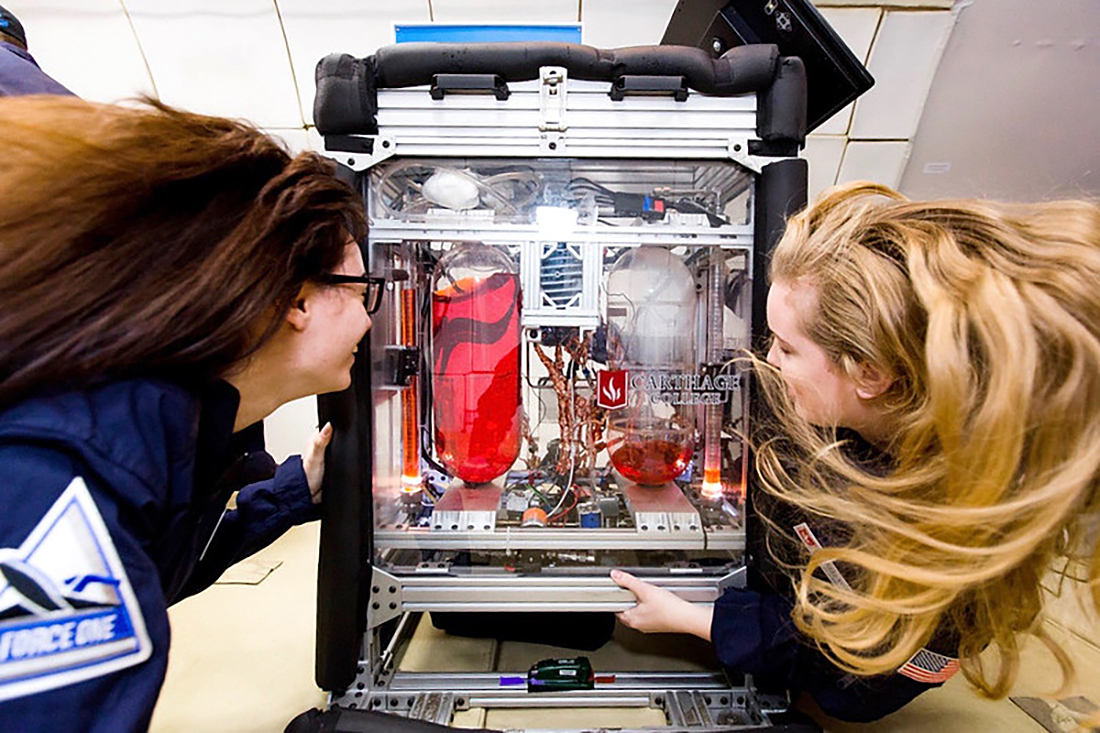
Rocket off course? It could be a slosh problem.
Propellant slosh, to be exact. The motion of propellant inside a rocket-based launch vehicle or spacecraft tank is an ever-present, vexing problem for spaceflight. Not only can it make gauging the amount of available propellant difficult, but the volatile waves of liquid can literally throw a rocket off its trajectory.
“To understand why it’s such a critical issue, it’s important to realize that for most launch vehicles, liquid propellant initially makes up nearly 90% of the vehicle mass,” explained Kevin Crosby of Carthage College in Kenosha, Wisconsin.
Crosby is the principal investigator for a slosh control system supported by NASA’s Flight Opportunities program. The innovation will be tested on flights in Nov. 2020 from Zero Gravity Corporation on the company’s G-FORCE ONE modified parabolic airplane, which provides brief periods of microgravity.
“As propellant is used over the course of a mission, room becomes available in the tank for it to slosh,” said Crosby. “And every time you fire an engine, it creates intense vibration and even more potential for the liquid to be disturbed.”
Crosby explained that without any slosh mitigation, the risk of losing control of the launch vehicle can increase dramatically.
While many slosh suppression methods already exist, Crosby noted that most can only be used in spherical tanks. Lower-mass and lower-cost options are needed for the cylindrical tanks often used in rocket-based launch vehicles.
To address the challenge, Crosby – along with co-investigator Sathya Gangadharan of Embry-Riddle Aeronautical University (ERAU) in Daytona Beach, Florida, and students from both institutions – are testing a method that attempts to control slosh by using magnetic forces. Prior to the current parabolic flight campaign, Flight Opportunities funded testing of the technology on earlier parabolic flights in November 2019.
The technology, called the Magneto-Active Slosh Control System, consists of a patented diaphragm with a magnetic membrane encased in a polymer mesh. The device is positioned in a cylindrical propellant tank, free floating on the surface of the propellant. Magnetic coils are placed on the outside of the propellant tank, and that magnetic field causes the diaphragm to stiffen, helping to hold propellant on one side of the device.
“In microgravity, magnetic forces steer the membrane through the liquid and exert forces on it, which allows the system to suppress slosh before it gets going,” explained Crosby.
