
With 14 electric motors turning propellers and integrated into a uniquely designed wing, NASA will use the X-57—its first all-electric experimental aircraft and the first crewed X-plane in decades—to demonstrate that electric propulsion can make planes quieter, more efficient, and more environmentally friendly.
Distributed electric propulsion technology is based on the premise that closely integrating the propulsion system with the airframe and distributing multiple motors across the wing will increase efficiency, lower operating costs, and increase safety.
The first of three X-57 aircraft configurations arrived at Armstrong in October 2019 for testing and preparation for initial flight tests. Dubbed Modification II (Mod II), this configuration will undergo ground tests, followed by taxi tests, and then flight tests.
A goal of the X-57 project is to help develop certification standards for emerging electric aircraft markets, including urban air mobility vehicles, which also rely on complex distributed electric propulsion systems. NASA will share the aircraft’s electric propulsion–focused design and airworthiness process with regulators and industry, which will advance certification approaches for aircraft utilizing distributed electric propulsion.
Following are highlights of recent accomplishments and a look at what lies ahead in several key areas.
Aero Database Development
Researchers at Armstrong and NASA’s Ames and Langley Research Centers have run more than 2,500 computational fluid dynamics (CFD) cases using a variety of CFD codes to support the development of an X-57 aerodynamic database. The database models the aerodynamics of the baseline X-57 vehicle and also includes aerodynamic increments from the cruise propulsors on the wing tips and the 12 high-lift propulsors distributed along the wing’s leading edge. Propulsors are modeled in CFD using actuator disks with thrust and power values derived from XROTOR models of the cruise and high-lift propellers. An uncertainty model for the aerodynamics of the vehicle was derived, in part, from the variation between the different CFD codes and was incorporated into the database. The aerodynamic database was implemented at NASA Langley, and Armstrong piloted simulations for controls analysis and airworthiness evaluations.
Systems Integration and Test Planning
The X-57 aircraft is undergoing a series of tests before the Mod II flights occur. Weight and balance tests, ground vibration tests, and post-shipment functional checkout activities will occur first. Hardware and software upgrades will be implemented to improve propulsor efficiencies, followed by a series of system-level verification tests. Off-nominal cases will be checked to ensure there are no unexpected system behaviors. Then instrumentation data will be transmitted from the vehicle to the control room during hangar radiation tests as well as combined system tests to check for electromagnetic interference and compatibility issues. For dynamic testing, a low-speed taxi test will identify any loose wiring connections at the interfaces. At the completion of these build-up tests, the X-57 aircraft will be ready for flight.
Wing Loads Testing
Following the Mod II phase, Modifications III and IV will feature a high-aspect ratio wing, compared to the wider, standard wing from the Mod II phase. The Mod III/IV wing was tested at Armstrong’s Flight Loads Laboratory to calibrate installed strain gauges for real-time loads monitoring and to verify that the wing met design specifications. The new wing will permit the repositioning of the electric cruise motors to the wingtips, which could significantly boost aircraft efficiency. The Mod IV configuration will include 12 smaller high-lift motors in addition to the two larger cruise motors on each end of the wing to produce distributed electric propulsion.
