As engines are fired, software written and hardware welded to prepare for the first flight of NASA’s Space Launch System (SLS), engineers are already running tests in supersonic wind tunnels to develop the next, more powerful version of the world’s most advanced launch vehicle capable of carrying humans to deep space destinations.
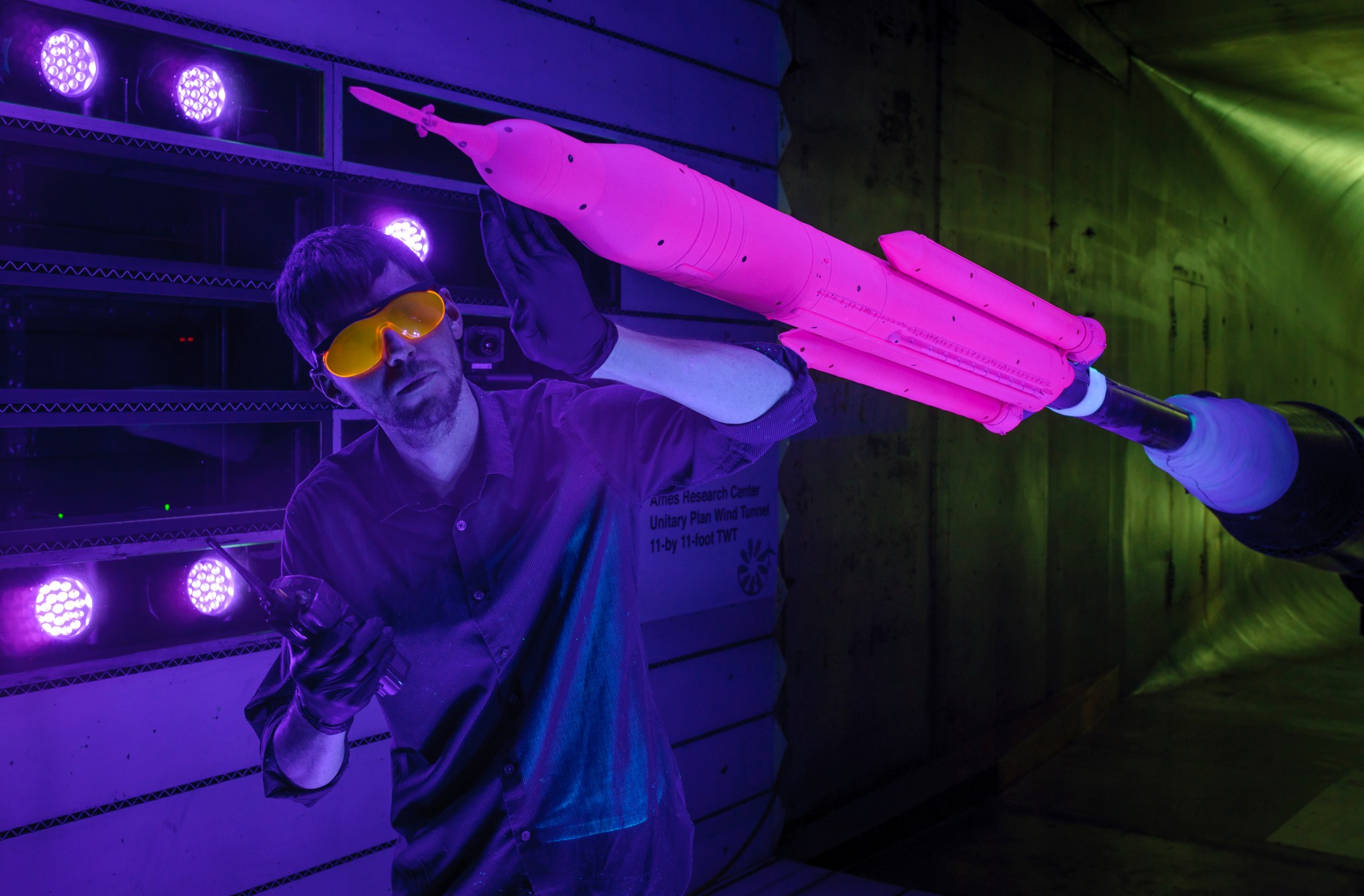
“Aeronautics leads the way in the design of a new rocket,” said Jeff Bland, SLS discipline lead engineer for Integrated Vehicle Structures & Environments at NASA’s Marshall Space Flight Center in Huntsville, Alabama. “The first leg any journey for spacecraft launched from Earth is a flight through our atmosphere.”