On the parabolic flights in November 2019, Crosby and team tested the system by manually switching between different magnetic fields to assess the technology’s effectiveness in responding to varying levels of slosh. On the upcoming parabolic flights, they’ll test it using software and hardware rather than manual control.
“That’s the beauty of the Flight Opportunities program — we can test one aspect of this work and then fly again to test the next stage,” said Crosby. “We know this works in our current experiment set-up, but moving forward, we need to scale it to larger vehicles to see if it is practical for spacecraft. And these parabolic flights are a critical stepping stone to that.”
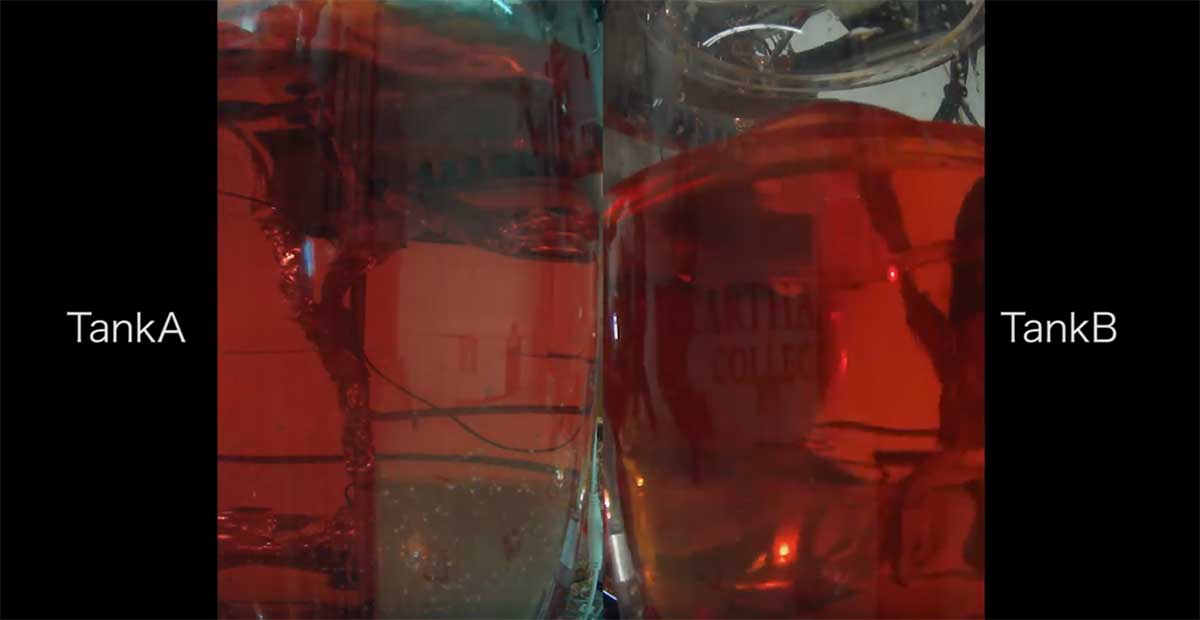
The flights have also proven to be a valuable pathway to further research and careers for Carthage College students and their peers at ERAU. Students have gone on to jobs at NASA and with aerospace companies, to prestigious graduate programs, and used their flight experiment results in Ph.D. dissertations.
“Being able to learn about space science research while experiencing microgravity itself solidified my desire to pursue a research career in this field,” said Celestine Ananda, a Carthage College recent graduate with several suborbital flights on her resume. “I’m starting a Ph.D. program in aerospace engineering this fall, largely due to my research experience funded through the Flight Opportunities program.”
The flights have also enabled Carthage students to test the college’s related propellant gauging technology. This mission-critical need for determining the amount of propellant left in a tank is made more difficult by slosh – and it becomes increasingly important at the latter stages of a mission (e.g., when returning to Earth from a trip to the Moon), when there is very little margin for error.
Testing the technology on NASA-supported parabolic flights from 2011-2018, as well as a 2019 flight on Blue Origin’s New Shepard rocket-powered system, enabled Crosby and his students to demonstrate high accuracy for gauging unsettled liquids in propellant tanks – the level of accuracy required for NASA’s Orion spacecraft and Space Launch System rocket.
“Each flight gives the students such a unique laboratory experience that they just wouldn’t be able to get otherwise,” said Crosby. “And for them to be able to work on a project that has the potential to help NASA or commercial launch vehicle providers address mission-critical needs is an amazing opportunity for them.”
