSFC. “COPVs used on launch vehicles leave the ground at their highest pressure, and as their contents are depleted, the pressure drops. Their use environment often is measured in minutes,” he said. “With going back to the Moon and to Mars, we will have situations where COPVs might sit at a lunar base, or in the Mars Ascent Vehicle, or a lunar orbital platform like Gateway. There will be a long-use environment measured in days, weeks, months, and even years, and we have to get comfortable that they won’t leak down or rupture.”
The NESC’s work on more than 30 COPV-related assessments has focused on test and analysis to help fill in knowledge gaps and help propel the technology forward, with the aim of ensuring their continued safety in future NASA missions.
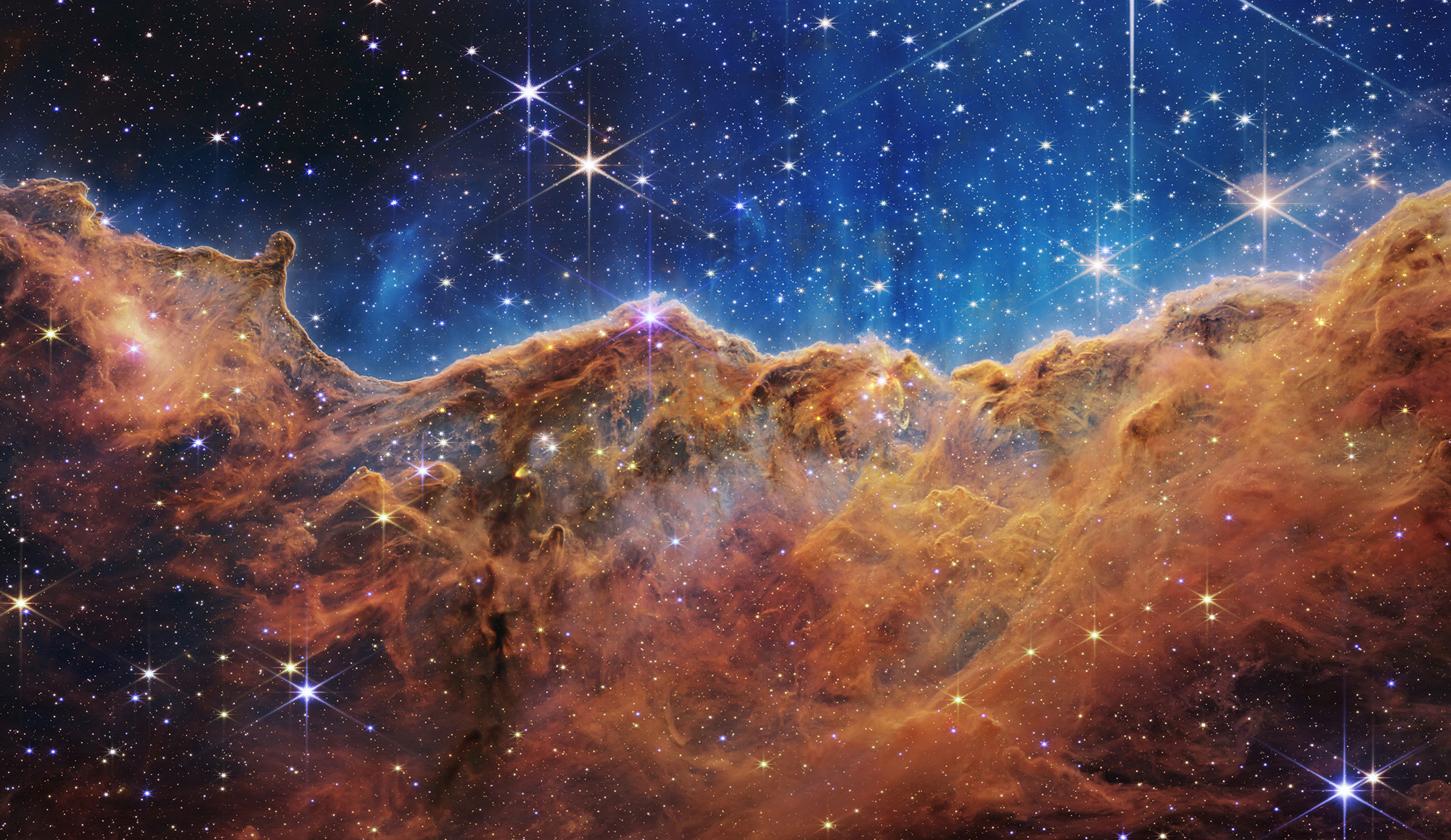
What Challenges Our Understanding of COPVs?