Manufacturing is well underway on the initial configuration of SLS. It is 322 feet tall and able to lift 70 metric tons (77 tons). For the first test flight of SLS, the rocket will carry an uncrewed Orion spacecraft beyond the moon and then return to Earth, deploying 13 small science and technology satellites in deep space during the journey.
The new wind tunnel tests are for the second generation of SLS. It will deliver a 105-metric-ton (115-ton) lift capacity and will be 364 feet tall in the crew configuration — taller than the Saturn V that launched astronauts on missions to the moon. The rocket’s core stage will be the same, but the newer rocket will feature a powerful exploration upper stage. On SLS’s second flight with Orion, the rocket will carry up to four astronauts on a mission around the moon, in the deep-space proving ground for the technologies and capabilities needed on NASA’s Journey to Mars.
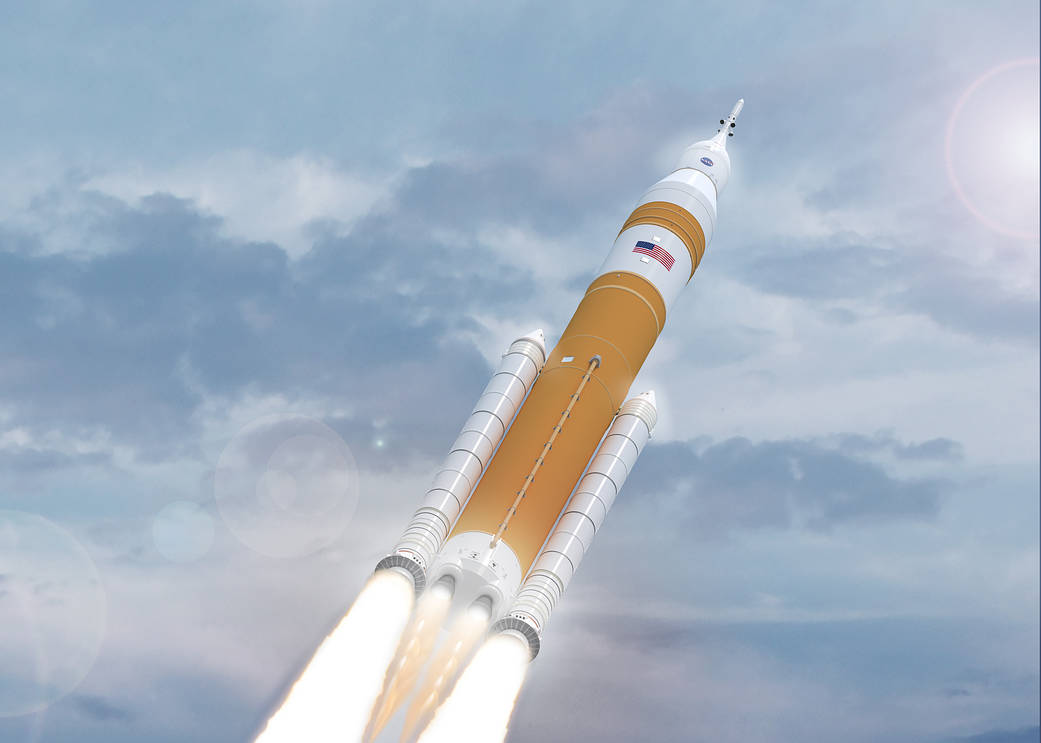
Scale models of the upgraded rocket in crew and cargo configurations are being carefully positioned in wind tunnels for test programs to obtain data needed to refine the design of the rocket and its guidance and control systems, said Dr. John Blevins, SLS lead engineer for aerodynamics and acoustics at Marshall. During hundreds of test runs at NASA’s Langley Research Center in Hampton, Virginia, and Ames Research Center in Silicon Valley, California, engineers are measuring the forces and loads that air induces on the launch vehicle during every phase of its mission.