Other Technologies Aboard G-FORCE ONE
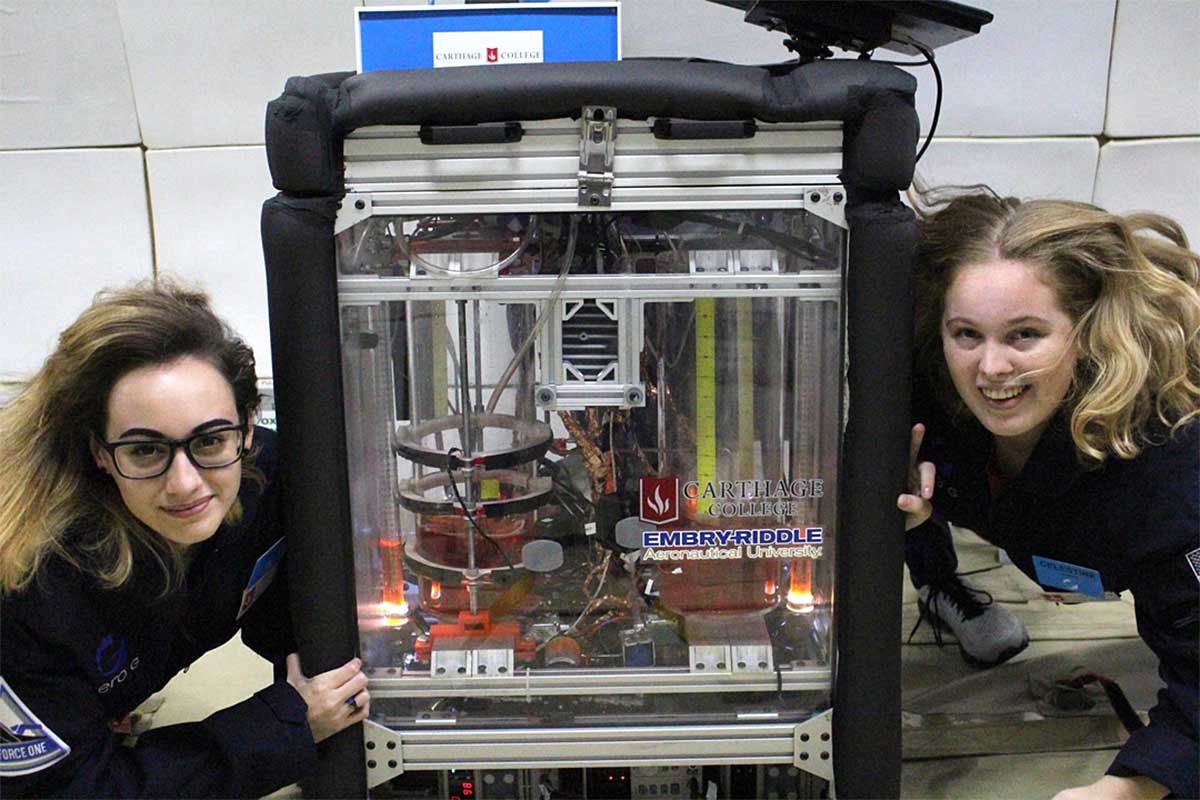
The other innovations being tested aim to provide important capabilities for future NASA missions, including:
- Evaluating preserved blood for potential space-based transfusion therapy: Researchers from the University of Louisville will attempt to show that dehydrated red blood cells can be adequately rehydrated and regain viability and function in reduced gravity.
- Advancing a space-based bioreactor: Rensselaer Polytechnic Institute researchers will test a ring-sheared drop technology for potential use as a containerless bioreactor, studying the growth and behavior of E. coli and several species of algae. Researchers at NASA’s Marshall Space Flight Center in Huntsville, Alabama, are also using a modified version of the hardware to perform engineering development tests in advance of an International Space Station experiment.
- Fabricating compact life support systems on the Moon: Researchers from the University of Colorado in Boulder are evaluating a direct writing technique for additive manufacturing of efficient structures using multifunctional composite materials.
- Improving condensation efficiency: University of Missouri researchers are testing electrowetting enhanced dropwise technology to automate removal of condensation droplets from spacecraft surfaces as they form.
- Evaluating metal foam-based 3D printing: West Virginia University researchers are testing a series of metal oxide foams for potential use in space-based additive manufacturing.
- Refining surface sample collection methods: Researchers at NASA’s Jet Propulsion Laboratory in Southern California are testing a dual rasp sampling tool with rotating heads that designed to cut through compacted lunar or planetary surface soil and guide it into a sampling cup.
- Monitoring spacecraft surfaces, water systems, and crew health: JPL researchers are also evaluating an automated device that aims to provide microbial monitoring and is designed to extract DNA from six biological samples simultaneously.
- Producing optical fiber in orbit: Physical Optics Corporation researchers are testing the ability of their low-power, compact, ruggedized system for producing ZBLAN optical fiber to reliably initiate an automated draw process in reduced gravity.
About Flight Opportunities
The Flight Opportunities program is funded by NASA’s Space Technology Mission Directorate at the agency’s Headquarters in Washington, D.C. and managed at NASA’s Armstrong Flight Research Center in Edwards, California. NASA’s Ames Research Center in California’s Silicon Valley manages the solicitation and evaluation of technologies to be tested and demonstrated on commercial flight vehicles.
By Nicole Quenelle
NASA’s Armstrong Flight Research Center