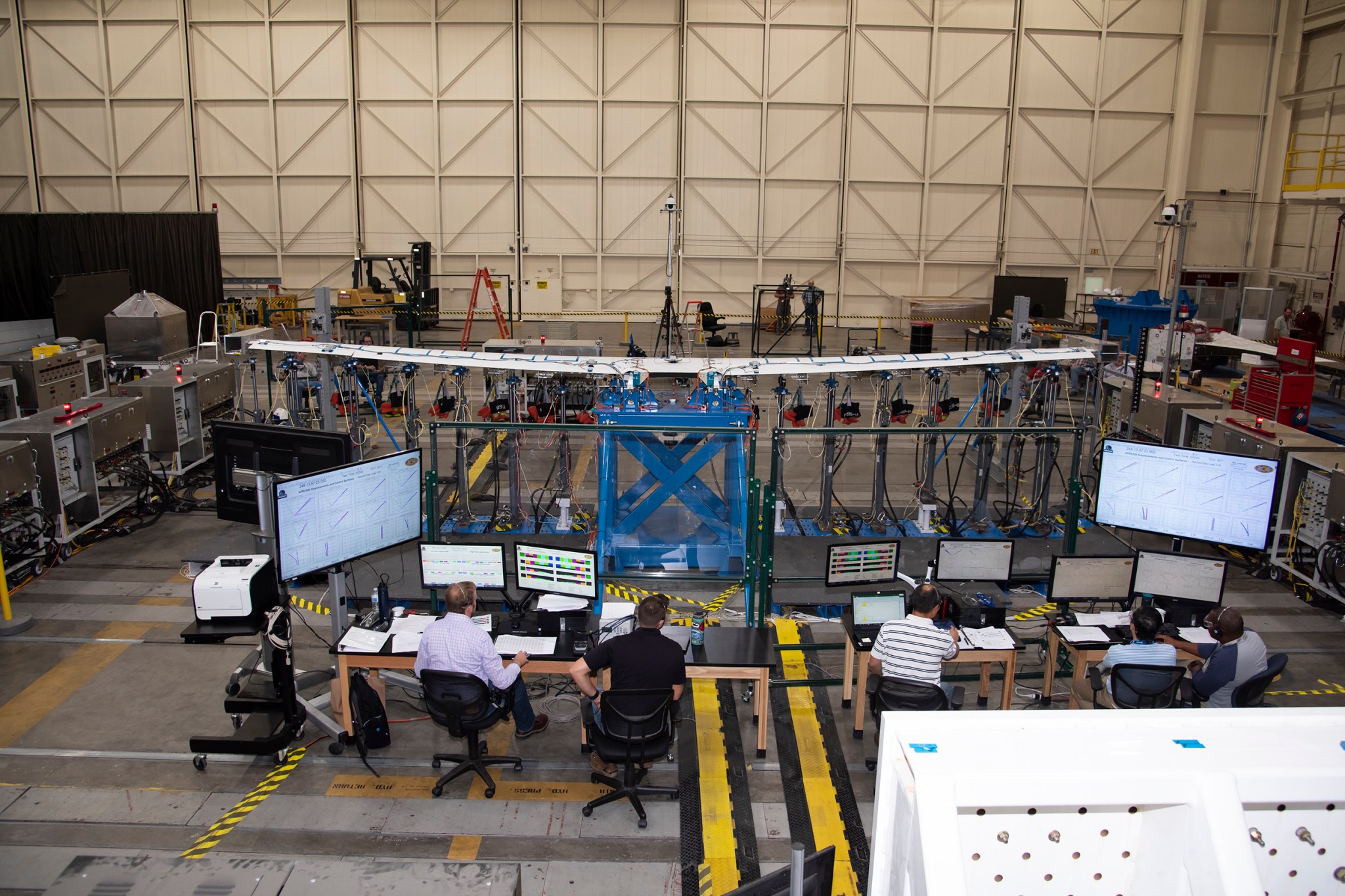
Collaborators
NASA’s Langley Research Center, Glenn Research Center, Ames Research Center, and Johnson Space Center; Empirical Systems Aerospace; Joby Aviation; Xperimental; Scaled Composites; Utah-based Electric Power Systems; TMC Technologies; and Tecnam
Benefits
- Enables cleaner flight: Electric propulsion provides a 5- to 10-factor reduction in greenhouse gas emissions with current forms of electricity generation and essentially zero emissions with renewable-based electricity.
- Reduces lead emissions: Electric propulsion provides a technology path for small aircraft to eliminate the use of 100 low-lead (100LL) avgas, which is the greatest contributor to current lead emissions.
- Improves efficiency for commuter aircraft: This research could lead to the development of an electric propulsion–powered commuter aircraft that is more efficient than today’s models.
- Reduces total cost of ownership for small aircraft: This project will demonstrate high-performance electric motors, controllers, and power delivery systems that are more reliable and easier to maintain than traditional hydrocarbon-based systems. These technologies will eventually allow aircraft to be built with reduced maintenance costs and improved reliability in flight.
PI: Sean Clarke | 661-276-2930 | Sean.Clarke@nasa.gov