Designed to hold gases and liquids under pressure, COPVs typically consist of a metal or plastic liner surrounded by a composite overwrap. The liners, made from aluminum, steel, Inconel, elastomers, or plastics, serve as a permeation barrier while the composite overwrap, made from a matrix of fibers in a cured resin material, carries the load generated by its high-pressure contents. Once manufactured, COPVs go through a process called autofrettage, where the tank is subjected to high pressures to compress the inner surfaces, making them less susceptible to operational stresses later.
After autofrettage is when many questions begin. Did autofrettage affect the state of stress in the liner? Was there crack growth and will it propagate? Will current inspection methods find those cracks? What is the COPV’s tolerance to stress rupture or other failure modes?
Dr. Lorie Grimes-Ledesma at JPL leads the NESC’s Composite Pressure Vessel Working Group (CPVWG) and has studied COPVs for nearly two decades, particularly in understanding their failure modes. “The complexity of COPVs is deceptive and bleeds into all failure modes associated with these tanks. And there are failure modes we still don’t fully understand,” she said. “The cylinder section of a COPV isn’t all that geometrically complicated, but the mechanics that occur in the dome region are.”
In the dome, the liner tapers, and the way the layers of fiber wind their way over the dome can involve stops and starts and double curvatures. These geometric changes make understanding the stress and strain behavior in the dome difficult. With a three-dimensional state of stress that changes across its structure, COPV failure modes can be difficult to understand or predict. But if it fails, she said, “It will take your spacecraft down. There is so much stored energy.”
Filling in Knowledge Gaps with Tests and Analyses
To help advance COPV technology and be better prepared for long-term space travel, the NESC has been actively engaged in several activities, including a stress rupture test program and reviews of commercial provider and Orion COPVs, said Mr. Michael Kirsch, NESC Deputy Director. “We’ve also worked on the development of state-of-the-art nondestructive evaluation (NDE) techniques, and our COPV working group is actively engaged in the development of design standards for the industry.”
The stress rupture test program began more than a decade ago when concerns arose that COPVs on the Space Shuttle orbiter and the International Space Station (ISS) could be prone to failure of overwrap strands. Although typical industry approaches for stress rupture analysis had been performed prior to flight, shortfalls in the analysis methods and test data were found after a detailed review. Orbiter COPVs were reviewed using existing data, but because ISS and other Agency COPVs would be in use for longer periods of time, the NESC wanted to address some of the shortfalls in stress rupture data and analysis methods.
Specialized rigs at the White Sands Test Facility (WSTF) were built to test large quantities of fiber strands at high stress ratios and complex loading scenarios. Over several years, the NESC has collected data to develop a global stress rupture model and new methods of analysis, which have greatly reduced uncertainty in reliability predictions for ISS COPVs.
Cracks in COPV liners can also lead to rupture, and inspecting liners for cracks has become more difficult as COPVs have moved to thinner liners for weight savings, said Dr. William Prosser, NASA Technical Fellow for NDE. “This has been challenging for our NDE techniques to provide the reliable detectability of the maximum flaw sizes they can withstand.” The most commonly used NDE technique has been dye penetrant, which is placed on the liner surface to make cracks visible. “It’s a great technique, but as you get to smaller and smaller crack sizes, they get harder to visually see and less distinguishable from the background.” And once manufactured, the COPV liner interior is no longer accessible to dye.