“All the critical aerodynamic environments, from when the upgraded rocket leaves the Vehicle Assembly Building at Cape Canaveral to launch, acceleration through the sound barrier and booster separation at greater than Mach 4 are evaluated in these four tests,” Blevins said.
Ascent tests completed at Ames in November determined the rocket’s behavior as it climbs after launch, and the kind of instructions to be programmed into the rocket flight computer for guidance and control as the rocket passes through transonic flight. For instance, the tests will determine what commands the autopilot will send to the rocket’s nozzles to correct for wind or other factors and stay on course.
Buffet testing at Langley in November focused primarily on how the cargo version of the upgraded rocket behaves as it moves through the atmosphere at just below the speed of sound, approaching about 800 miles per hour, then moves into supersonic flight. As the rocket approaches the speed of sound, shock waves build and move along different points of the launch vehicle. These shock waves can cause buffeting, shaking, vibration and unsteady loads that could result in damage or course changes that must be corrected, Blevins said.
The cargo version of the upgraded rocket has a smooth fairing above the exploration upper stage instead of the Orion spacecraft and launch abort system, so separate wind tunnel testing is needed. Similar tests planned for the fall 2017 at Langley will include observing this transonic shock oscillation and buffeting on the crew version of the rocket, at both subsonic speeds and higher Mach numbers. At Mach 1.5 or 2, the waves terminate, or remain at the same points on the rocket for the rest of the flight, but they continue to change angle and strength.
These wind tunnel tests are critical, Blevins said, because the location and temporal behavior of these shock waves are difficult to predict with computational fluid dynamics — they must be observed and measured.
Two other test series are planned at Langley. The first in early 2017 will provide data to ensure that as the SLS’s two solid rocket boosters separate from the rocket during ascent, they don’t come back into contact with the vehicle. These tests are complex, Blevins said, because the models of the rocket’s core stage and each of the two boosters are separately instrumented, and even the dynamics of the small rocket motors that jettison the boosters are simulated.
Next will be liftoff transition testing, scheduled in the summer. These tests will include evaluation of the effects of winds on the rocket as it is waiting on the pad, and the presence of the mobile launcher and tower during liftoff. Drift of the vehicle as it moves past the tower must be controlled to avoid damage and because the sound bouncing back from the pad can cause damaging vibration.
“We expect that at the end of this test series we will have all the aerodynamic flight data needed for the upgraded rocket,” he said. “We’ll be ready for the first flight with crew, targeted as early as 2021, and subsequent flights.”
NASA engineers have also teamed with CUBRC Inc. of Buffalo, New York, to use a special type of wind tunnel to better understand and analyze how the SLS heats up as it ascends into space. A model of the rocket was used in the first phase of aerodynamic heating tests in CUBRC’s Large Energy National Shock Tunnel (LENS-II) in September. A second phase of testing is planned for models of the SLS in crew and cargo versions, in early 2017.
The SLS wind tunnel testing is very much a cross-agency effort resulting in information and new test techniques that also benefit other rocket and aerospace programs, said Dr. Patrick Shea. He’s based at Langley, but served as SLS aerodynamics test lead for the transonic ascent testing recently completed at the Ames facilities.
For example, the Ames aerodynamics team is developing an optical measurement method involving Unsteady Pressure-Sensitive Paint. During a test, special lights and cameras will observe changes in the paint’s fluorescence, indicating the strength of aerodynamic forces acting along different areas of the rocket or test article. Ames was able to take advantage of the presence of the SLS rocket model to conduct its own tests using the paint.
“For a lot of aero-acoustics and buffet work, we instrument the models with hundreds of pressure sensors. If we can start moving to more of an optical technique such as the dynamic pressure sensitive paint, it will really make good strides forward,” Shea said. “It ended up being a really nice integration of their test technique and our test campaign.”