Building on laser profilometry and eddy current flaw scanning capabilities developed at WSTF, the NESC began an assessment to design and fabricate a unique, semi-automated COPV liner external and internal inspection system. A method was needed to detect flaws like cracks, buckles, liner thickness variations, and other anomalous changes that can occur after autofrettage. Combining WSTF’s capabilities, along with a specialized rotating scanner, probe, and sensors, a 360-degree view of the vessel can now be captured by a data acquisition system. “It can follow the contours on the interior of the vessel,” said Mr. Regor Saulsberry, retired WSTF engineer who helped develop the scanner technology. “The sensors look for defects and cracks using the eddy current and laser profilometry maps the interior surface within a few thousandths of an inch. We get a high resolution view of the interior of the tank and end caps that let us see very fine defects.”
“Before, we had no way of inspecting to see if autofrettage or proof test cycles caused a crack to grow or how much it grew,” added Dr. Prosser. “Other COPV providers are interested in our technique and are pursuing adaptations for their own applications,” Dr. Prosser said. “It has had a significant impact.” The NESC has also employed NDE techniques like computed tomography to help identify buckled areas between the liner and the overwrap.
Supporting the Commercial Crew Program (CCP) as its partners develop their own COPV designs and explore new use environments has also grown the NESC’s COPV knowledge base. “CCP has made us dive into the detailed mechanics of COPVs that we’ve never needed to pursue in the past,” said Dr. Grimes-Ledesma. “But the modeling and analysis capability we’ve established over the years put us in a good place to support their COPV development.”
New designs have considered submerging COPVs in liquid oxygen (LOX) to better manage the temperature requirements of their contents, so the NESC led an assessment to understand how particular carbon fiber composite materials behave in LOX. The NESC investigations to better understand the liner material’s capability under service-like conditions resulted in a new approach to analyzing grain size in COPVs.
Another potential hazard COPVs will face on long missions in space is impacts from micrometeoroid and orbital debris (MMOD). For a short time during the Artemis I mission, COPVs located on the interim cryogenic propulsion stage will be vulnerable to MMOD. To understand the failure criteria of these COPVs, an NESC assessment team fired various-sized particles at COPVs and coupons at a WSTF test facility to simulate hypervelocity MMOD impact. “We tested in the COPV barrel and shoulder regions, varied velocity and particle make-up (aluminum and steel), and tested at different impact angles,” said Mr. Michael Squire, NESC Principal Engineer. “And we found that the tanks are more robust than originally thought.”
Prior risk assessments, based on analysis only, had assumed COPV failure would occur with penetration of the COPV overwrap. After testing, however, the NESC team determined smaller particles could penetrate the overwrap and partially into the liner and the tank would not fail. By more fully understanding the size of particle and depth of penetration required to cause a failure, the risk of failure could be more accurately calculated. “The failure risk for these tanks dropped,” Mr. Squire said. “We found when we reran the risk numbers, these tanks were no longer driving the risk for the vehicle.”
Keeping tabs on all COPV activities across the Agency, the CPVWG has helped develop COPV standards for NASA and the industry and provided consultation and expertise to answer COPV questions for NASA programs and projects. Their testing and analysis programs have significantly influenced damage tolerance life-test methods, provided data on life expectancy, and the Agency’s understanding of crack growth. “The working group is tasked with tracking COPV technology and making sure we understand how COPVs are being used and what gaps might exist in our knowledge of them,” Dr. Grimes-Ledesma said. “Because the consequence of COPV rupture is so severe, it has warranted so much work, but because we started working on very difficult and previously neglected areas related to COPV failure modes in 2006 and 2009, the NESC has been in a good position to answer questions to support Orion, commercial crew, and ISS.”
COPV Study Has Far-Reaching Benefits
Has the time, energy, and funds the NESC has dedicated to COPVs been worth it? “From an NESC perspective, having the body of knowledge to be able to penetrate the technical issues on the variety of COPVs used by the Agency has been a high return on investment,” said Deputy Director Kirsch.
“It’s been beneficial for all of our programs,” added Mr. Russell. “We want to do more things, travel further, and save weight, so it will always be a challenge. But it is worth the risk if you do it right, take the time, and analyze the risk. It’s our job to help engineering organizations inform the risk to people who have to make the big decisions. The NESC role has always been to do these difficult evaluations, tests, and analyses — to help understand the reliability of these complex systems.”
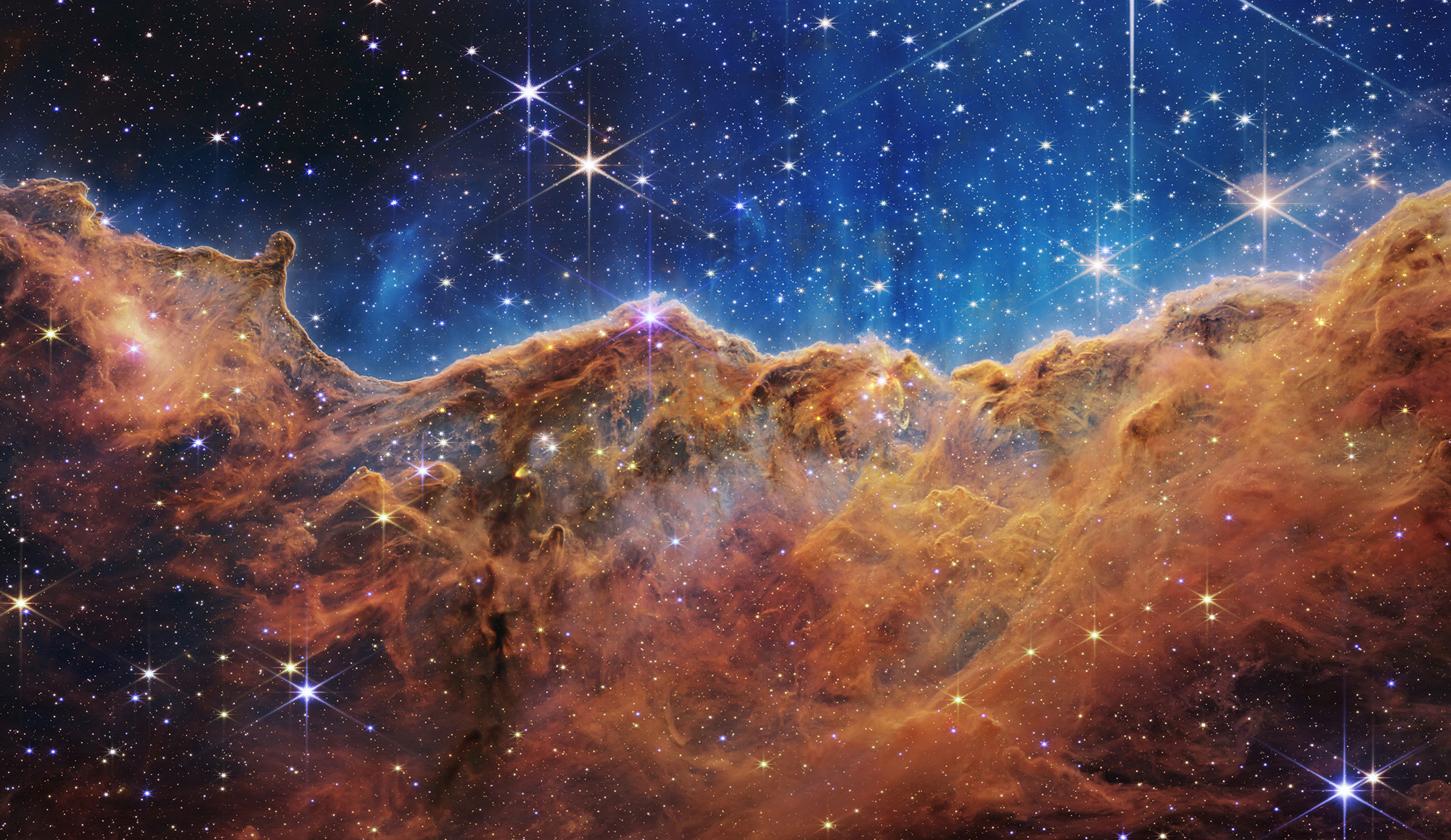